Total Productive Maintenance (TPM)
Start the Lean Journey with this program for better shop-floor Equipment efficiency, Up-time, and Cost management.
In-Field TPM Training

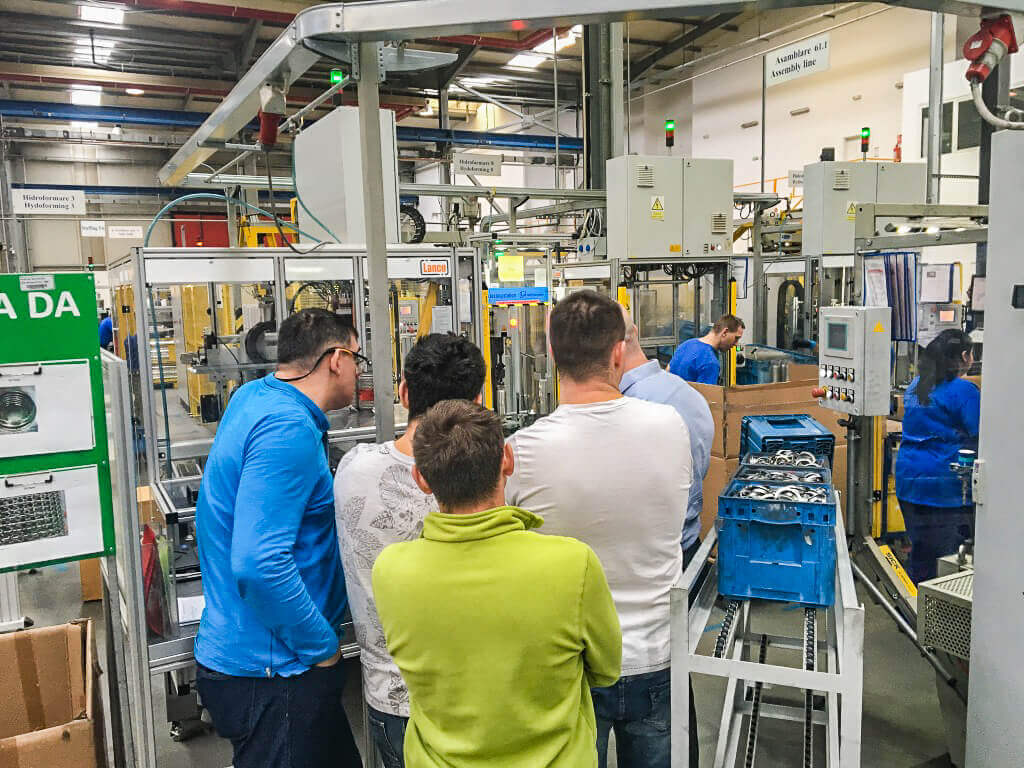
Why Total Productive Maintenance (TPM)?
50 years ago Toyota recognized that the key to manufacturing success is when the machinery performs as expected from the design specifications.
The base of a successful production system is Total Productive Maintenance also know as Toyota Productive Maintenance.
Many manufacturers soon realize in their pursuit of Lean that poor productivity is their main barrier to manufacturing excellence.
This training will give participants the foundation necessary to start the first steps of the TPM implementation and review best practices used by Toyota and other manufacturers.
Learn how to increase your equipment availability
Participants will split into teams to perform activities in the shop floor and present their observations
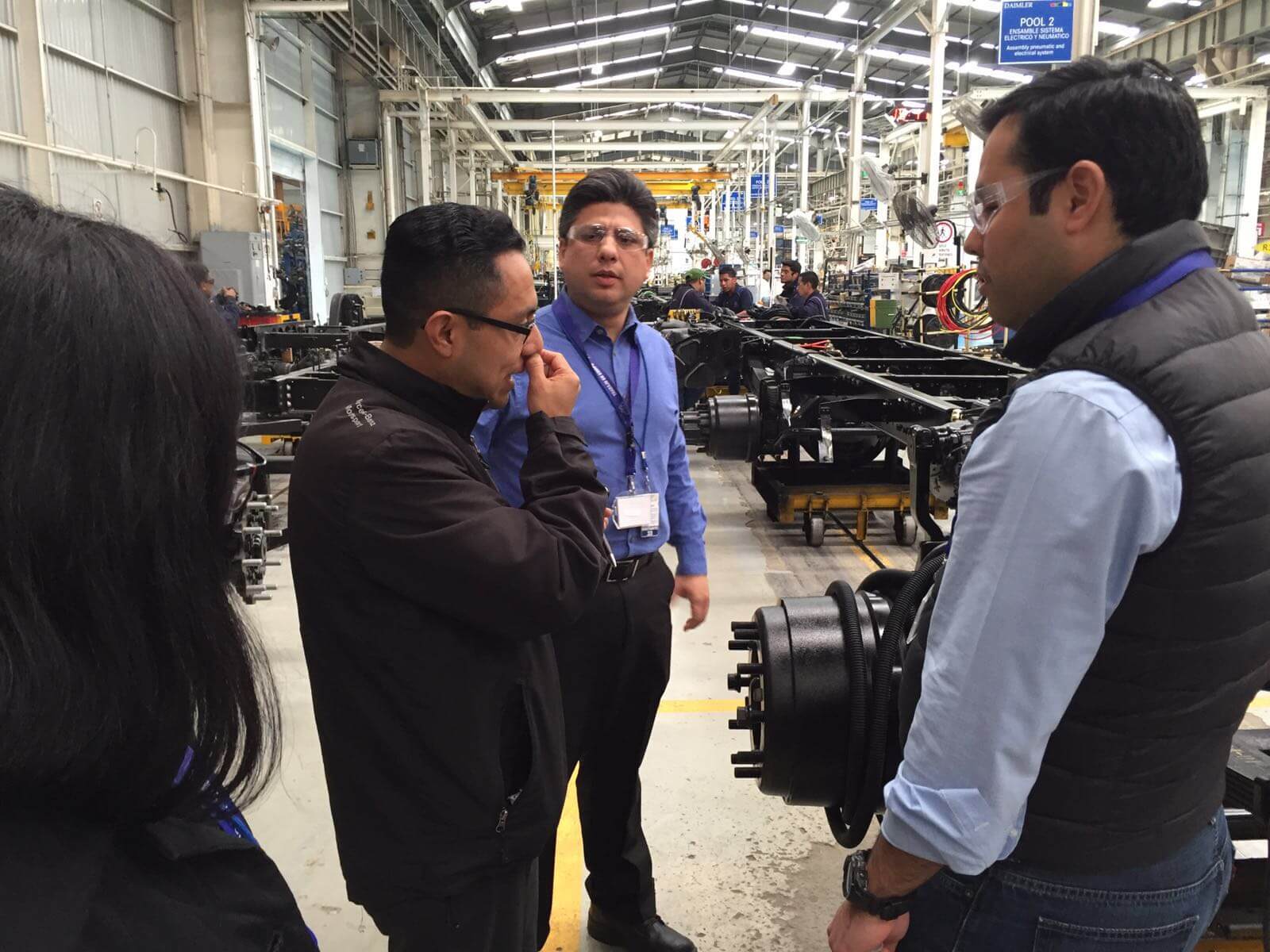
Understand the Toyota TPM System
Identify and analyze the operational losses using TPM management tools and structure.
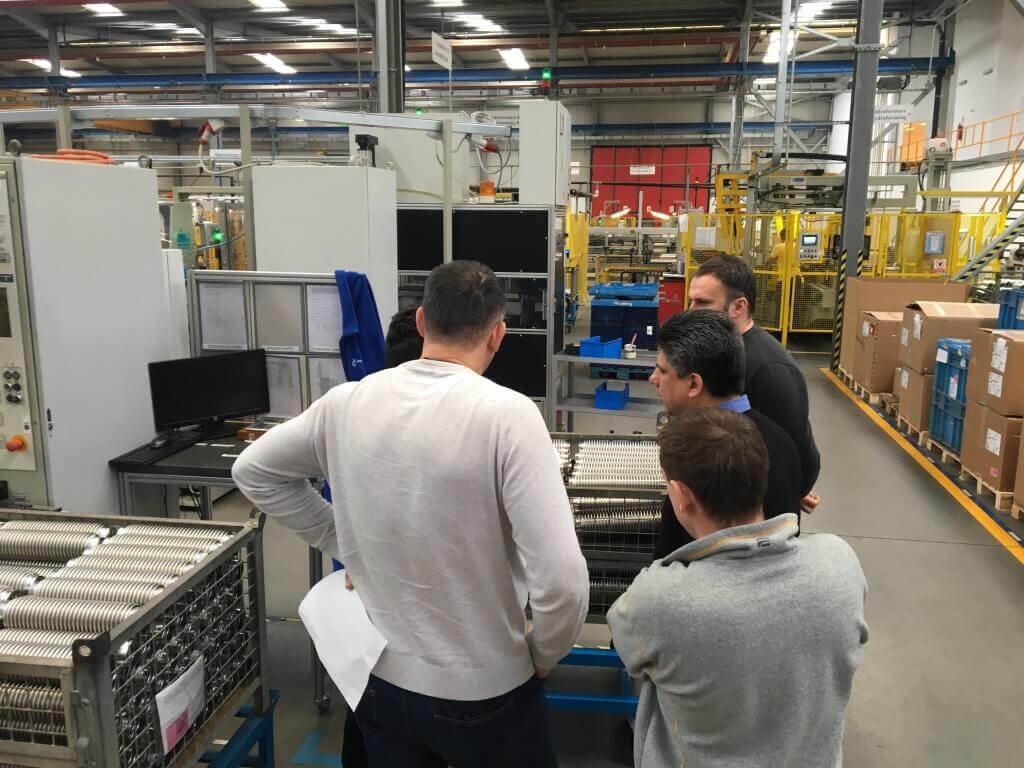
Real Shop floor applications
We will exercise different TPM concepts directly on the host plant processes
