
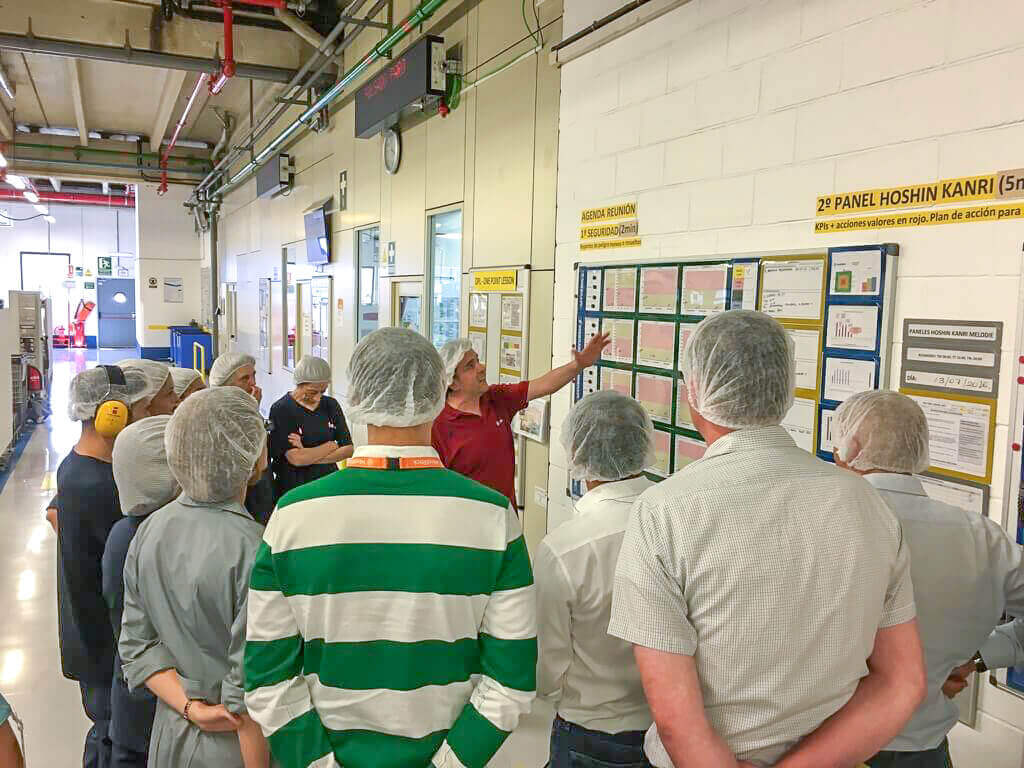
Lean Management for Business Processes
Reduce delivery time, increase productivity and service quality levels, with the same people and less stress.
This program address the factors to get you out of the improvement trap
Most companies embarking on a lean journey soon become frustrated with improvement events and isolated projects that yield great short-term results but have no sustainability and no major innovation.
They are searching for something more: the culture that goes beyond “just managing” continuous improvement.
