Lean Management Consulting & Support
We can help with the different stages of your journey towards operational excellence.
Why are we different?
ALFRA Consulting is a leading consulting firm with years of proven record. Our aim is to accelerate the capabilities of your organization, to identify and improve the performance of their operations.
Even when significant benefits can be achieved in a few months, sustaining outstanding results will be achieved through a culture of permanent learning and improvement, with people development as the core of everything.
Any strategy that is not centered on the people is doomed to fail!
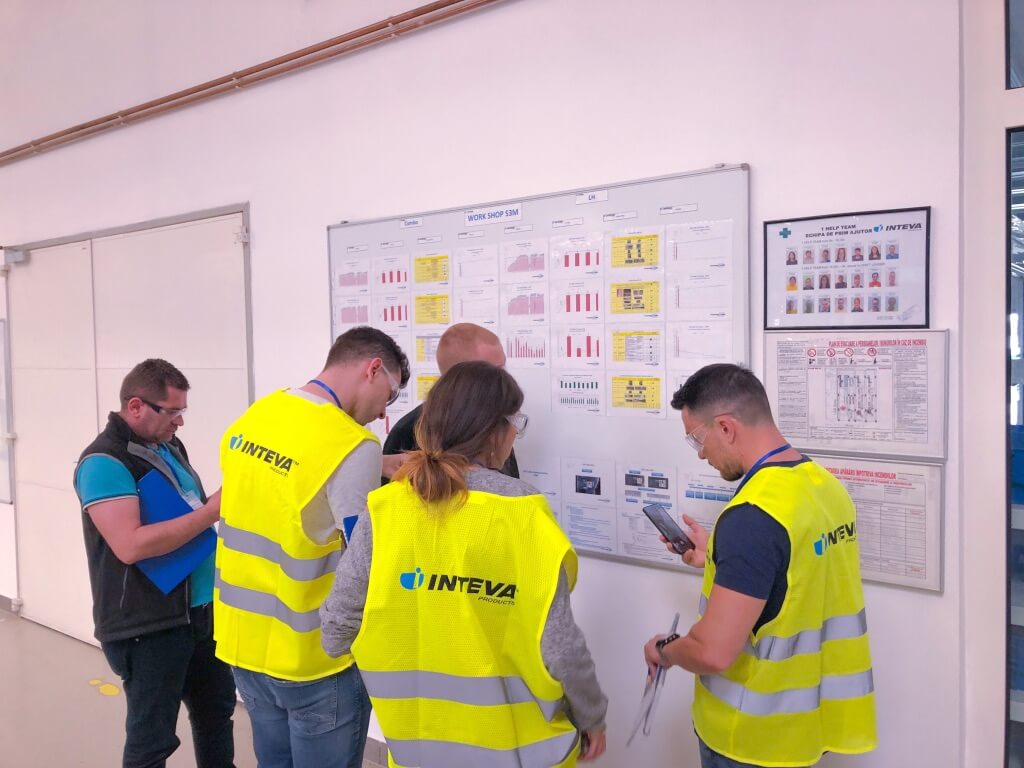
Benefits from lean deployment*
*results differ by industry & maturity.
-
30 to 50% Lead Time Reduction
-
5% to 30 % Quality Improvement
-
20% to 50% Space Reduction
-
15% to 50% Labor cost Improvement
-
Sustainment of results through highly empowered teams
OUR LEAN CONSULTING APPROACH
Building long term success with systems that goes beyond tools!
“We can help you on the different phases in the long road towards a LEAN transformation, contact us if you would like to learn more about your companies needs so we can adapt a program according to your organizational culture ‘’
-
1) Operational Assessment
Grasp the actual situation of the company, identify the gaps vs. desired condition, we base in our model of The Toyota Way Assessment
-
2) Roadmap Development
A middle term plan is defined aligned to the strategic goals of the company
-
3) Systems Deployment & People Development
Deployment of management systems & tools, while developing internal capabilities in the team
-
4) Periodical maturity assessments
We measure the evolution of the journey to evaluate success and adjust/set targets
Each company develops its own Culture
We have experience helping companies around the globe from several industry sectors.
