Job Safety and Ergonomics Analysis Training
In-field Training
In our 2-day-workshop participants develop the skills to optimize the workplace arrangement, developing waste free and safer conditions for the workers.
Main Objective: Give the teams the opportunity to learn, practice, and evaluate the current working conditions and define ways to improve the safety and ergonomics (cognitive and physical) of workers in order to deliver higher levels of safety, quality, and productivity.
Align & deploy actions across the organization to achieve your objectives
Participants will split into teams to perform activities in the shop floor and present their observations.
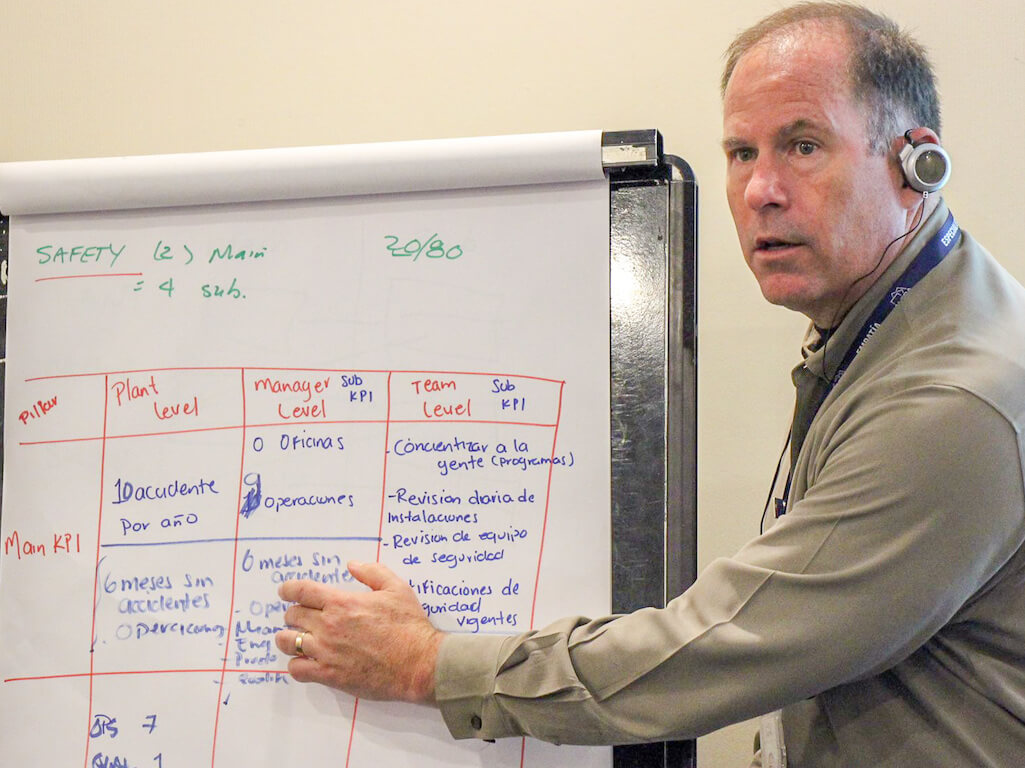
Practical Learning
