Value Stream Mapping & Design in Field Training
Manage your company operations in order to improve the flow of value to your customers.

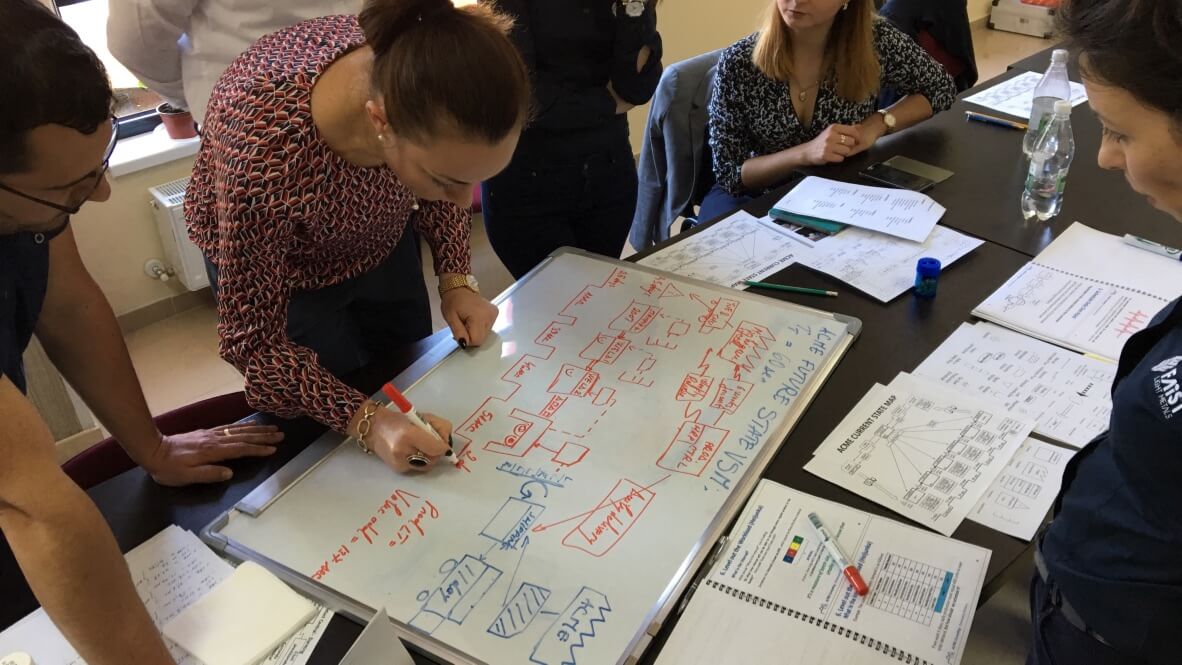
Developing a “Lean production system” will allow us to focus on delivering the maximum value to our customers.
We will explain the concept and practical implementation of Value Stream Mapping & Design, in order to plan and implement improvement activities. We will also analyze the material and information flow for the selected pilot process, in order to identify the main opportunities and develop a value stream design (Lean value stream plan).
Identify main opportunities and design a lean value stream
Participants will split into teams during the VSM training to perform activities on the shop floor and present their observations.