|
|
---|
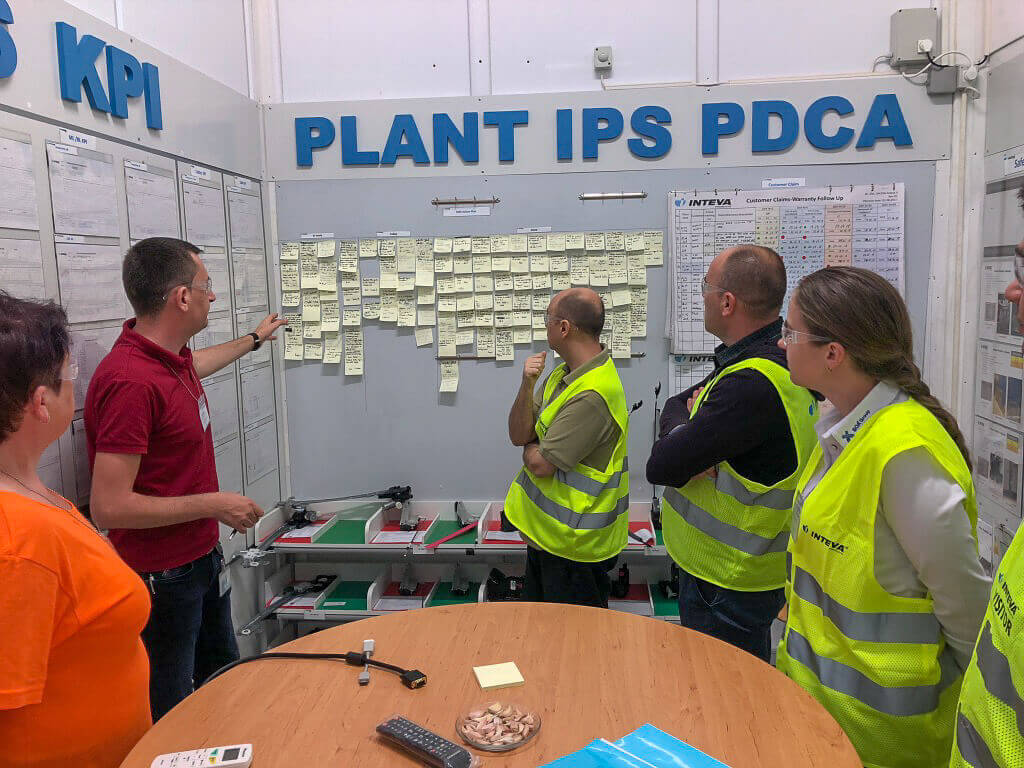
We review the established systems and tools, interviewing with the leadership team, middle managers, and front line associates. We also analyze the evolution of the KPI across the last years.
We are looking for evidence of the 4Ps (Philosophy, Process, people, Problem-solving) and how is aligned with the company´s objectives.
We correlate the actual management system with the behaviors generated, in order to define the current situation and assess the gaps against the ideal state, delivering a strategic roadmap, which should be deployed by the management team.
Lean Systems Deployment Support
In a coaching scheme, systems are deployed by the managerial team, while being assessed and given feedback by the consulting team, but direct responsibility falls on the company’s managerial team responsible for the deployment of Lean. The consulting team will provide general guidance and the means to develop Lean tools by the internal team.
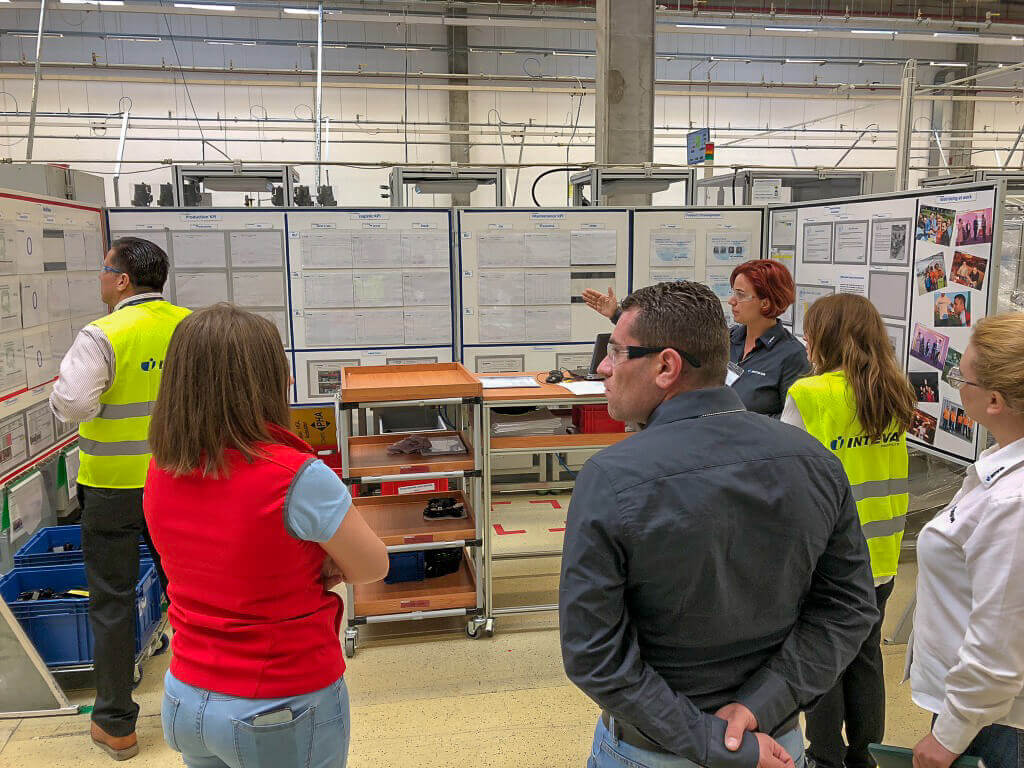
Leaders Coaching & Development
It’s essential to begin with leaders that clearly understand the vital role as coaches and facilitators, it’s of much importance to have personal development before being able to develop others, making leaders which live by the companies values, aligned to operational excellence. The first leader development in Lean Management must be at a directive level since they will be the ones that create a culture within the organization by means of the systems and behaviors established.
