8D – Problem Analysis and Solving Training
Practice on how to identify, analyze, solve and prevent problems
In-Field Training

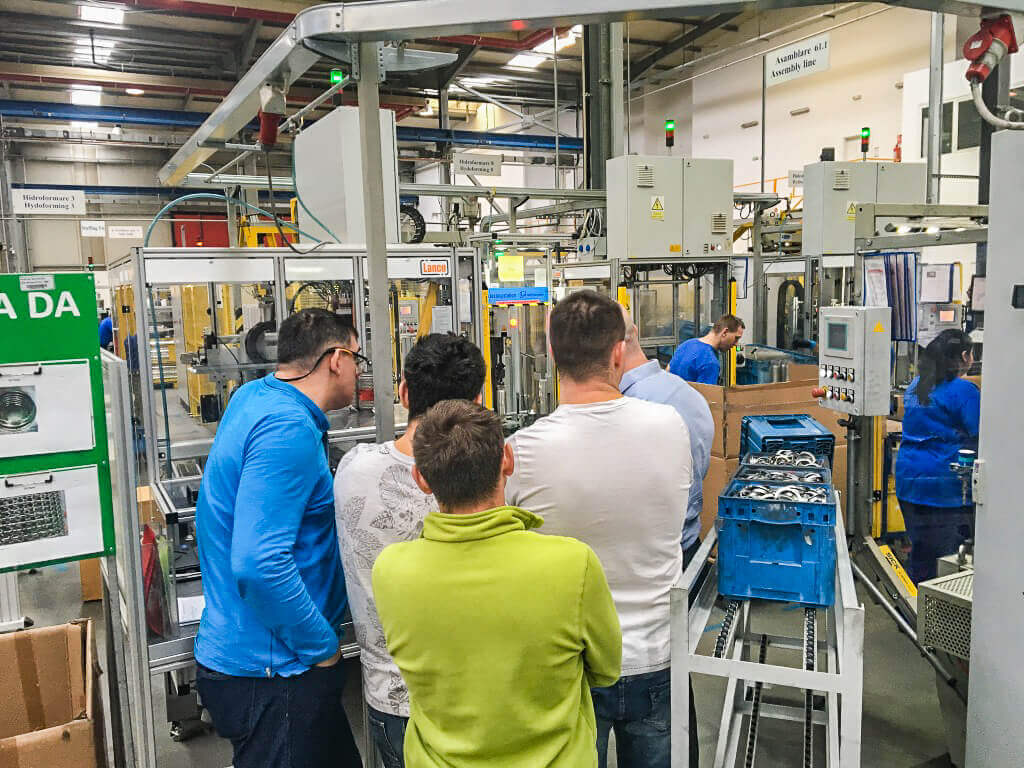
A major frustration for companies is the failure to solve recurring problems, even when implementing countermeasures, problems reappear.
Which are the 8Ds?
- D1: Defina cross-functional team
- D2: Define the problem
- D3: Take Short Term Action (Containment)
- D4: Determine Root Cause
- D5: Develop Countermeasures
- D6: Implement and Validate Countermeasures
- D7: Prevent Recurrence and share lessons learned
- D8: Recognize the Team
Companies need to have Strong & Consistent:
- Means to quickly visualize and prioritize issues
- Analysis skills to understand & breakdown the problem
- Validation of the factors that creates the problem (systemic root cause).
- Discipline to verify actions and results
- Improvement actions to prevent future problems.