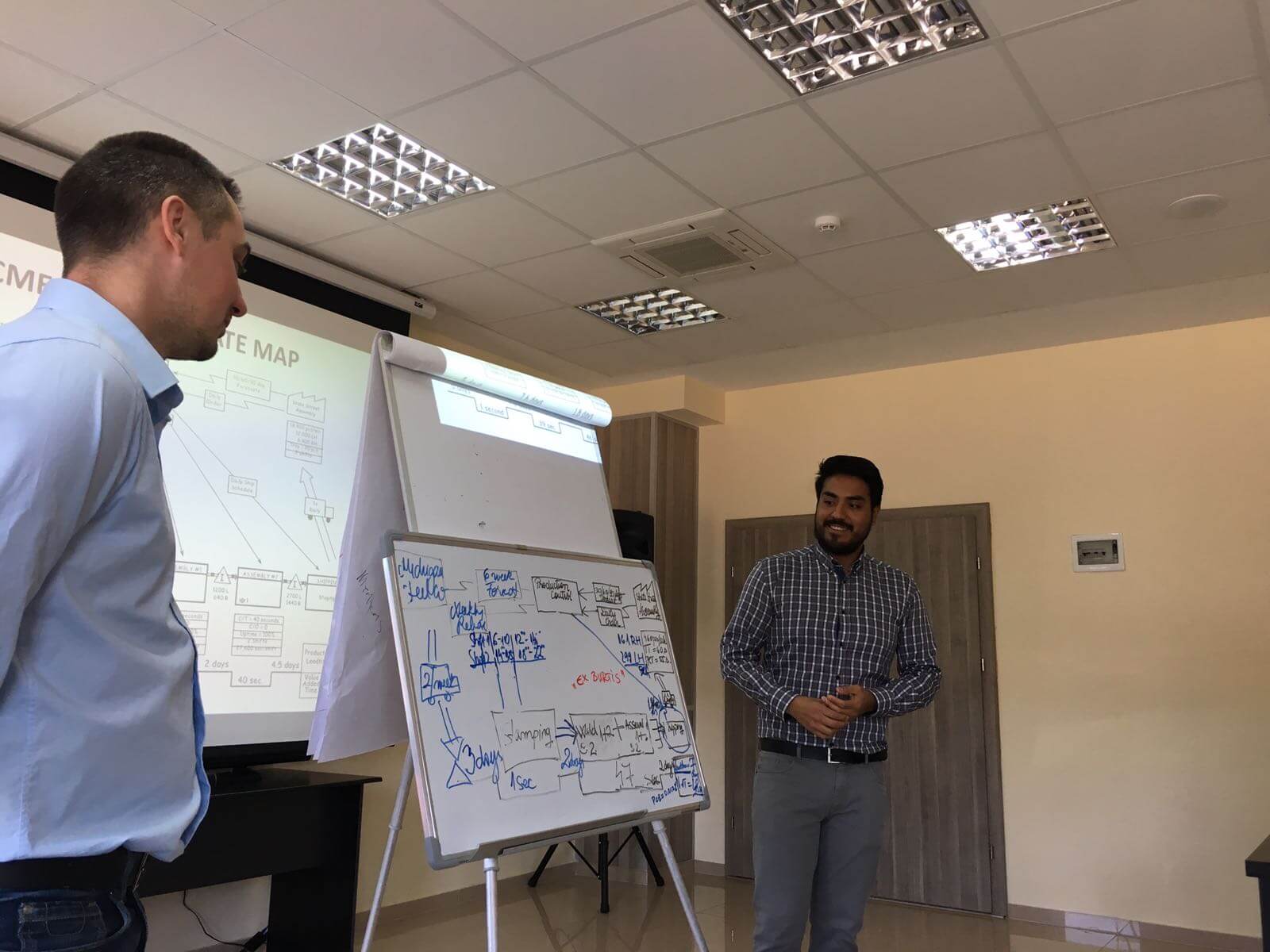
Practical Learning
Learn the concepts from examples, group exercises and trainers’ experience
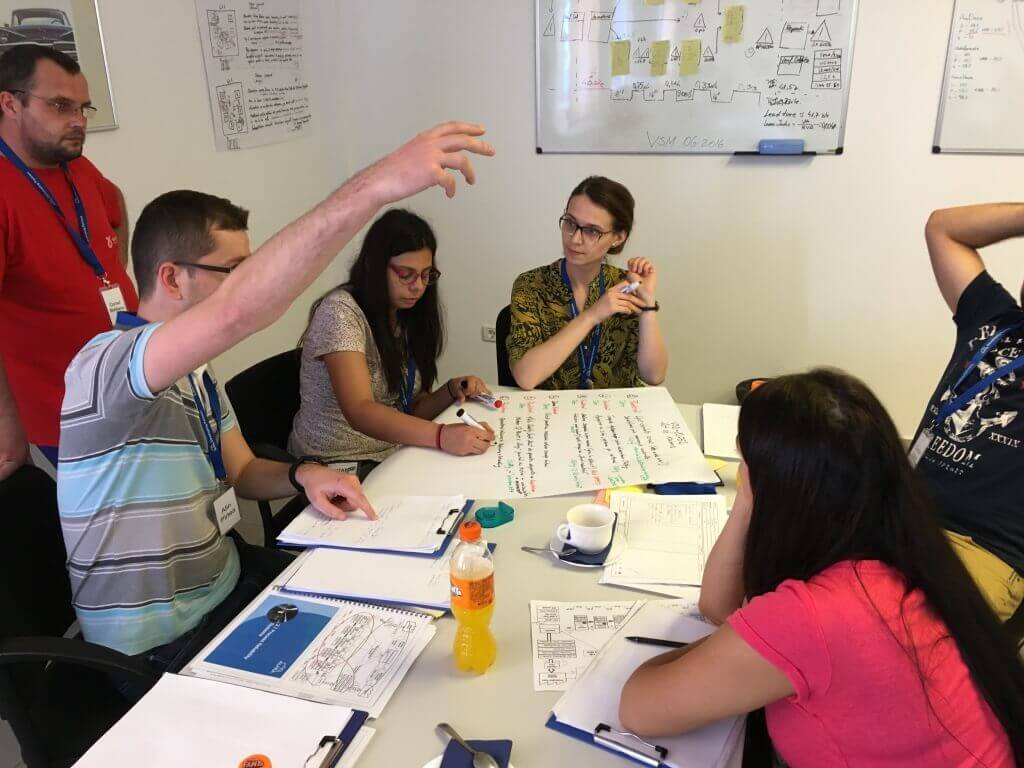
Group Discussion