Learn the concepts from Toyota examples, group exercises and trainer’s experience
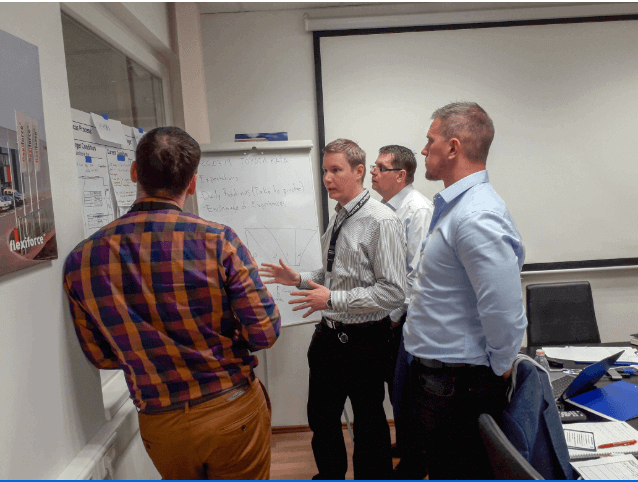
Group Discussion
Share experiences with managers from different industries and background
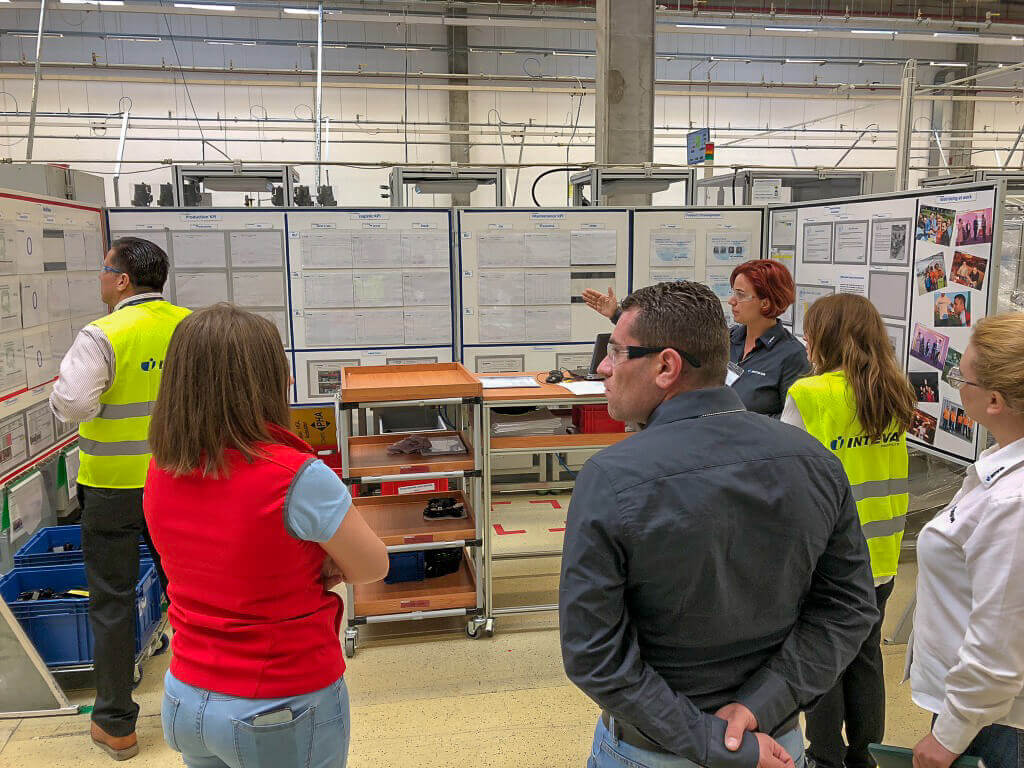
Shop Floor Exercises
The training is hosted by a factory, with activities direct in the process area
Elements of an effective Workplace
Effective workstation arrangement elements:
- Upgrade security (Safety)
- Ergonomically Efficient
- Increased quality & productivity
- Easy Maintenance
- NO Mura, Muri and Muda
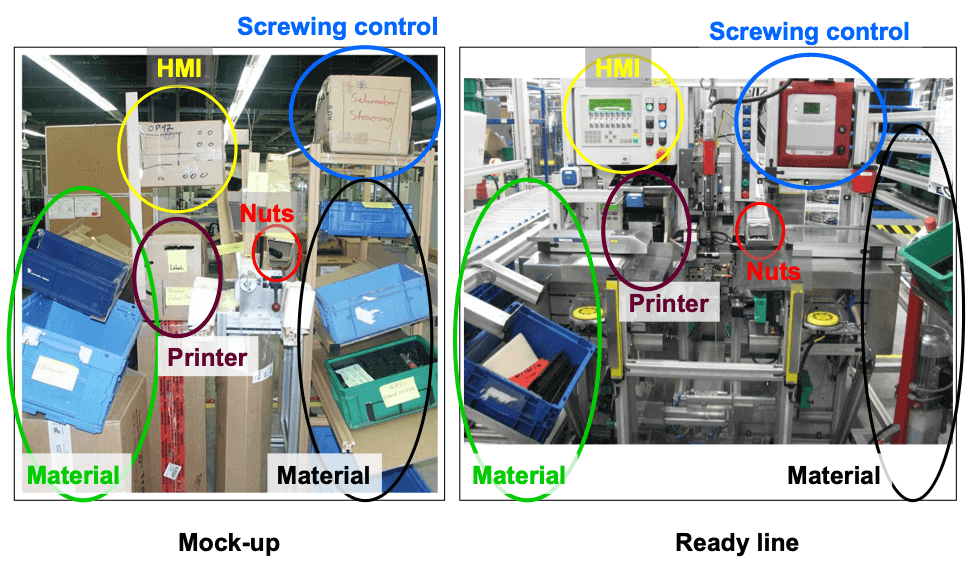
Why participate:
- In our 2-day-workshop participants develop the skills to optimize the workplace arrangement, developing waste free and safer conditions for the workers.