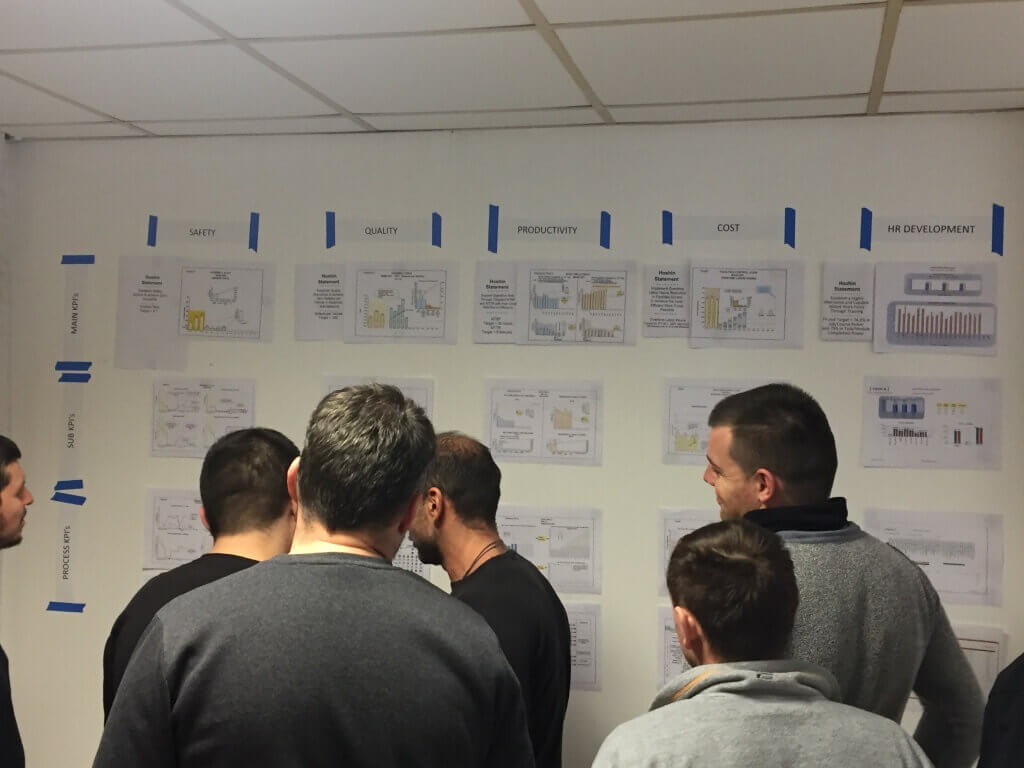
Toyota & other companies TPM Examples
We will review examples of implementations from other companies
Total productive maintenance (TPM) aims to maximize the entire equipment life cycle in order to achieve the highest operational availability.
Language: Romanian
Training Length: 3 days
Aimed to: General Managers, Managers & Leaders in Maintenance, Manufacturing, Engineering and Continuous improvement.
What we will practice:
-
How to manage the TPM Elements in the equipment lifecycle
-
Practical examples from Toyota and others managing the TPM
-
Step by step Guidelines for your own TPM implementation
-
Learn how TPM improves the teamwork of between departments
- Learn why TPM gives a strong foundation for operational excellence
- Overview on how to implement a Working Management System for TPM Management
- Clear guidelines to Implement the first TPM deliverables on your facility
Approach:
-
TPM Training is oriented to develop solid Maintenance Management practices.
-
All the content is related as a whole Management System, as part of the General Production System.
-
This Training is not oriented to learn or develop technical skills (e.g. repair a motor, program a Robot, etc).
Training Agenda:
- The 4 Pillars of TPM activity. Toyota Total Productive Maintenance (TPM) Toyota’s Japanese Original version.
- 12 Important Items for TPM Management. Toyota’s Japanese Original version
- Toyota Total Productive Maintenance Visual Elements to Facilitate Operation and Maintenance
- 5 Senses on the Shop Floor.
- Autonomous Maintenance: Steps for Implementing Operator’s Maintenance
- Visual Preventive Maintenance.
- Human Resources for TPM
- Fundamental Concepts: 4 major items for Team Leader Role
- Toyota Floor Management Development System for Maintenance Management
- Strategy to Implement TPM on the plant
Do you want to go further? we can answer any question
Mentenanta Autonoma, Managementul Mentenantei, Mentenanta Preventiva, Mentenanta Productiva Totala, Maintenance, Tpm, Lean Maintenance, Mentenanta, Mttr, Mtbr, Oee, Mentenanta Preventiva, Mentenanta Productiva Totala, Mentenenta Preventiva, Mentenanta Correctiva, Mentenanta Autonoma, Cost Reduction, Mentenanta Preventiva Si Mentenanta Productiva Totala (Tpm), Mentenanţă Şi Mentenabilitate, Loss Prevention, Ooe Improvement, Eficienta Echipamentul, Timpul Mediu De Reparare, Timpul Mediu Intre Defectari, Lean TPM, Lean Manufacturing, 5s, Visual management, TPM Indicatorii, mentenabilitate, MTTR, MTBR, breakdown analysis, timp stationare,