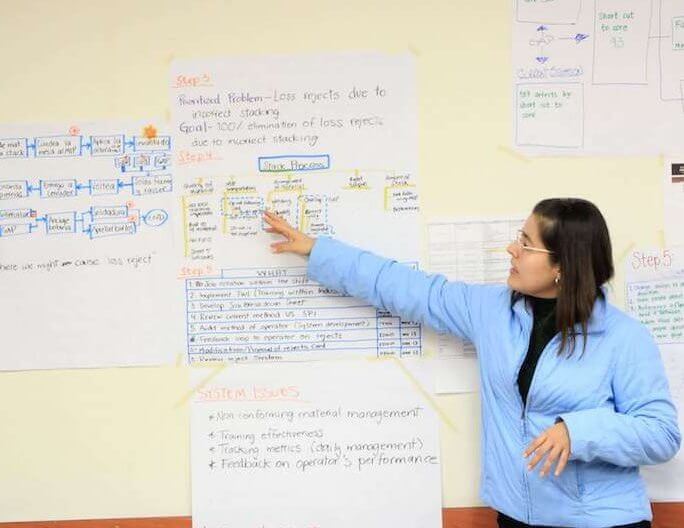
Which are the 8Ds?
- D1: Defina cross-functional team
- D2: Define the problem
- D3: Take Short Term Action (Containment)
- D4: Determine Root Cause
- D5: Develop Countermeasures
- D6: Implement and Validate Countermeasures
- D7: Prevent Recurrence and share lessons learned
- D8: Recognize the Team
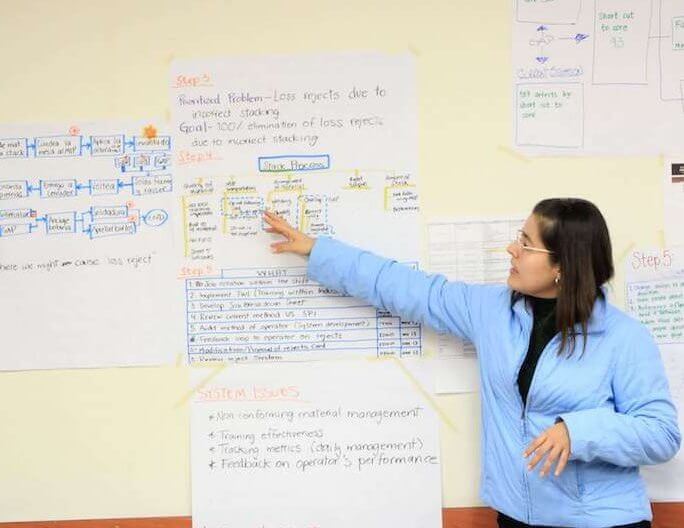
This training will give participants the foundation necessary to start the first steps