- Learn what ergonomics and job safety analysis means and which benefits it brings.
- Learn the method in a practical way, working in teams, receiving knowledge and sharing with other colleagues’ ideas to implement.
- Participants will be able to pass the knowledge on their companies, being able to evaluate and identify potential risk and waste sources, in order to improve working conditions
- Exercises & real applications are focused on your own operations.
- Participants get a comprehensive understanding of the Ergonomic Principles for Improvement.
- Build capabilities to identify opportunities and improve them.
Training Agenda:
- Mura, Muri, Muda and Risk factors at work
- The Job Hazard Analysis process
- Job Risk Evaluation
- Ergonomics for improving productivity.
- Ergonomic Assessment and Action Plan
- Design for Manufacturing principles to decrease physical workloads
- Ergonomic Assessment and Action Plan
- Leading Ergonomic Improvement Workshops
- Analyze, Assess, Improve, Check.
Instructed by seasoned Lean Coaches
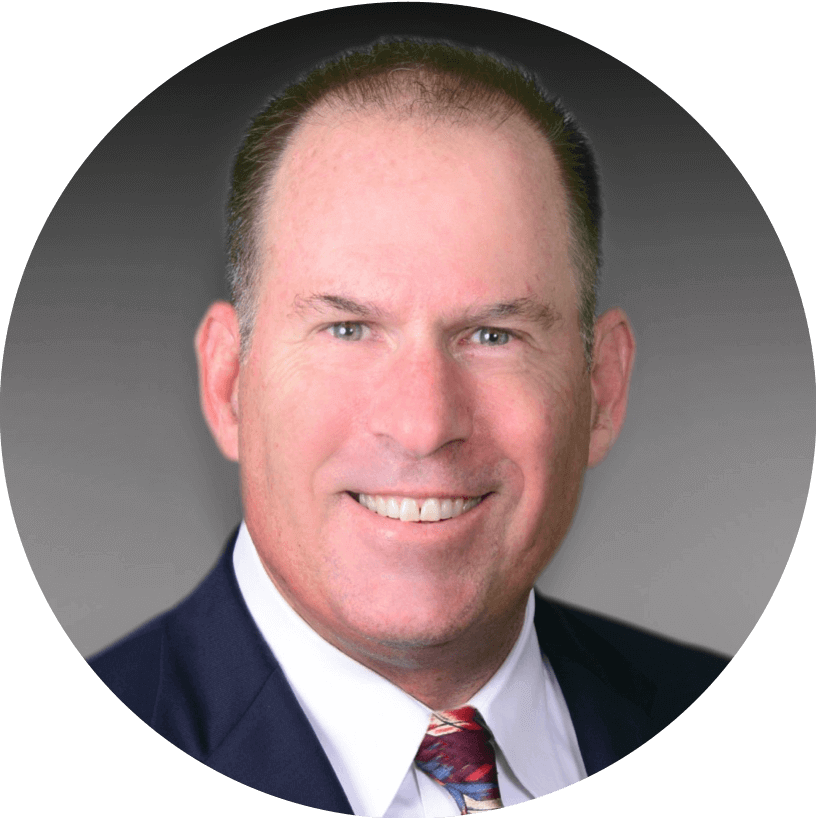
Jeff Strabala
Former Toyota Manager & Operations Management Expert
Jeff worked for Toyota for over 21 years; his extensive experience is based in Operations Management in Toyota North America as Manager and internal consultant.
