Production Planning and Control Training
The key for real Lean Production success
One of the keys to Toyota’s success is the role that Production Planning and Control plays in the organization.
Production Planning and Control is the voice of the Customer to manufacturing and conversely it is the section that manages information flow from the Customer, Suppliers, Manufacturing and Engineering.
As Atsushi Niimi (former President of TMMNA) once said, “PPC is where the real power of Toyota is”.
Hands On – Gemba Workshop at Host Company
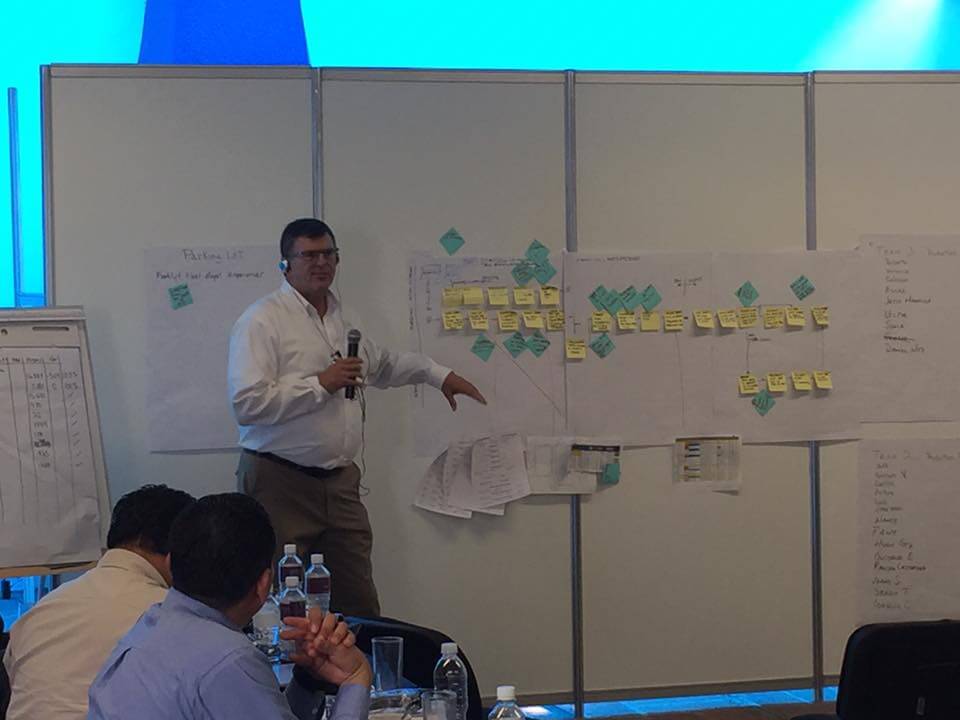
Learn to Map the entire Supply Chain
Identify & Analyze the main opportunities from the supply chain with a real value stream mapping in the host company.

Group Discussion
Share experiences with supply chain professional from different industries and background.
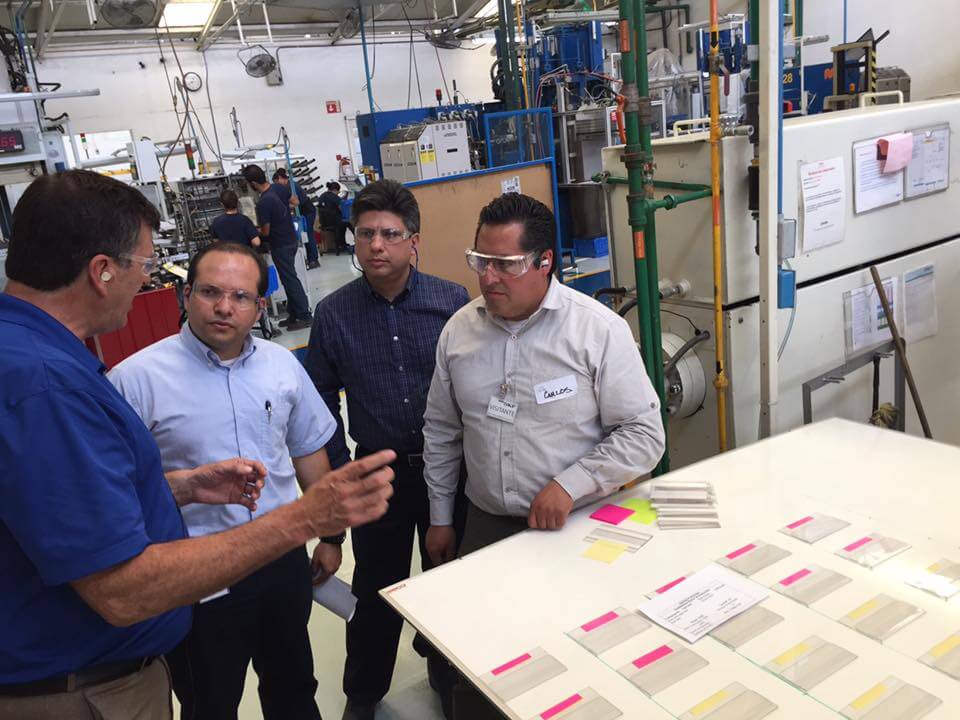
Real Implementation
The training is based on a real project environment to define a production plan and its requirements.
Training Lenght:
24 Hours (3 days)
Who should attend?
General Managers, Managers and Supervisors in Supply Chain, Production Planning or Lean Implementation that would like to understand how to maintain a consistent flow of information while supplying the plants with Just in Time product and materials.
Recommended industries:
Manufacturing Companies: Automotive, Electrical/Electronic, Pharmaceutical, Food & Beverages, Printing, Plastics, among others.
Participants will understand the Toyota Way in:
- How to create a Production Forecast
- How to smooth a weekly production schedule.
- How to facilitate a Production Forecast Meeting
- How to adjust daily production based on Pull System.
TRAINING AGENDA: BODY OF KNOWLEDGE:
- 4 hrs.
- Role of PPC in a Lean Company
- Current Planning vs Production Planning and Control(PPC)
- Creating a Production Planning Group
- Creating a Production Plan (Theory)
- Defining TAKT time
- Creating a Production Forecast
- Creating the Production Plan
- 4 hrs
- Go, See and Understand (Gemba) at planning.
- Gemba Walk Production Line
- Map current State production plan
- Value finished Goods
- Create Production Board(Maintenance Support)
- Create Finished Good Kanban (Staff Support)
- 50% of Team. 6 hours
- Select Target Product Line(cell)
- Create Production 2 month production forecast 1-month firm plan.
- Create Weekly Plan
- Set Min~ Max inventory Targets
- 50% of Team. 6 hours.
- Inventory Finished Goods
- Create Daily production pattern
- Set up Kanban Board Kanbans
- Production Team/Conveyance Training
- Entire Team, Production Manager, Conveyance Manager. 2 hour
- Status check
- Roadblocks and Countermeasure.
- Develop checklists
- 6 hours.
- Assign each member to small group of 2~3.
- Process confirmation.
- List Problems
- Report Out. 2 hours.
- Reports Results
- Report lessons learned
- Create host company homework
In this course we will:
- Show the Roles and Responsibility of PPC in a lean organization.
- Create a smoothed weekly Production Plan that will absorb order fluctuation.
- Create a Kanban Replenishment system to drive Just in Time Production while maintaining minimum and maximum inventory levels of finished goods
- Measure the results of our trial.
This workshop will give the participant a chance to create a Production Forecast and Firm Plan, create a weekly plan, and create a Kanban control board to regulate production (replenishment) and confirm production readiness (Man, Method, Machine and Material).