Toyota Kata In Field Training
Leaders coaching disciplined problem-solving.
Toyota Kata In Field Training
Leaders coaching disciplined problem-solving.
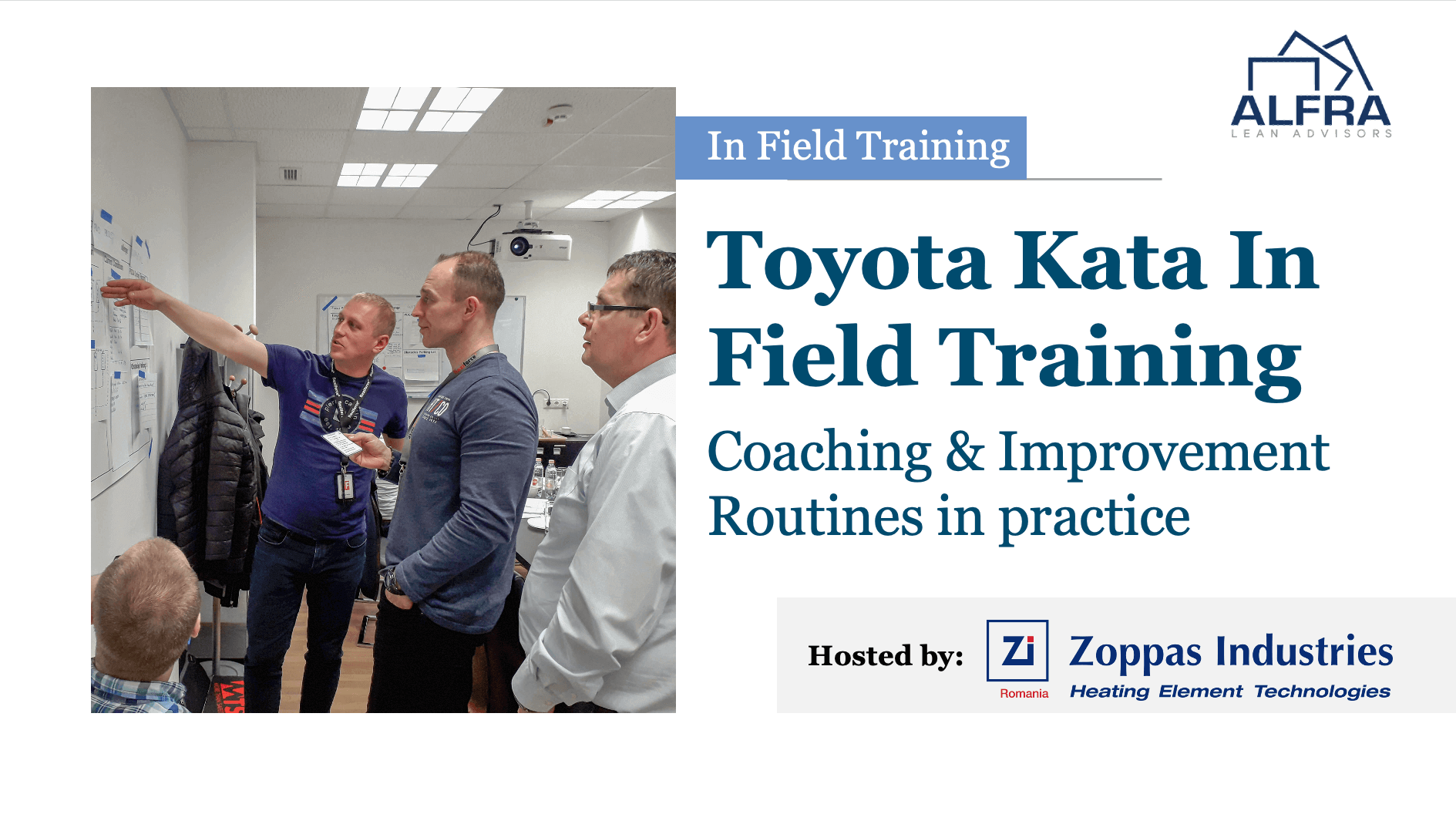
Develop your leaders as problem solvers and coaches of the improvement journey.