Align & deploy actions across the organization to achieve your objectives
Participants will split into teams to perform activities in the shop floor and present their observations
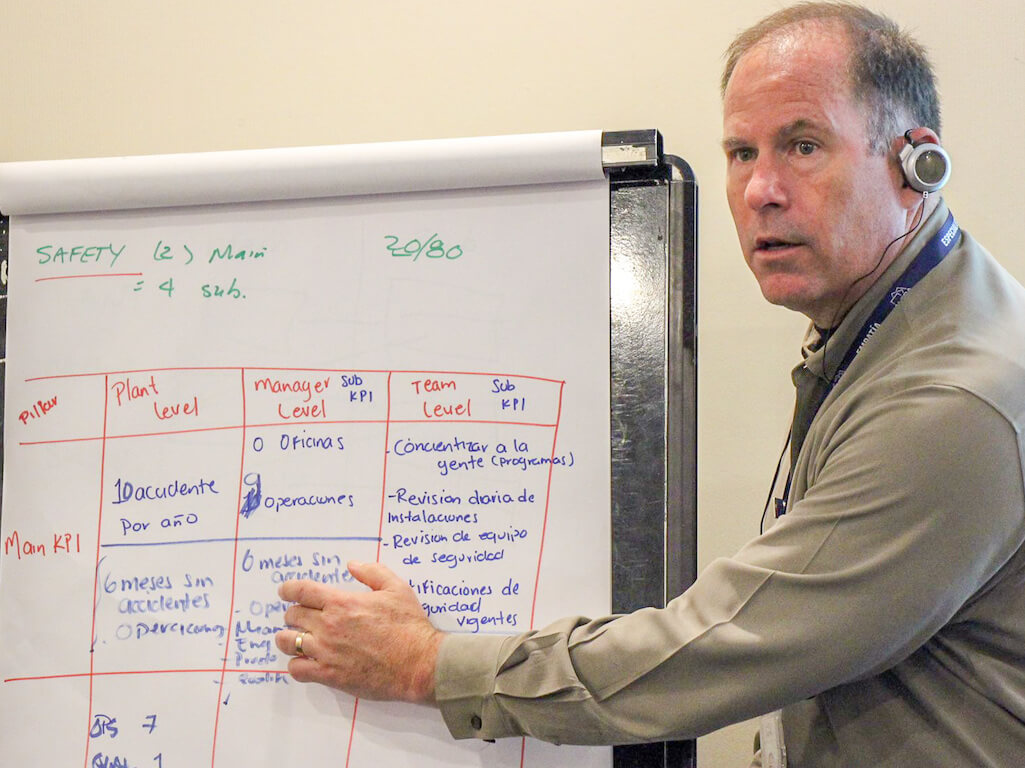
Practical Learning
Learn the concepts from Toyota examples, group exercises and trainer’s experience
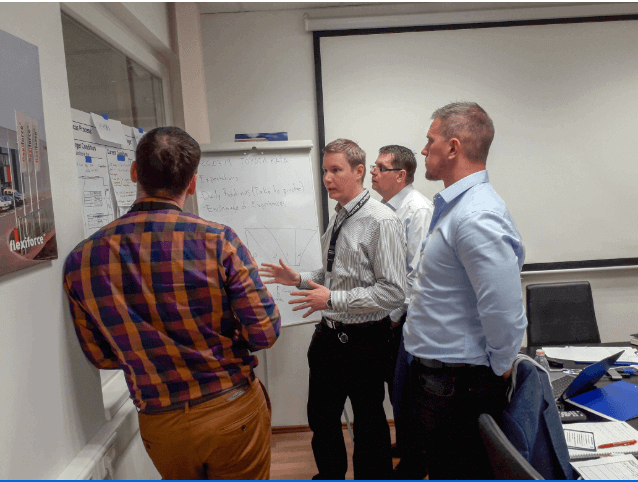
Group Discussion
Share experiences with managers from different industries and background
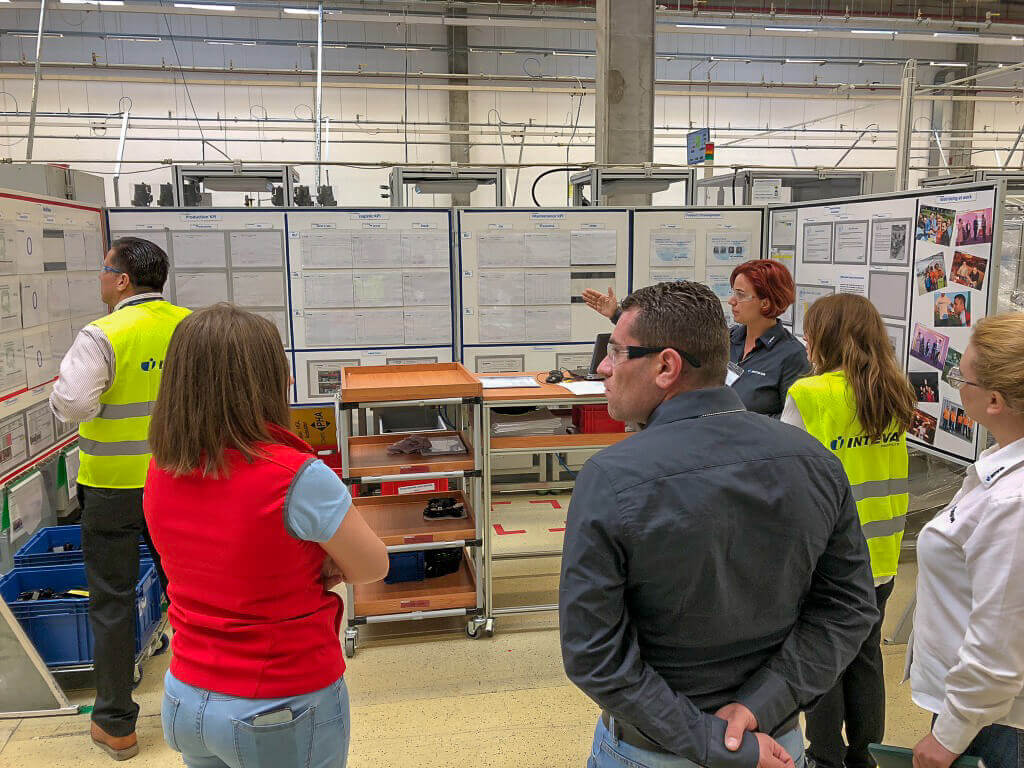
Shop Floor Exercises
The training is hosted by a factory, with activities direct in the process area
Who should attend?