Jeff was member of the Leadership team for the launch of two “Greenfield” automotive plants and subsequent plant capacity expansions valued in $4.2 billion USD. During his tenure at Toyota, Jeff also spent 3 years of “internal consulting” with improvement projects at Toyota and Tier 1 suppliers.
Project General Manager (Consultant) – Toyota OMDD
- Internal consulting position, Investigation, Analysis, and Improvement of floor operations applying core Toyota Production Systems tools.
Project General Manager – Toyota North America.
- Improved Safety Systems for Toyota’s MS manufacturing plant through active initiatives to educate plant personnel revise and introduce new programs, establish management accountability through daily reporting and monthly performance meetings, introduced gated safety management process that reduced TIR by 50% within 6 months.
- Developed, Validated comprehensive [all functions] Safety Metrics during 2013 New Generation Corolla launch, resulted in improved safety KPI during launch, Metrics, tracking and reporting adopted in North American Region.
Assistant General Manager-Toyota
- Responsible for Plant Manufacturing Operations, member of Executive Team,
Primary responsibility for Production Control, Supply Chain & Logistics, Project Management for 8 Model changes, Plant Manpower Productivity planning and reporting. - Supported Toyota Production System training and application, and Visual Management (FMDS) roll out at TMMBC, management Mentor.
Manager, Production Control – Toyota (TMMBC & TMMI)
- Production Control Planning & Coordination of Operations for Toyota truck factory with multiple product lines 2000 -2003.