Share experiences with managers from different industries and background
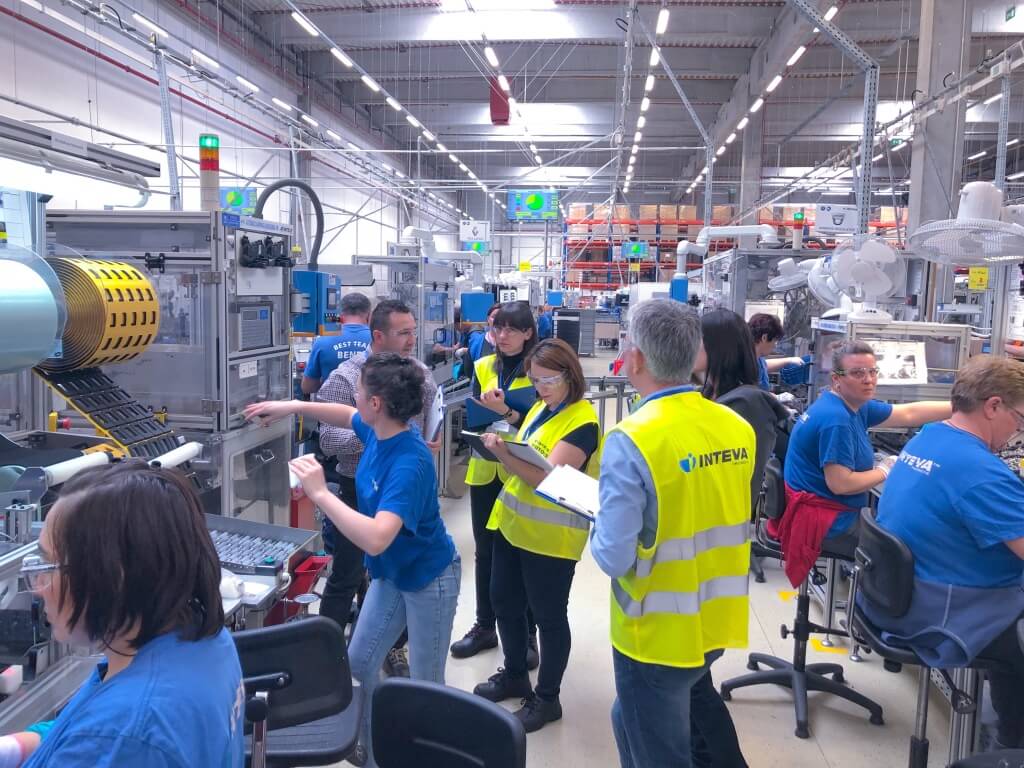
Shop Floor Exercises
The training is hosted by a factory, with activities direct in the process area
Who should attend?