Leaders who wants to understand how to go beyond tools and create effective management systems in order to increase performance and creating a sustainable lean culture.
Why to participate:
-
Learn how to set up the framework for daily management system to engage every level of management and team members towards driving business results
-
Learn by doing: Alignment of the organization’s goals and activities both vertically and horizontally to drive the desire behaviors.
Recommended Industries
Manufacturing (Automotive, Food, Plastics, Electronics…), & Services ( Banking, IT & Project based companies).
- Implement methods to stabilize, speed up and assure quality of processes
- Identify and break interdepartmental constraints to ensure team work
- Visualize and measure the process’s main opportunities
- Origins of the Lean System (TPS)
- Lean Thinking objectives
- Lean at Transactional Environments
- Lean System vs. Traditional System
- Challenges in the Transactional Areas
- The 8 Wastes at the Office
- Definition of Value at Transactional Work
Module Activities/Exercises
- Value Classification (VA, NVA, BVA)
- 8 Wastes Walk
- Process time, Lead Time , VAT
- Set ups, batch size & Fiability
- Inventory (Work in Process or in Queue)
- Accurate & Complete Info (%A&C).
- Information Technologies Used
- People Involved in the Process
- Document Information & customer requirements
- Identify Main Process es (In order).
- Select process indicators
- Walk the Value stream & draft main processes
- Identify how work is prioritized
- Calculate Value stream Metrics
Module Activities/Exercises
- Value Stream Case Mapple Inc.
- Value Stream Case Borgis Corp
- 5S & Visual Management
- Standard Work System
- Pull Systems
- Continuous Flow Approaches
Training Agenda:
- Value Stream Analysis & Proposal
- Consensus & Commitment in Action Plan
- Value Stream Mapping Future State
- Basic Problem Solving – PDCA Cycle
- KPI establishment
- Daily Management
- Cultural Enablers
- Lean Thinking vs. The Toyota Way
Follow up Application: Explanation of the Post training activities
Instructed by seasoned Lean Coaches
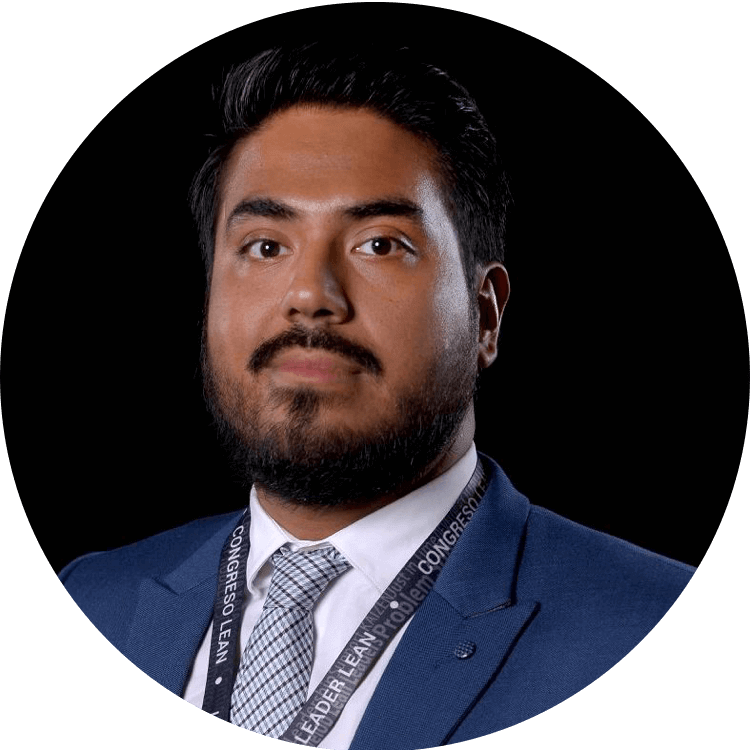
Edgar Cardenas
Lean Advisor & Coach – Europe Operations Director
Edgar has worked the last years in countries like Romania, Hungary, Russia, Mexico, Colombia, Spain and USA…, providing support to companies on their improvement journey based on developing teams to improve the quality of people & processes, in several industries including: Automotive, Electronics manufacturing, Food & Beverages, Plastics, Shared Service Centers, logistic services, among others.
