Hoshin Kanri (Strategy Deployment) Workshop
“Hands On Deep Dive” for management teams to perform a “Hoshin Planning” session.
Most organization’s struggle is “getting everyone on the same page and going in the same direction, this is what the Hoshin Kanri process is designed to do.
This will be a “live” session for leadership teams to participate in a “Hoshin Planning” session for their organization.
This Hoshin Kanri process is both a “top down” and “bottom up” process that leverages the power of the entire organization, not just a few leaders. It will get everyone in the organization on the same page.
The resulting alignment will get everyone going in the same direction, focusing on the “vital few” major problems in the organization.
Align & deploy actions across the organization to achieve your objectives
Participants will split into teams to perform activities and present their observations
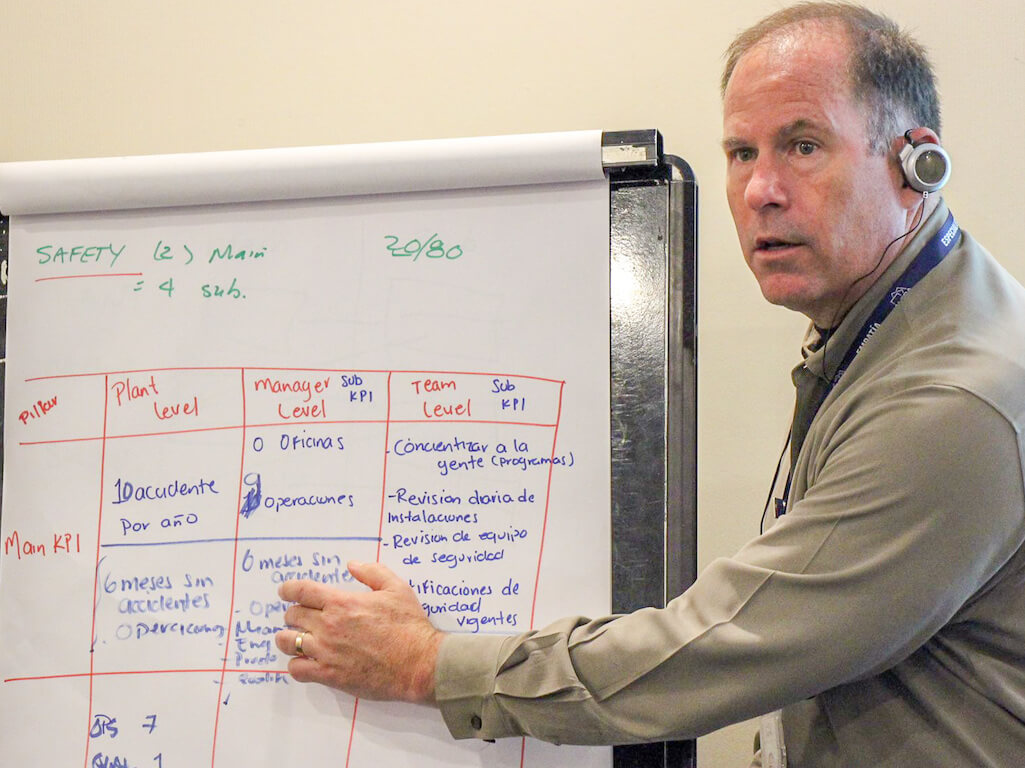
Practical Learning
Learn the concepts from Toyota examples, group exercises and trainer’s experience
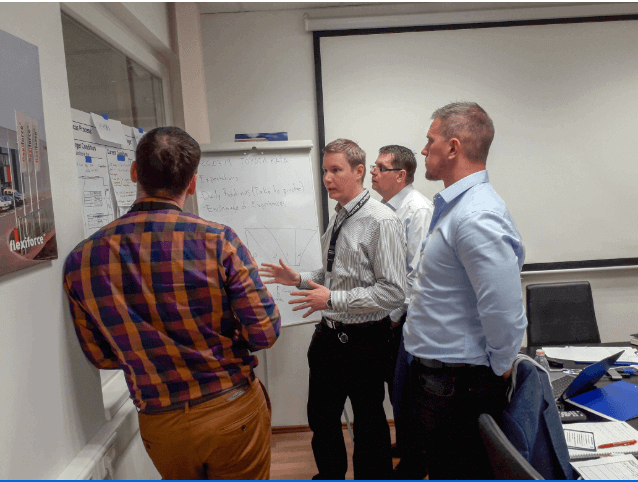
Group Discussion
Share experiences with managers from different industries and background
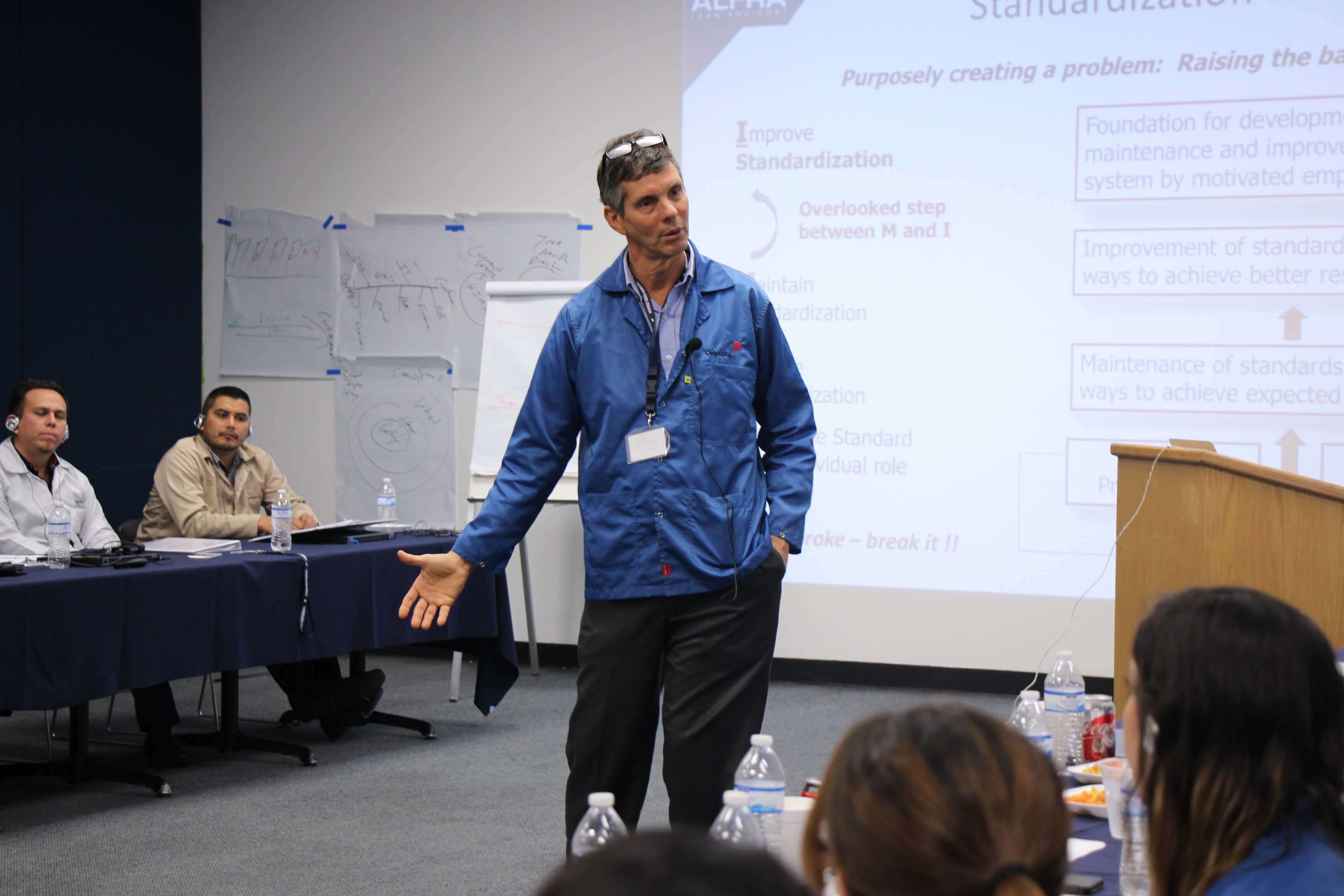