of the 8D – Problem Analysis and Solving implementation and review best practices used by Toyota and other manufacturers.
Learn how to prevent, identify analyze and solve problems within your company.
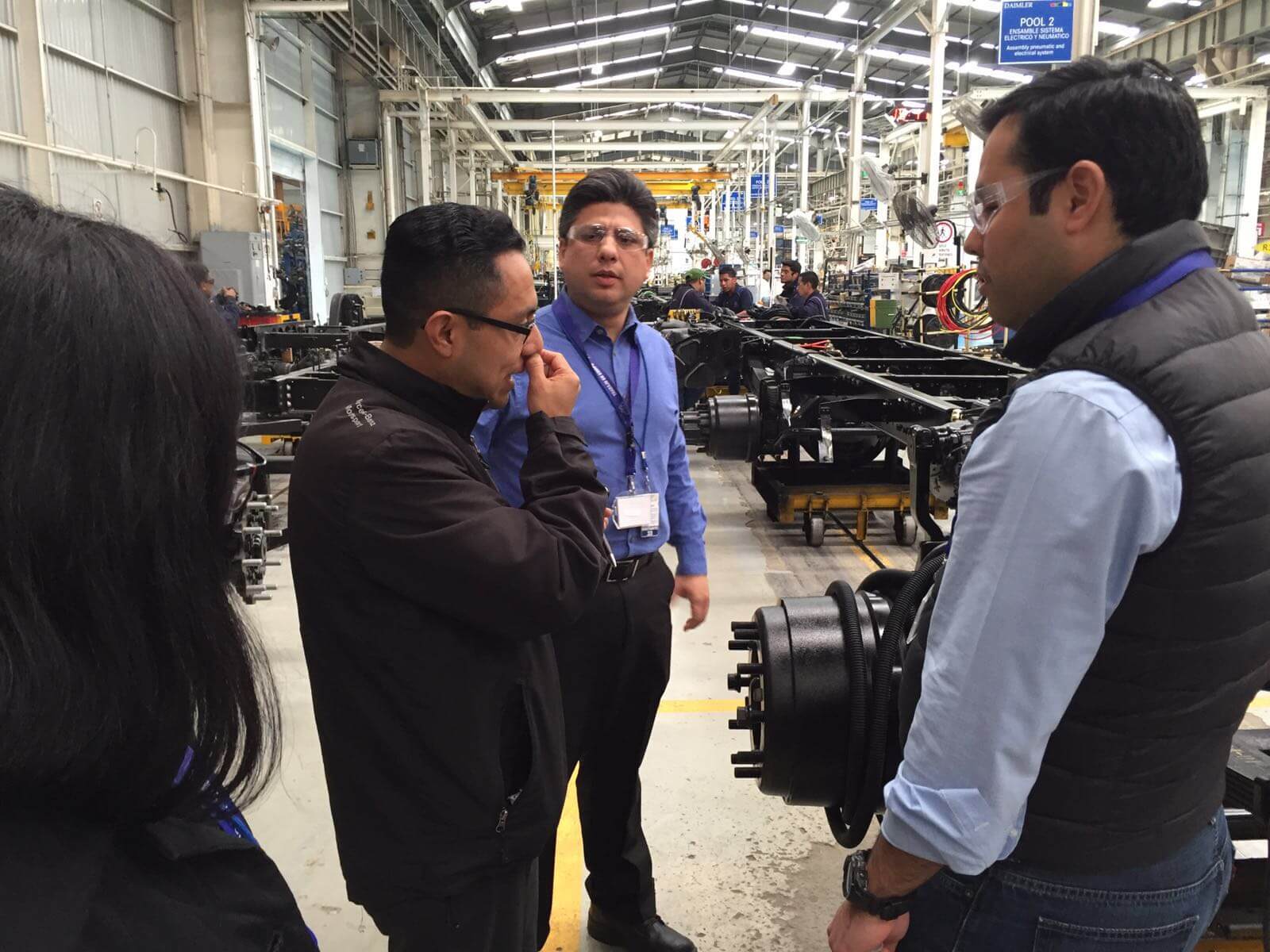
Applications on Shop Floor
We will perform activities directly in the process area
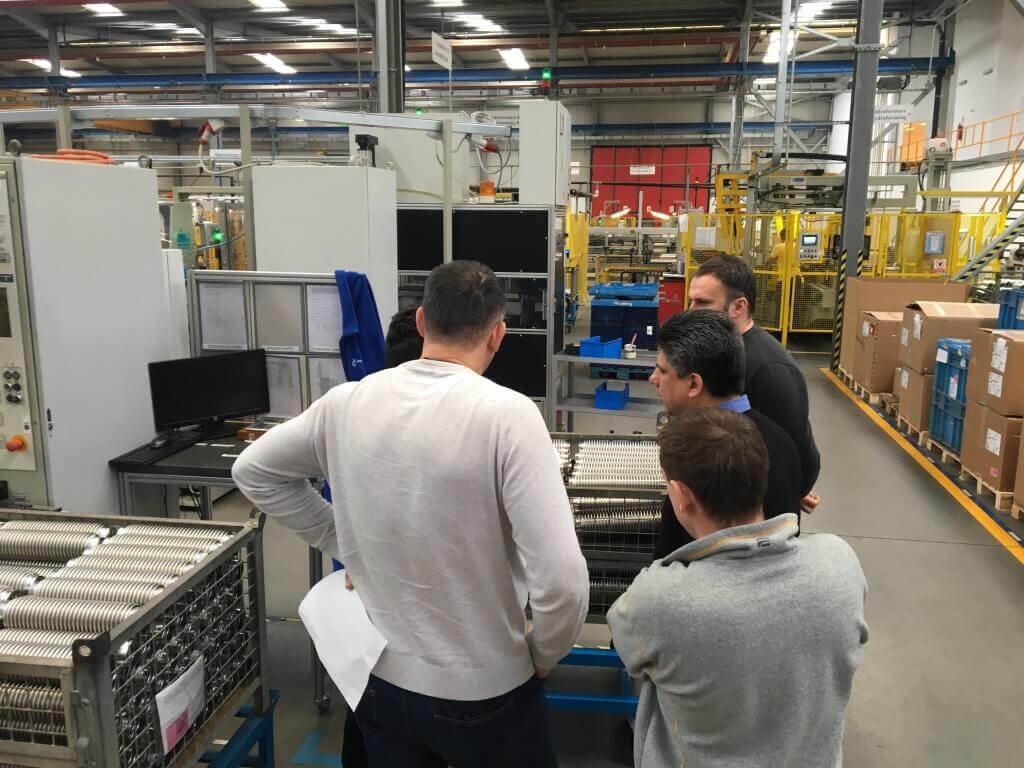
Real Case Examples
We will review examples of implementations from other companies