He recently provide support to companies like Bosch, Hino Motors, Mercedes Benz, Kimball, Zebra technologies, Takata, Inteva Products, Dawn Foods, BOA, Mars, Rubbermaid, Faist Group, Emerson, Exide, Harsha Engineers, Steelcase..
-
Lean for Business Processes corporate trainer for several companies
-
Operational Excellence speaker at several international Lean Conferences & Summits.
-
He has developed in Lean Management over 1000 managers & leaders
-
Certified as Lean Practitioner & Six Sigma´s Black Belt by the IIE, Atlanta , Georgia.
-
Edgar has received direct coaching and professional development from renowned leaders like:, Ritsuo Shingo (Former Toyota President ), PhD. Jeffrey Liker (The Toyota Way), Gary Convis (Former VP at Toyota N.A. )
Align and engage all the company levels to go beyond the “typical” Lean implementation
9-11 July, In-field Training at Inteva Salonta
After training attendants will be able to:
- Clearly identify what adds value & what is waste from the perspective from the different customers
- Develop Lean System for reliable and flexible processes
- provide guidance in the first steps for a Lean Journey
- How to assure and achieve certainty of the service levels for every process
- Identify & Break interdepartmental constraint with fundaments to enable real team working
Daily Management Development System
Where can we implement Lean management?
Major benefits are observed in operations with a high interaction of people/functions, technology, culture, procedures and policies.
Companies which rely in constantly delivering new and innovative product/services to their customers, require a high performance process, the lack of a common objective and a poor interaction between different functions and people (customer, sales, marketing, engineering, finance, operations, contractors and more) are the main contributors to end with a slow reaction to the customer or market, deliver with low quality and high development costs, ending with a scarce conversation rate of successful launchings or new contracts.
Aligning priorities and enhancing communication improves the information flow, developing standards of work and a pull managed work system, with a quality at the sources method (not letting pass any problem to the next step), enables an accurate and timely development cycle, improving at the end the rate of success.
In project based environments, the alignment of priorities and communication is critical to deliver projects on time, with the desired functionality (quality), and under budget.
This can be done implementing Lean management systems where we organize our team to perform the work according standard priorities and improving communication (daily management system) across the entire process, this management structures helps to react to daily arriving issues and changes. Developing a robust and simple process management ensures stability and reliability, that means we can offer to our customers a consistent delivery time, within cost and in quality.
Companies from IT, Construction, and any other service delivery company can benefit from this approach.
Lean can be implemented not only in operative processes but in the functional processes that support the delivery of the value, regardless if it’s a product or service, the operations of valued added required processes that enable them.
From the communication with the customers, the sourcing of the raw material, the internal planning and scheduling, the manufacturing itself, the delivery of the product, the invoicing and the accounts payables until the payment is received, all this process can be improving with the Lean point of view.
Saving important days in cash flow for the company and increasing the flexibility to be able to respond faster to the customers.
The main objective of a customer service office like a call center or help desk, is to provide a fast and accurate response to its customers, the random arrival of different types of customers and the wide range of inquires/topics to resolve, tend to create unstable processes and inconsistent quality and delivery time, ending with upset customers and a lack of credibility in the service center.
Lean management systems provide consistency on the performance, giving stability to the processes, through developing people and establishing management practices, we will bring the problems to the surface in order to improve them.
Visual management, pull systems, standard work, quality at the sources, cross training, among other Lean concepts are implemented.