Case examples
Real cases from hoshin planning
Instructed by seasoned Lean Coaches
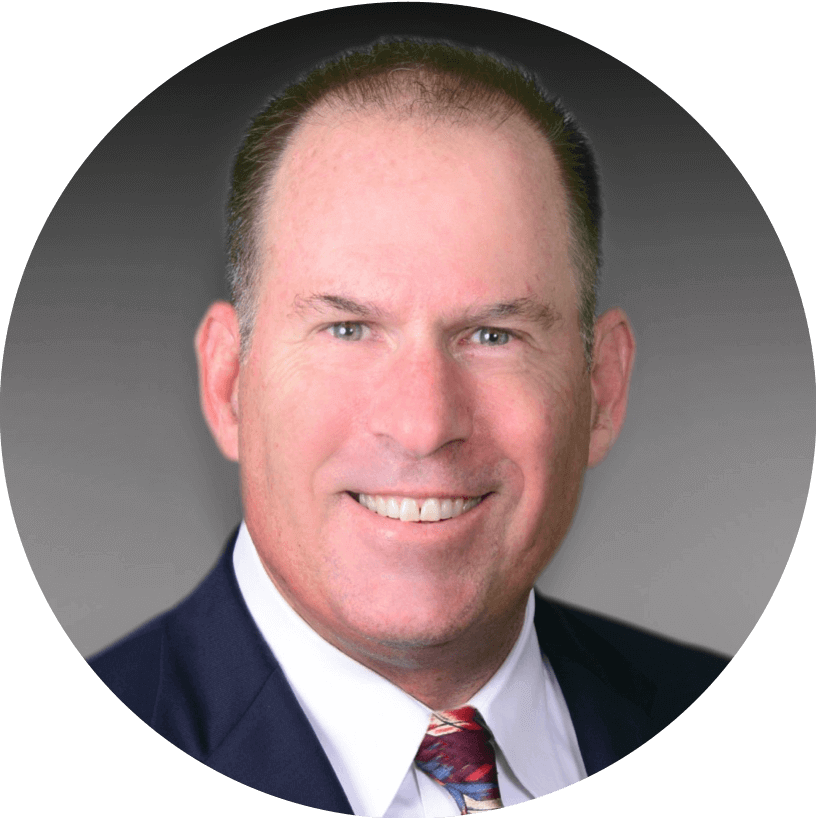
Jeff Strabala
Former Toyota Manager & Operations Management Expert
Jeff worked for Toyota for over 21 years; his extensive experience is based in Operations Management in Toyota North America as Manager and internal consultant.
Jeff was member of the Leadership team for the launch of two “Greenfield” automotive plants and subsequent plant capacity expansions valued in $4.2 billion USD. During his tenure at Toyota, Jeff also spent 3 years of “internal consulting” with improvement projects at Toyota and Tier 1 suppliers.
Project General Manager (Consultant) – Toyota OMDD
- Internal consulting position, Investigation, Analysis, and Improvement of floor operations applying core Toyota Production Systems tools.
Project General Manager – Toyota North America.
- Improved Safety Systems for Toyota’s MS manufacturing plant through active initiatives to educate plant personnel revise and introduce new programs, establish management accountability through daily reporting and monthly performance meetings, introduced gated safety management process that reduced TIR by 50% within 6 months.
- Developed, Validated comprehensive [all functions] Safety Metrics during 2013 New Generation Corolla launch, resulted in improved safety KPI during launch, Metrics, tracking and reporting adopted in North American Region.
Assistant General Manager-Toyota
- Responsible for Plant Manufacturing Operations, member of Executive Team,
Primary responsibility for Production Control, Supply Chain & Logistics, Project Management for 8 Model changes, Plant Manpower Productivity planning and reporting. - Supported Toyota Production System training and application, and Visual Management (FMDS) roll out at TMMBC, management Mentor.
Manager, Production Control – Toyota (TMMBC & TMMI)
- Production Control Planning & Coordination of Operations for Toyota truck factory with multiple product lines 2000 -2003.
- Additional collateral duties involved management of TMMI Corporate Strategy and Reporting, TPS Training Group, Manpower Planning and Productivity group.
Manager Accounting & Finance, Toyota TMMI
- Started up Accounting & Finance operations for Greenfield Toyota plant in Indiana, responsible for accounting, internal and government compliance, budgeting and cost reduction efforts.