Managers and members of operational departments (production, quality, engineering, lean ..), and functional (HR, project management ..).
Why participate:
- Learn how to develop the Value Stream Mapping method
- Identify the main sources of waste in the flow of materials and information
- Develop a comprehensive Value Stream Design proposal (Action Plan + Guide)
- The relationship with the potential implementation benefits in terms of inventory, delivery, quality, space, costs, safety.
– Learn how to develop the Value Stream Mapping method
– Identify the main sources of risk in the flow of materials and information
– Develop a full Value Stream Design proposal (Action Plan + Guide)
– Learn about the potential benefits of deployment in terms of stock, delivery, quality, space, costs, safety.
Training agenda:
- Principles of Lean Production System
- Definition of values and losses in production processes
- Push and Pull Systems – Kaizen
- Why management through Value Streams
- Product families, development of product family matrices
- Demand analysis and identification of pacemaker
- Lean indicators for production processes
- Analysis of values and classification of activities
- Yamazumi, SIPOC & amp; Spaghetti Charts
- Identifying the main product families (high runners)
- Collecting process indicators
- Value analysis for process steps
- Information flow analysis (supply, production planning, warehousing, production, delivery)
- Workload and process analysis
- Command analysis and tact time analysis
- Inventory of raw material, subassembly and finished product
- ABC (High Volume Low Mix) case
- Darming Case (Services)
- NovoLance case (Product Launch)
- Summary of performance indicators (Lead time, Quality,% Value)
- Analysis of the current state vs. target state
- Developing ideas for improvement & amp; VSM development-future state
- Requirements to achieve the proposed future status (At process and company level)
– How to develop the Value Stream Mapping method
– Identify the main sources of waste in the flow of materials and information
– Develop a comprehensive Value Stream Design proposal (Action Plan + Guide)
– Implementation-related potential benefits ratio in terms of inventory, delivery, quality, space, costs, safety.
- Value Stream Design Principles
- Development of implementation proposals and impact / effort matrix
- Development and agreement of the action plan
- Presentation of the “Future State Map” for the Lean process
- The ratio of potential benefits (financial and cultural)
Instructed by seasoned Lean Coaches
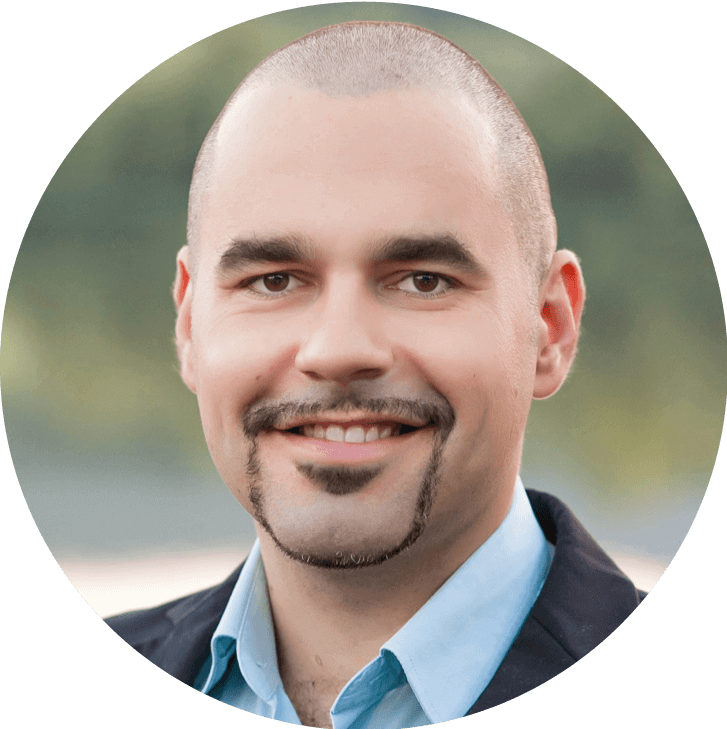
Laszlo Seres
Former EMEA Lean Manager & Coach
László has deep experience in automotive industry in different countries (Germany, Hungary, Romania..) from middle level to EMEA management position . He was responsible for supporting and establishing different functions like Industrial Engineering, Maintenance and Operational Excellence, with focus on developing the people and teams in these areas.