Toyota Kata is a management system that provides the means to achieve two important objectives:
A methodology to achieve challenging objectives that are currently beyond a team’s ability to reach, and developing leaders as coaches for creating a culture of continuous improvement. This is done through simple & time-efficient, daily routines.
In Field Toyota Kata Training at Host Plant
The Improvement Kata
A systematic four-step pattern for managing teams. Practicing it helps any team get better at meeting goals and challenges.
The Coaching Kata
A set of teaching routines that help you develop coaching skills. It is a coaching pattern that helps managers teach critical thinking and acting.
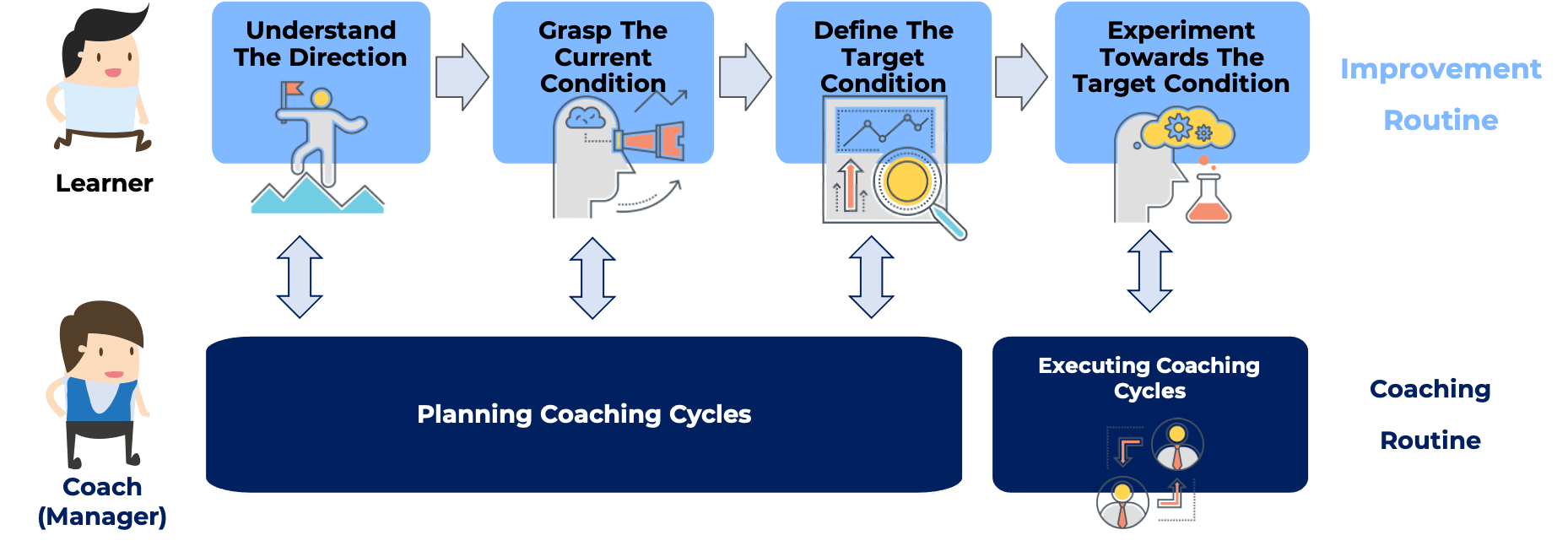
When: 23, 24 & 25 November 2022
Where: Sannicolau Mare, Timis, Romania
Who should attend? Senior managers, leaders and middle managers that are interested in creating a sustainable culture of continuous improvement through use of the cutting edge management methodology of Toyota Kata.
Key benefits
You will learn the fundamental concepts of how to apply the improvement and coaching routines in your organization
- Providing a systematic, scientific routine that can be applied to any problem or challenge.
- Commonizing how the members of an organization development solutions.
- Migrating managers toward a role of coach and mentor, by having them practice coaching cycles.