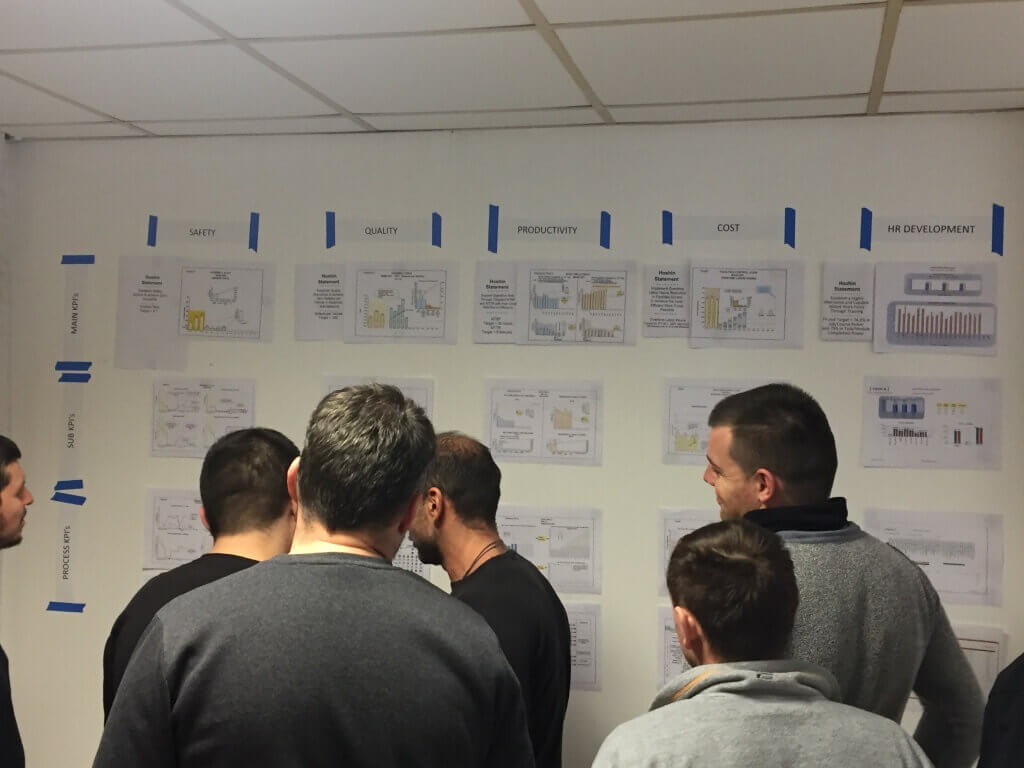
Team Work + Guidelines for your own Implementation
We will have teamwork exercises and plan for your own implementation
Explain the concept and practical implementation of the 8 steps process, in order to learn how to identify, analyze, solve, and prevent problems.
Participants split into teams to perform activities on the shop floor and practice the concepts, working in real processes & problems, with coaching provided throughout the steps.