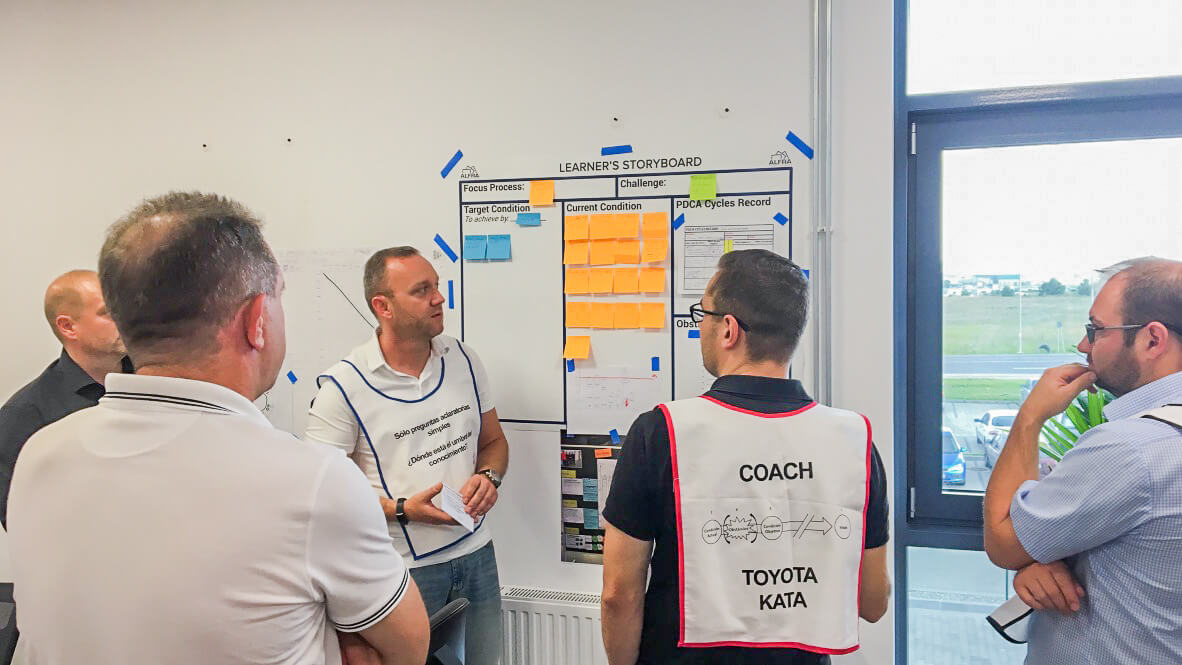
Leadership Development Japan Training
Schedule a call with us to tailor a plan for your objectives
Lean management, Quality Consulting, TPS, Kaizen Consulting, Lean Consulting, Consultant Lean, Leadership Coaching, Dezvoltari de lideri, 5S Coaching, Problem Solving, Consultanta Manufactura, Lean specialist, Lean experts, CI, Continuous Improvement, Daily Kaizen, PDCA, 5s Consulting, Consultanta Management, Leader Standard Work, Lean transformation.
Lean Consulting, Management Consulting, Lean Coaching, Kaizen Consulting, Romania, Process improvement, Continuous Improvement, BPI, TPS, Toyota Way