- Framing PDCA in a way that has people taking small steps every day
TRAINING AGENDA
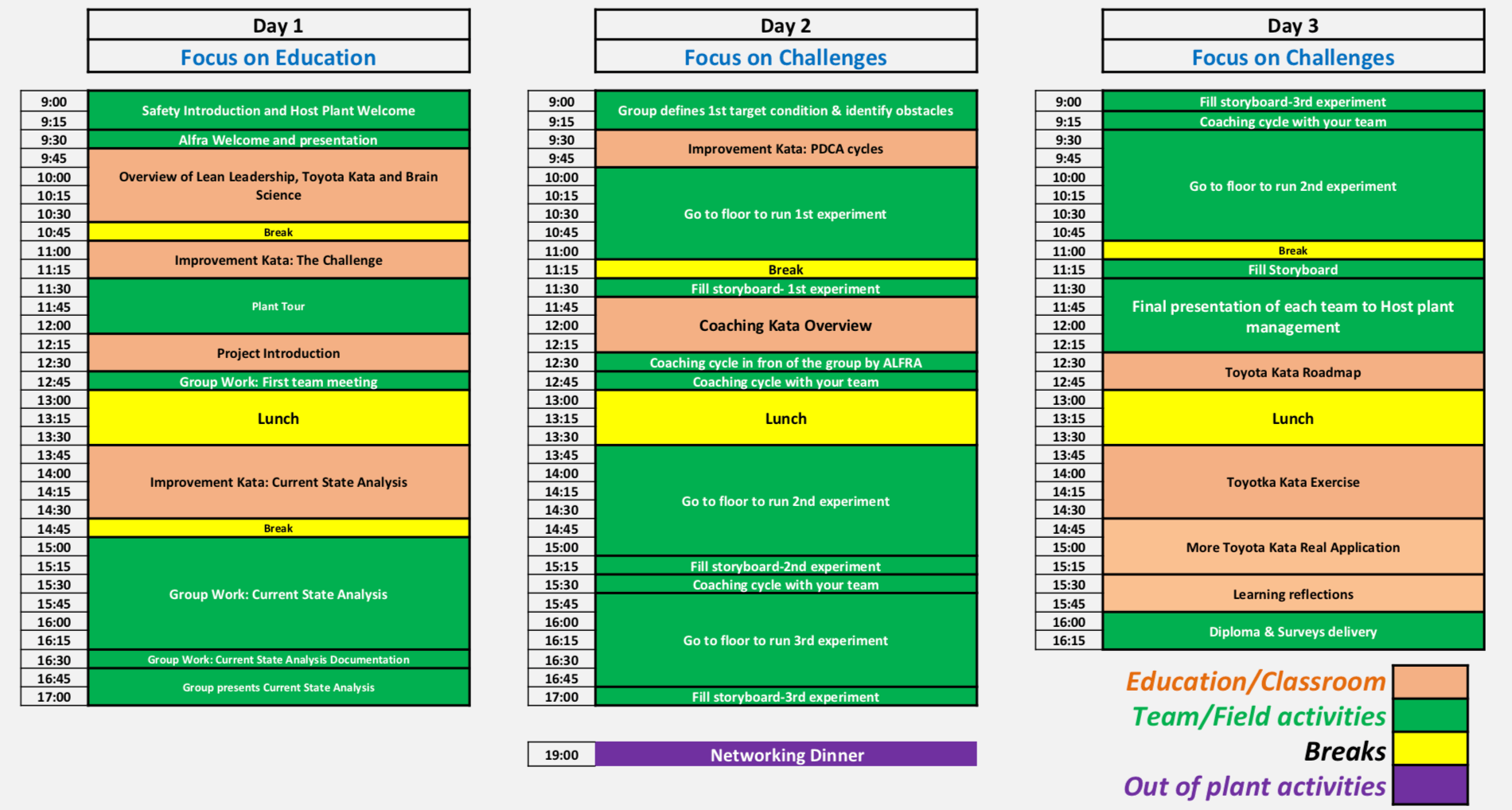
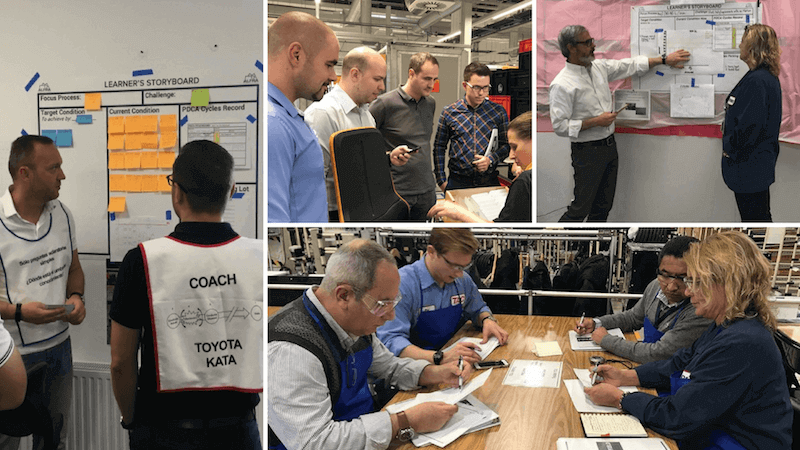
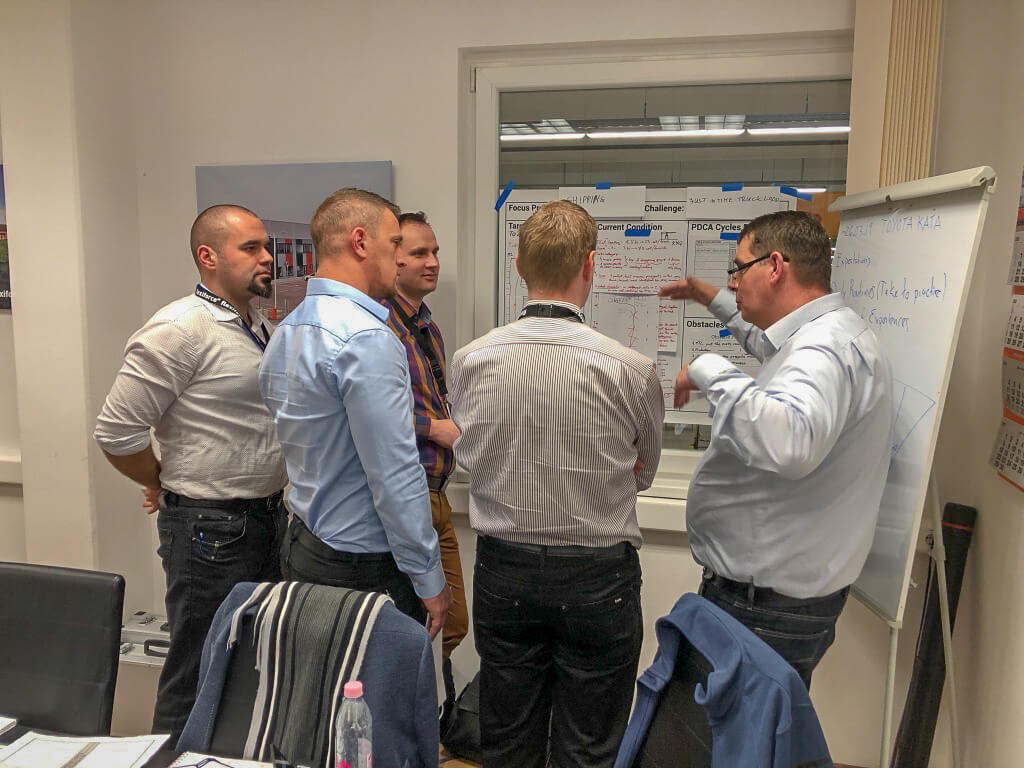
Practice the Kata
Practice several rounds the improvement and coaching Kata receiving feedback from ALFRA Coaches
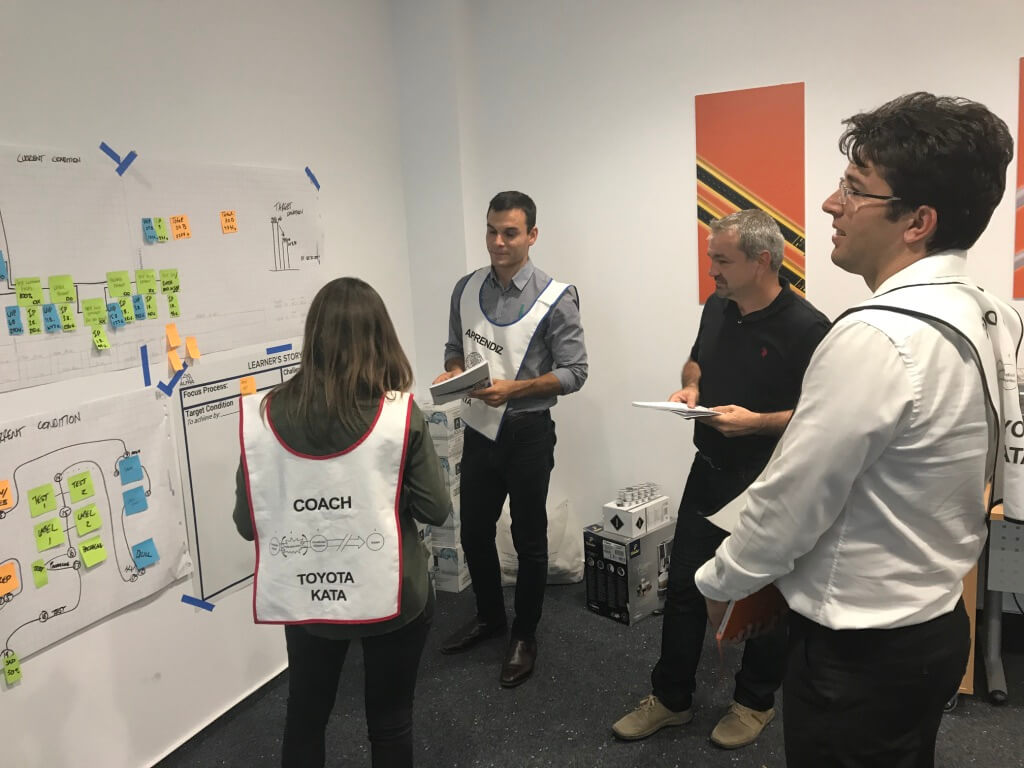