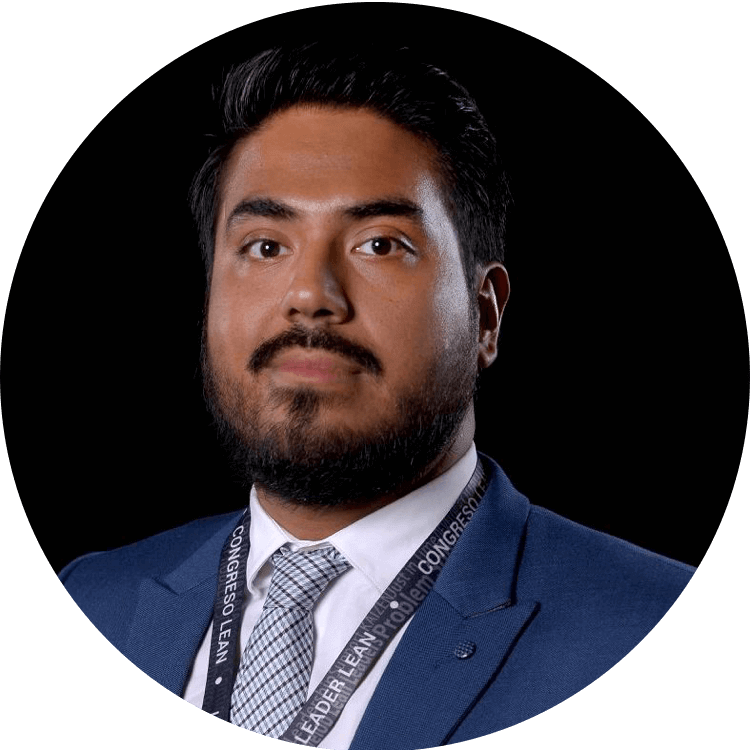
Edgar Cardenas
Lean Advisor & Coach – Europe Operations Director
Edgar has worked the last years in countries like Romania, Hungary, Russia, Mexico, Colombia, Spain and USA…, providing support to companies on their improvement journey based on developing teams to improve the quality of people & processes, in several industries including: Automotive, Electronics manufacturing, Food & Beverages, Plastics, Shared Service Centers, logistic services, among others.
He recently provide support to companies like Bosch, Hino Motors, Mercedes Benz, Kimball, Zebra technologies, Takata, Inteva Products, Dawn Foods, BOA, Mars, Rubbermaid, Faist Group, Emerson, Exide, Harsha Engineers, Steelcase..
-
Lean for Business Processes corporate trainer for several companies
-
Operational Excellence speaker at several international Lean Conferences & Summits.
-
He has developed in Lean Management over 1000 managers & leaders
-
Certified as Lean Practitioner & Six Sigma´s Black Belt by the IIE, Atlanta , Georgia.
-
Edgar has received direct coaching and professional development from renowned leaders like:, Ritsuo Shingo (Former Toyota President ), PhD. Jeffrey Liker (The Toyota Way), Gary Convis (Former VP at Toyota N.A. )
Language: English
Who should attend?
Leaders who wants to understand how to go beyond tools and create effective management systems in order to increase performance and creating a sustainable lean culture.
Why to participate:
-
KPI established at multiple Levels based on business objectives and function
-
Focus on Actions necessary to ‘move the needle’ on KPI Drivers
-
Timing and Process-completion Metrics to ensure activities are completed
-
”Catch-Ball Process” to align KPIs and Actions up/down and across the organization
-
Prioritization of Resources ($ and People) based upon Company and Department goals
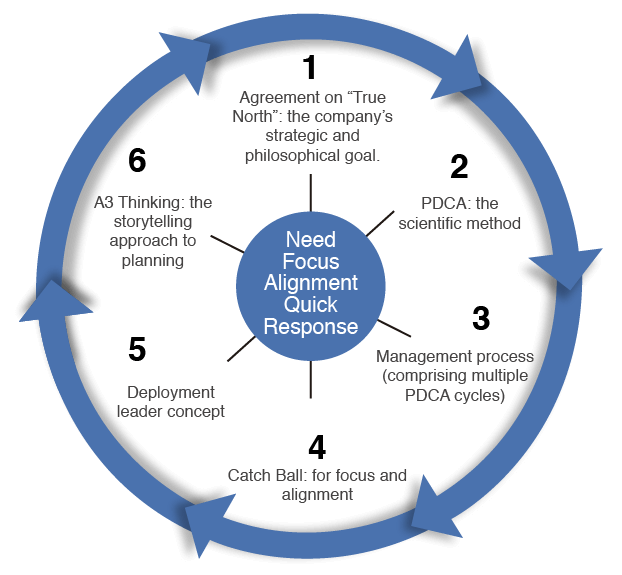
Training Agenda:
- “Purpose of Plan” and Power of Why – True North – Values, Vision, Mission, Roles and Responsibilities of each level
- Top issues and needs for – Customer (Customer Satisfaction Survey), Market, Business, Competition, Economic and Social Trends as well as legal issues
- Corporate and/or Company Headquarters Direction and Needs
- Our Plant upcoming changes, expansion, new product equipment, etc.
