
Quick Response Quality Control (QRQC) in Field training
“Quality is not a matter of certifications or tools, but a matter of Management”
How to build a Lean Quality system
A major frustration for companies is the failure to definitely solve recurring problems, even when implementing countermeasures, problems reappear.
Being able to solve these issues requires:
-
Skills to analyze in the shop floor in order to find the problem’s root cause
-
Get real information from operators level to solve the problems fast.
-
Validate the factors that reproduce the problem
-
Verification methods that help keep any countermeasure
-
Develop actions to prevent future problems.
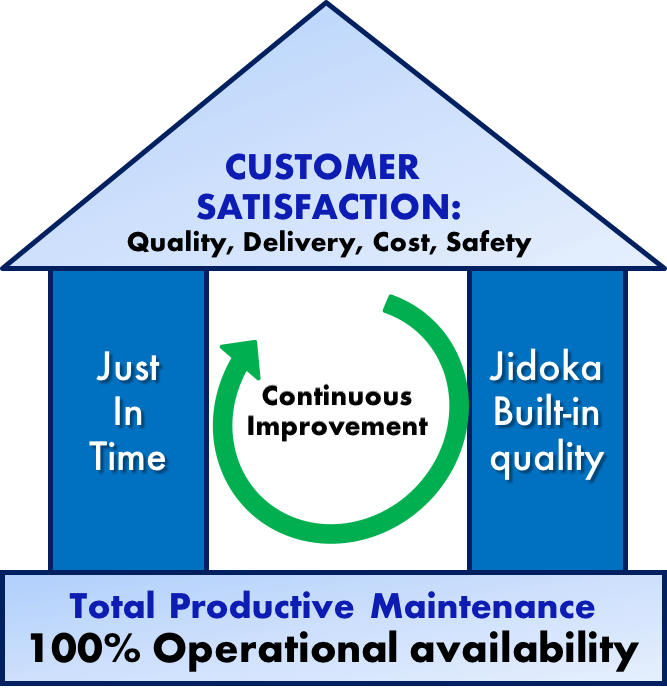
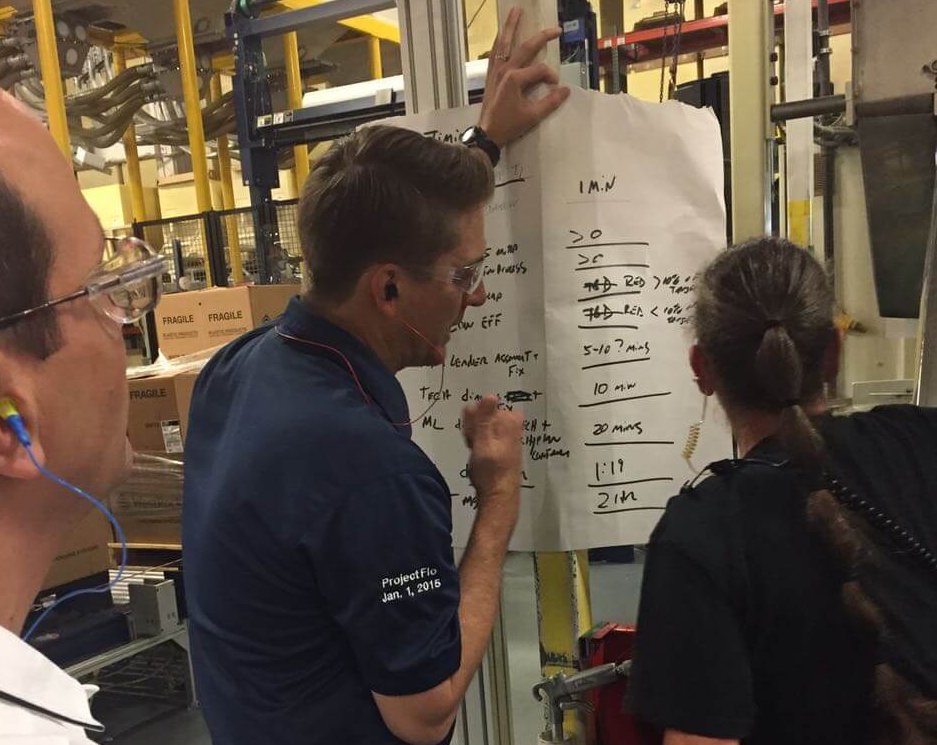
Understand the QRQC Structure
Understand step by step how to build a quick & effective quality management
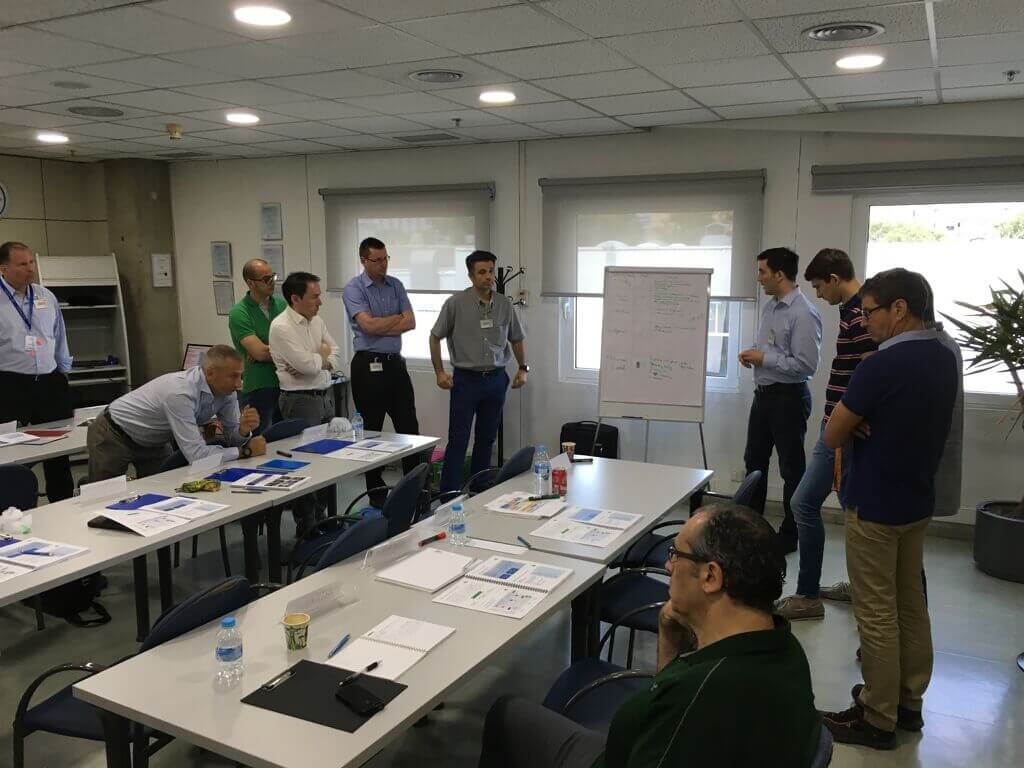
Team up with other professionals
Share experiences and discuss with colleagues from different industries
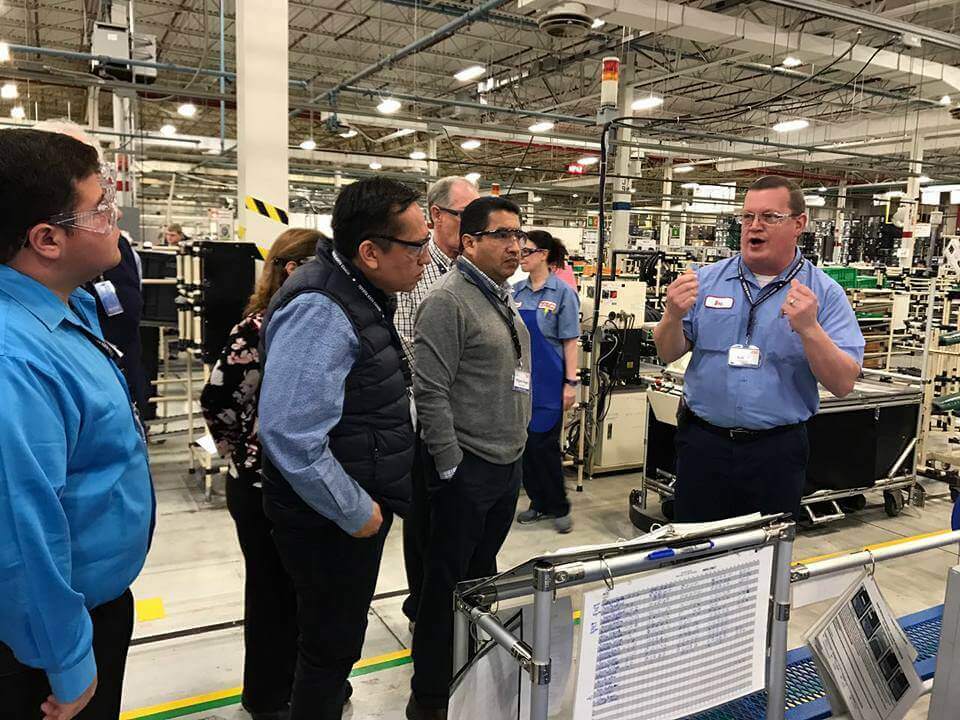
Genba Activities
We will practice the concepts directly on the host plant shop floor
Who should attend?
General Managers, Managers and Leaders in Quality, Manufacturing, Engineering and Lean departments.