8D Approach
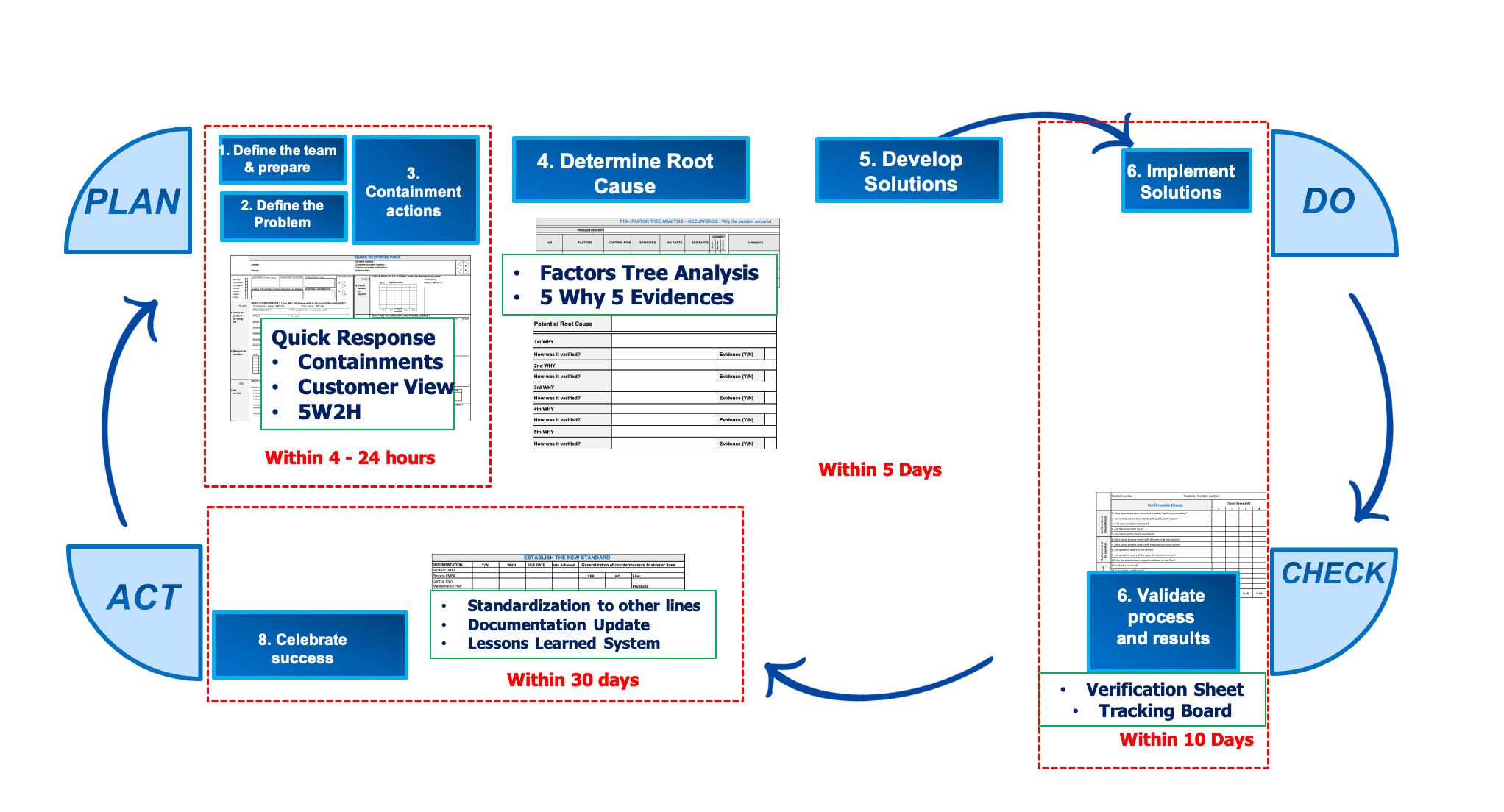
Training Length: 3 days
Aimed to: General Managers, Managers & Leaders in Maintenance, Manufacturing, Engineering and Continuous improvement.