- What Strategic Objectives to we need to achieve in the next 5 years?
- Key Performance Indicators Trends
- Current state of these metrics & ID gaps (both type and value), as well as Best Practices
- Internal assessment (State of Lean, Employee Issues, etc.)
- Beyond SWOT to Innovation Strategies
- Servant Leadership
- A new role for the “Next Generation Lean Leader”
- Process KPI’s
- Leader Standardized Work
- Lean Leadership “On the Job Development Model”
- PDCA – Discipline and Accountability
- Role of HR in Partnering with Leadership for Driving Innovative Change
- Leadership Development to Support Hoshin
- Engaged Workforce – Idea Generation
- Coaching – Problem Solving
- Reflection Process
Wrap up, debrief and next steps action plan
Hoshin gives focus on the few critical points to work on
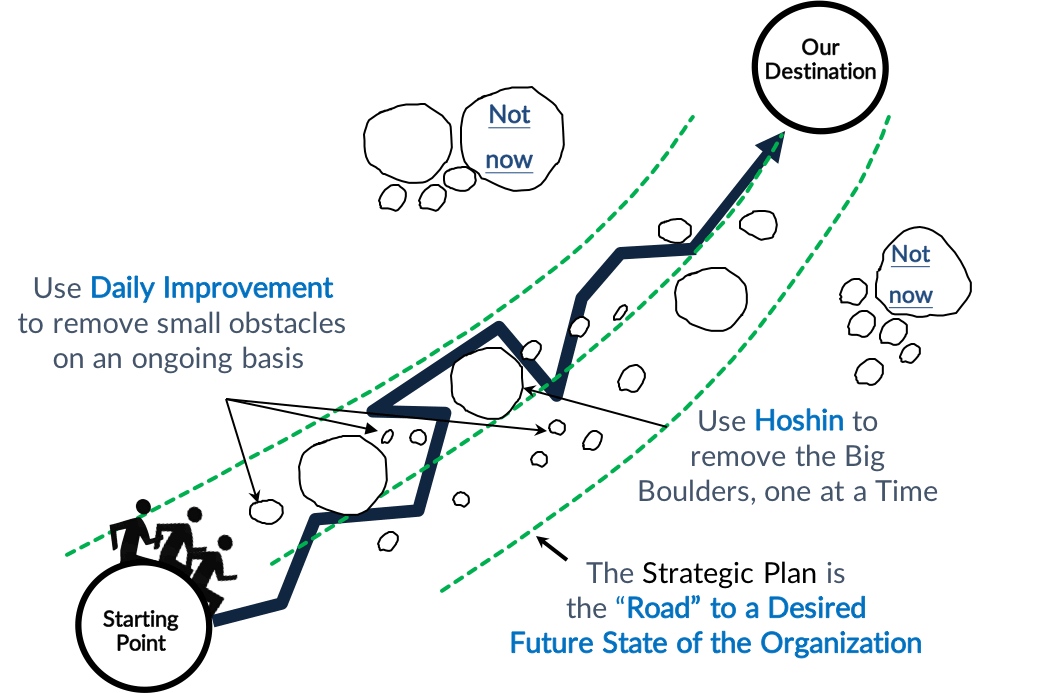
Learn more about Hoshin planning & management
Receive in your email the brochure with all details
Hoshin Kanri, Strategy Deployment, Catchball, Cascade, Shopfloor, Lean Strategy, Visual management, Board, TPS, Hoshin Kanri,