- Additional collateral duties involved management of TMMI Corporate Strategy and Reporting, TPS Training Group, Manpower Planning and Productivity group.
Manager Accounting & Finance, Toyota TMMI
- Started up Accounting & Finance operations for Greenfield Toyota plant in Indiana, responsible for accounting, internal and government compliance, budgeting and cost reduction efforts.
Host Plant: Inteva Products
Inteva Products Salonta Plant produces latches, window regulators and mechanical cables for several world class automakers. Salonta site has being in the lean journey for several years, achieving tangible benefits in performance, developing the teamwork to solve any kind of issue and continuously learning.
Committed to the highest standard for quality, Inteva meets all customer requirements and expectations. The company is focused on total commitment toward the continuous improvement of products and processes. Inteva employs over 15,000 team members in 18 countries. Inteva World Headquarters is in Troy, Michigan.
Inteva Products Salonta Plant produces latches, window regulators and mechanical cables for several world class automakers. Salonta site has being in the lean journey for several years, achieving tangible benefits in performance, developing the teamwork to solve any kind of issue and continuously learning.
Our product lines include Closure Systems, Interior Systems, Motors & Electronics and Roof Systems, and we have more than 90 customers, including virtually all of the world’s leading global and regional automakers.
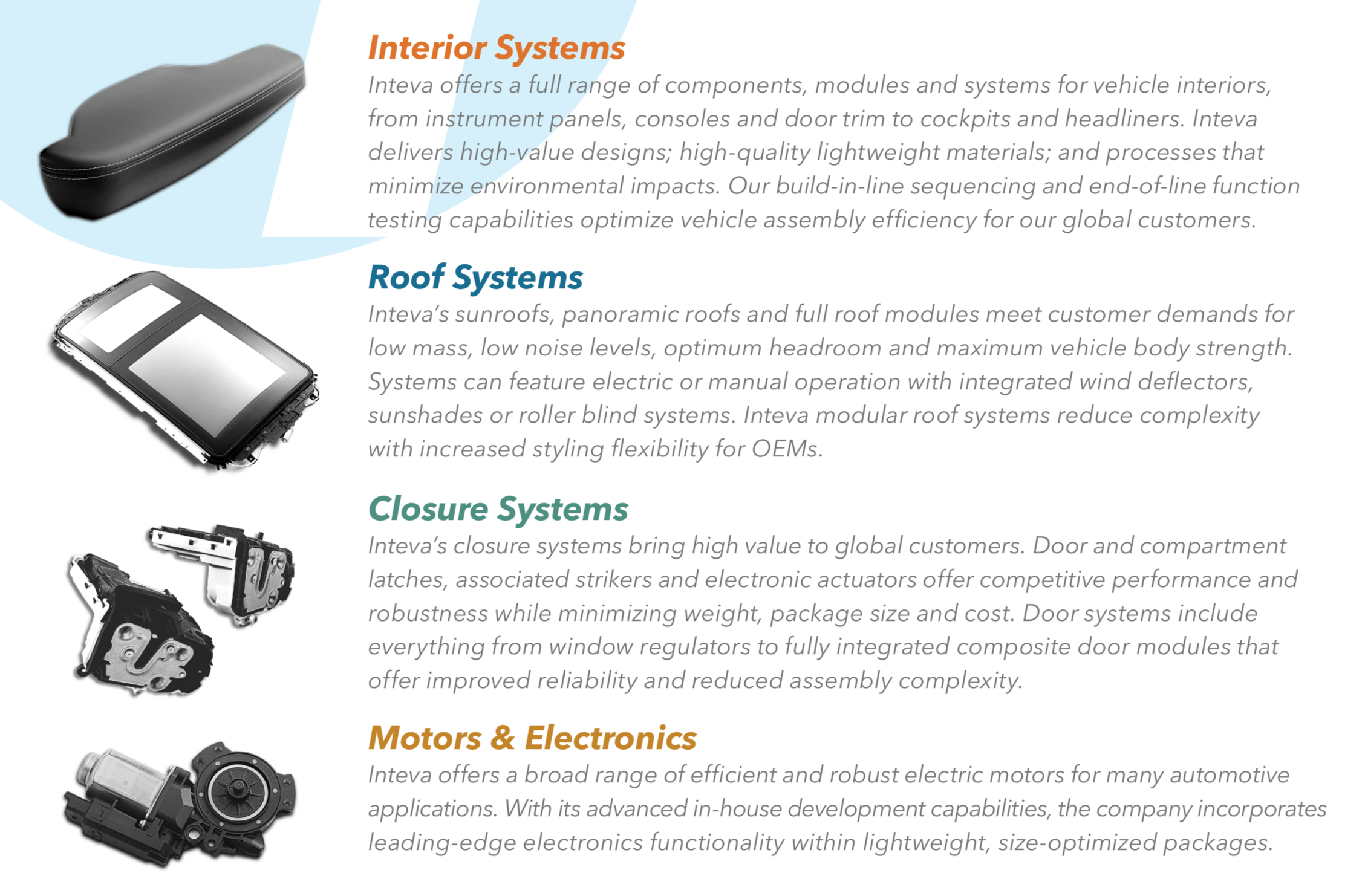
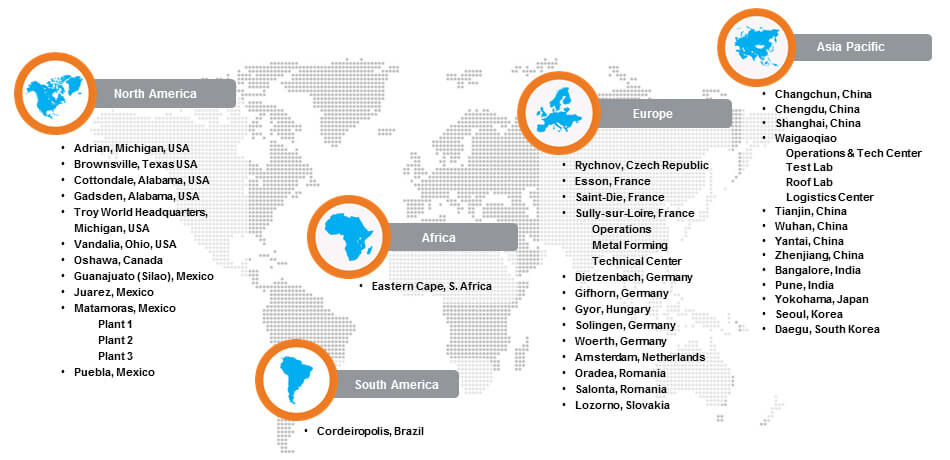