Introducing
RITSUO SHINGO IN ROMANIA
Learn the best practices from the Toyota Production System (TPS)
Boost your management skills to increase your company performance
3 SIMPLE REASONS TO ASSIST:
“Learn the TPS principles to enable high performance for your company”
“To practice the behaviors of a true Lean leader with a former Toyota Executive”
“To develop management skills that can only be achieved by intensive practice and coaching in the shop floor (Gemba)”
SAVE THE DATE
- days
- hours
- minutes
- seconds
WHERE/WHEN:
Arad, Romania
December 8-11, 2015
Host plant: Takata Seatbelts Arad

Ritsuo Shingo: Former Executive President Toyota China & Hino Motors
- Ritsuo Shingo started his career with Toyota Motor Company in 1970 and retired in 2012.
- His father, Dr. Shigeo Shingo is a renowned expert in improving manufacturing processes, who helped to develop many aspects of the revolutionary manufacturing systems which comprise the Toyota Production System.
- He helped in the start up of five Toyota manufacturing plants outside Japan.
- Ritsuo Shingo spent more than 13 years in various roles at Toyota in Legal, Public relations and purchasing departments.
- He spent 5 years in the US, starting up Toyota Detroit Office as a purchasing agent and at Toyota Motor Kentucky.
- He worked also at Toyota Motor UK and then returned to the China Dept. in Japan.
- In 1998, had newly established the Toyota first Joint Venture in China, “Sichuan Toyota Motor” and became the first president of the Joint Venture.
- In 2007, had newly established the Joint Venture between Hino Motors and Guang-Qi Motors and became the first president of the Joint Venture.
Training Details
Some of the best companies have hosted this training
Mercedes Benz, Celestica, Magna Powertrain, Rockwell Automation, SKF, Kimball, among others.
Ritsuo Shingo at Kimball Electronics
Ritsuo Shingo at Mercedes Benz
Ritsuo Shingo at SKF
Ritsuo Shingo will share his perspective from all the experiences of his long life in the Automotive Industry, with over 40 years experience in the Toyota Management System, in different leadership roles.
Participants will have the opportunity to access first hand information about Lean leadership and the best practices for a successful culture development.
The workshop will deal with TPS principles applied to manufacturing environments, which has a highly dynamic approach, with over 70% of the time in shop floor real application.
Aimed to: Senior Leadership, Functional Managers (HR, Finance, Sales..), Operations Managers, Lean Practitioners.
Training Length & Language: 32 Hours (4 Sessions) – English
Recommended Industries: All kind of Manufacturing (Automotive, Aerospace, Food, Plastics, Electronics, Construction…)
Limited Seating & Requirements: Seating is limited to 15 external participants, who could be from the same industry but not from a direct competitor company.
Classroom Lecture
Gemba Activity
SMED Explanation
TRAINING AGENDA: BODY OF KNOWLEDGE
Ritsuo Shingo Presentation (8:00 – 8:30)
Concept of 4S – Gemba Activity (8:30-10:30)
Waste (Muda) Identification – Gemba Activity (10:30-12:50)
Lunch: 13:00-13:30
Problem Solving & finding – Gemba Activity (13:00-15:20)
Standardization – Gemba Activity (15:20-17:40)
Total Participation – Gemba Exercise (8:00-10:30)
Autonomation / Build in Quality – Gemba Exercise (10:30-13:00)
Lunch: 13:00-13:30
QC Circle – Gemba Exercise (13:30-16:25)
Quality Control (16:25-17:00)
Motivation of Workers– Gemba Exercise (8:00-8:30)
Visual Control – Gemba Exercise (8:30-11:00)
Leader & Leadership – Gemba Exercise (11:00-12:00)
Robbery Story – (Elevator Story) (12:00-12:10)
Never Give up – Be Challenging (12:10-12:30)
Self Evaluation (12:30 – 13:00)
Lunch: 13:00-13:30
Culture (13:30-14:00)
Gembaism (Go & watch) – Gemba Exercise (14:00-16:40)
Brain Storming – Gemba Exercise (8:00-10:40)
Category Principle (10:40-11:10)
Level Production ( Heijunka) – Gemba Exercise (11:10-12:30)
SMED System – Gemba Exercise (12:30-13:00)
Lunch: 13:00-13:30
Pull System/Push System – Gemba Exercise (13:30-15:00)
Lot Production & One Piece Flow – Gemba Exercise (15:00-16:30)
Blame responsibility/Detect cause (15:30-14:00)
Certificate/Group photo – (16:00-17:00)
Host Company: Takata Romania – Arad Seatbelts Plant
Takata is dedicated to protecting human life. We began by developing seat belts utilizing the technology found in parachutes. Since then, we continue to develop the newest safety technology and make it available globally. This has been our objective since the beginning and we will remain committed to it. Our dream is to reduce the number of fatalities of traffic accidents to zero
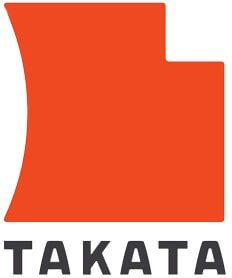
Takata began to expand outside Japan in the 1980s. At present, Takata has operating 55 plants in 20 countries such as Japan, China, United States, Romania, Mexico, Germany and Brazil to name a few.
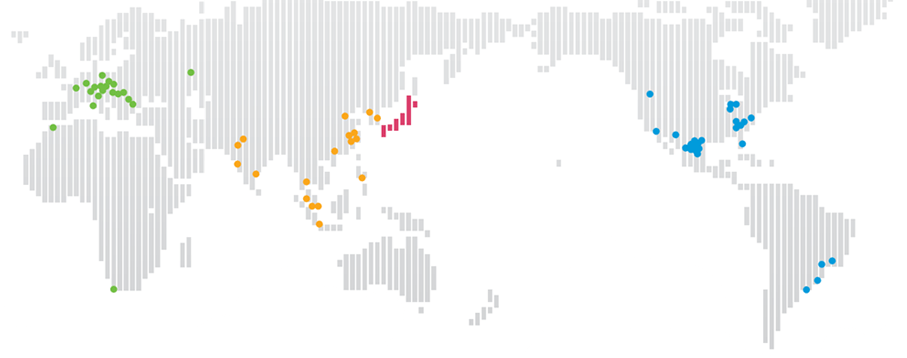
Zona Industriala Vest, str. III, Nr. 9, Arad, Jud. Arad
Our product range encompasses the full spectrum of passive and active automotive safety technology, and the results of our advanced research and relentless attention to detail can be found throughout the anatomy of a car helping to reduce the impact of traffic accidents on individuals and on society.