Why participate:
- Understand the San Gen Shugi attitude
- Explain the QRQC objectives, phases and tools
- Practical application of the QRQC method using real problems in the plant
- Understand how to deploy the QRQC method in your plant (meetings, follow up, indicators..)
QRQC Main benefits:
- Solve quickly and effectively problems, prevent occurrence.
- Develop in your team an attitude of reality based management & problem solving
- Use lessons learned for future projects to improve product and process quality.
Workshop objectives:
- Understand the San Gen Shugi attitude
- Explain the QRQC objectives, phases and tools
- Practical application of the QRQC method
- Understand how to implement the QRQC method in your plant
What is QRQC?
A structured approach to quickly answer to problems that occurs at our customer or internally, taking immediate countermeasures and analyzing to develop solutions that eliminate the recurrence of the problem.
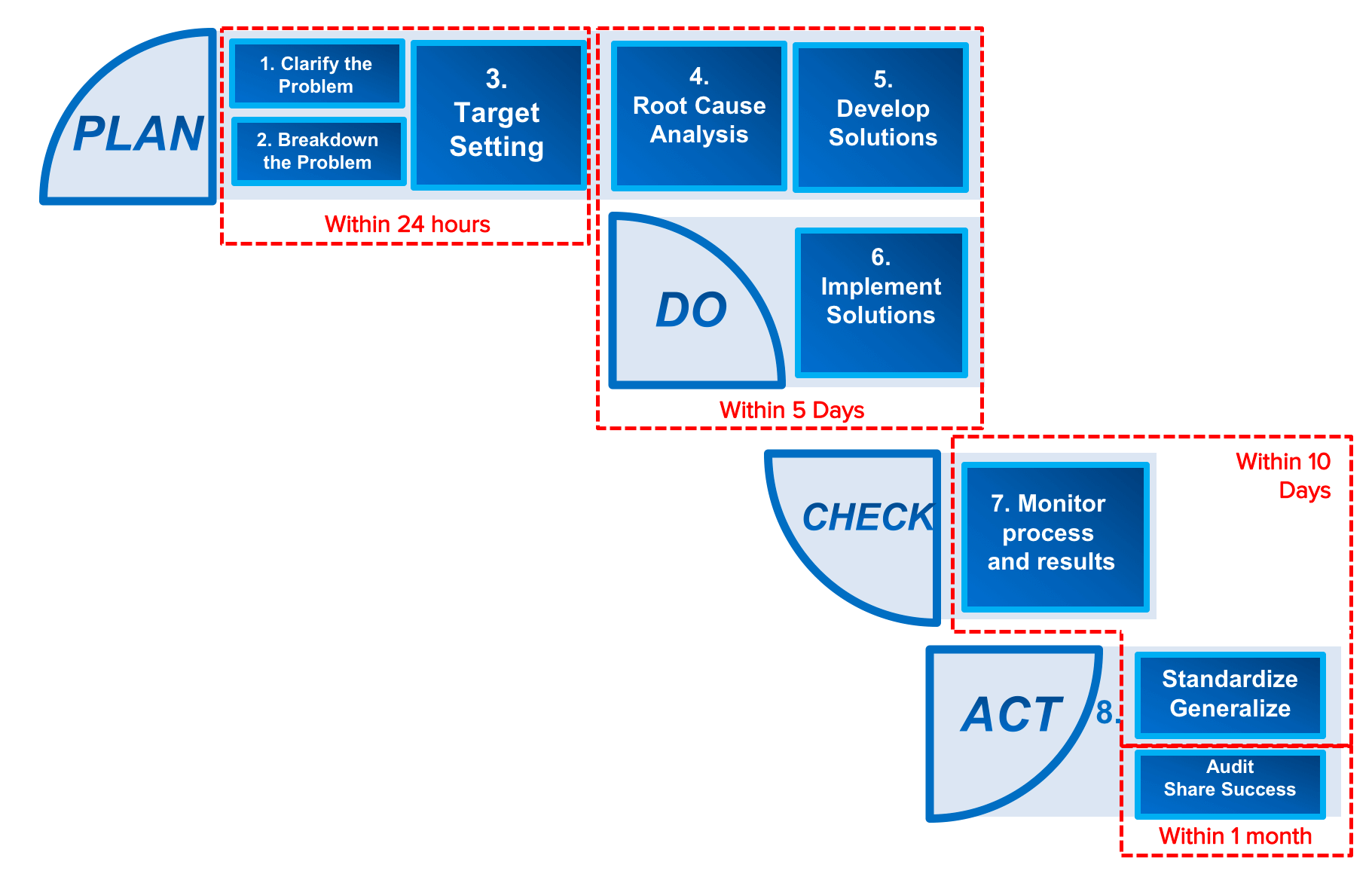