What we will practice:
- The attitude of reality-based management (the 3 reals)
- Discipline and logic to analyze problems
- Effectively identify the root cause and implement preventive action
- Evaluate the results and the process used to achieve those results
- Improve your actual problem-solving method to include a reliable way to identify problems, root causes, and eliminate systematic issues.
- Practice the steps to drive problem-solving in your own processes.
- Improve discipline and logic to analyze problems
- Effectively identify the root cause and implement preventive action
- Evaluate the results and the processes used to achieve those results
Instructed by seasoned Lean Coaches
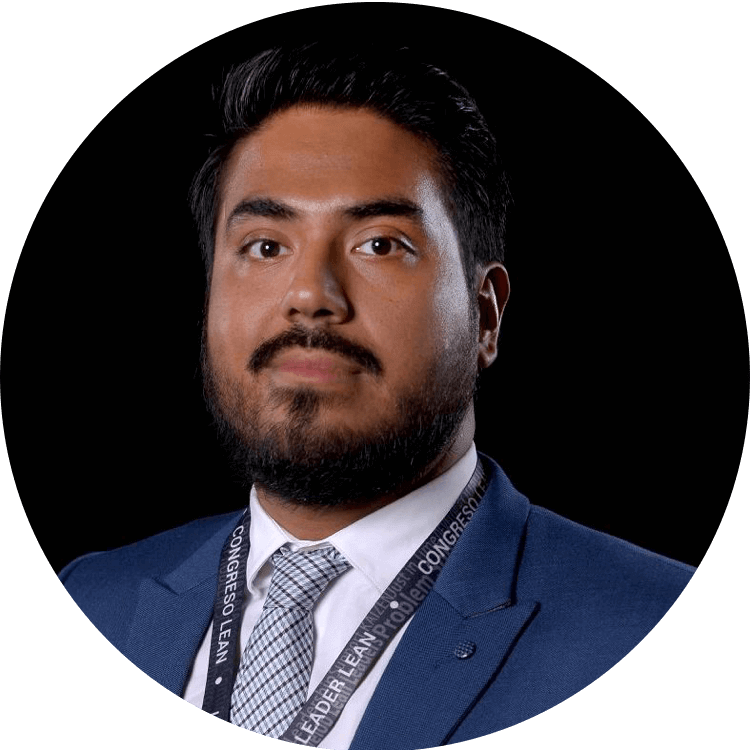
Edgar Cardenas
Lean Advisor & Coach – Europe Operations Director
Edgar has worked the last years in countries like Romania, Hungary, Russia, Mexico, Colombia, Spain and USA…, providing support to companies on their improvement journey based on developing teams to improve the quality of people & processes, in several industries including: Automotive, Electronics manufacturing, Food & Beverages, Plastics, Shared Service Centers, logistic services, among others.
He recently provide support to companies like Bosch, Hino Motors, Mercedes Benz, Kimball, Zebra technologies, Takata, Inteva Products, Dawn Foods, BOA, Mars, Rubbermaid, Faist Group, Emerson, Exide, Harsha Engineers, Steelcase..
-
Lean for Business Processes corporate trainer for several companies
-
Operational Excellence speaker at several international Lean Conferences & Summits.
-
He has developed in Lean Management over 1000 managers & leaders
-
Certified as Lean Practitioner & Six Sigma´s Black Belt by the IIE, Atlanta , Georgia.
-
Edgar has received direct coaching and professional development from renowned leaders like:, Ritsuo Shingo (Former Toyota President ), PhD. Jeffrey Liker (The Toyota Way), Gary Convis (Former VP at Toyota N.A. )
DO YOU WANT TO GO FURTHER? WE CAN ANSWER ANY QUESTION
Lean Manufacturing, 5s, Visual management, 8D Problem Solving, Problem Solving Training, 8D Training, Curs 8D, training 8D, PDCA training, 8D Principles, Problem Solving Principles, Problem Solving Implementation, Lean Training