Group Discussions
Learn & share experiences with managers from different industries, with team based activities.

Shop Floor Implementation
Perform experiments and coaching cycles on the shop floor from the host company
Host Company: Zoppas Industries – Timis, Romania
Zoppas Industries is a global supplier for the design, manufacture, and sale on the world market of heating elements and systems for domestic and industrial use.
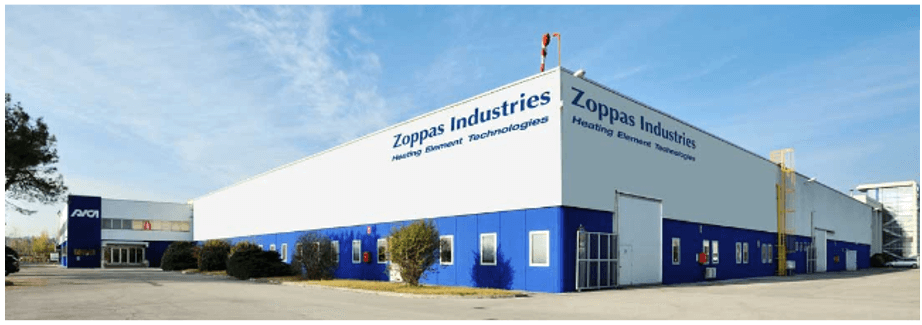
Recent Workshops:
Receive the brochure with all details in your email
Coaching, Leadership, Lean, Toyota, Kata, Development, Problem Solving, 8D, Lean Management, PDCA, Scientific thinking, process improvement,