László has 10 years of experience working in several countries like Hungary, Germany, Spain, Romania, Macedonia and Ukraine working for companies like BOSCH, TAKATA or Joyson Safety Systems
He coached people in the entire organization to ensure proactive continues improvement and problem solving attitude.
He is the Co-founder of Lean Process Development Engineer program at University of Miskolc.
Main expertise:
- People development with Coaching & Improvement Kata method
- Problem Solving development programs & Coaching
- Supporting the implementation of TPM system
- Production system planning, Industrial engineering, Material & Information Flow management
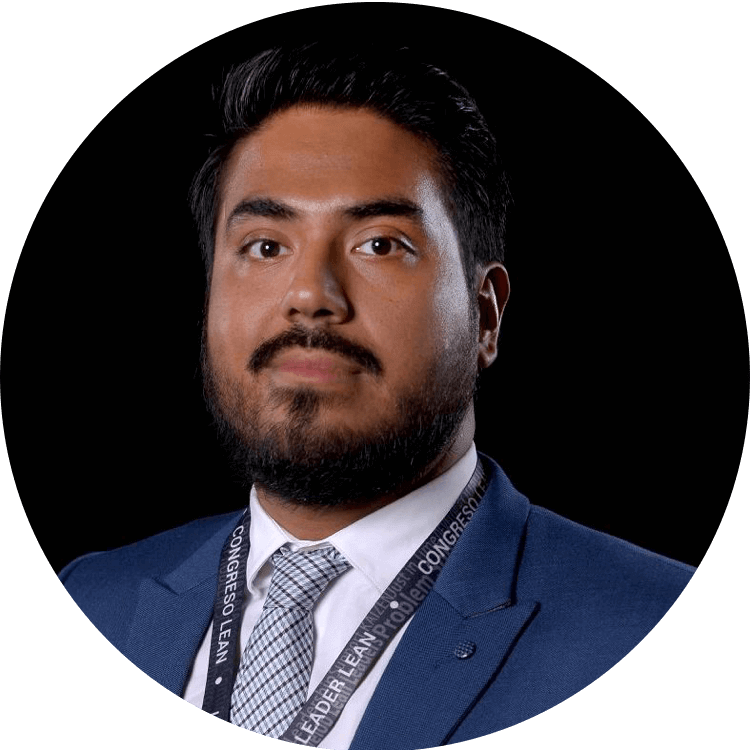
Edgar Cardenas
Lean Advisor & Coach – Europe Operations Director
Edgar has work the last years in countries like Romania, Hungary, Russia, Mexico, Colombia, Spain and USA…, providing support to companies on their improvement journey based on developing teams to improve the quality of people & processes, in several industries including: Automotive, Electronics manufacturing, Food & Beverages, Plastics, Shared Service Centers, logistic services, among others.
He recently provide support to companies like Bosch, Hino Motors, Mercedes Benz, Kimball, Zebra technologies, Takata, Inteva Products, Dawn Foods, BOA, Mars, Rubbermaid, Faist Group, Emerson, Exide, Harsha Engineers, Steelcase..
-
Lean for Business Processes corporate trainer for several companies
-
Operational Excellence speaker at several international Lean Conferences & Summits.
-
He has developed in Lean Management over 1000 managers & leaders
-
Certified as Lean Practitioner & Six Sigma´s Black Belt by the IIE, Atlanta , Georgia.
-
Edgar has received direct coaching and professional development from renowned leaders like:, Ritsuo Shingo (Former Toyota President ), PhD. Jeffrey Liker (The Toyota Way), Gary Convis (Former VP at Toyota N.A. )
Abordarea Value Stream Mapping & Design
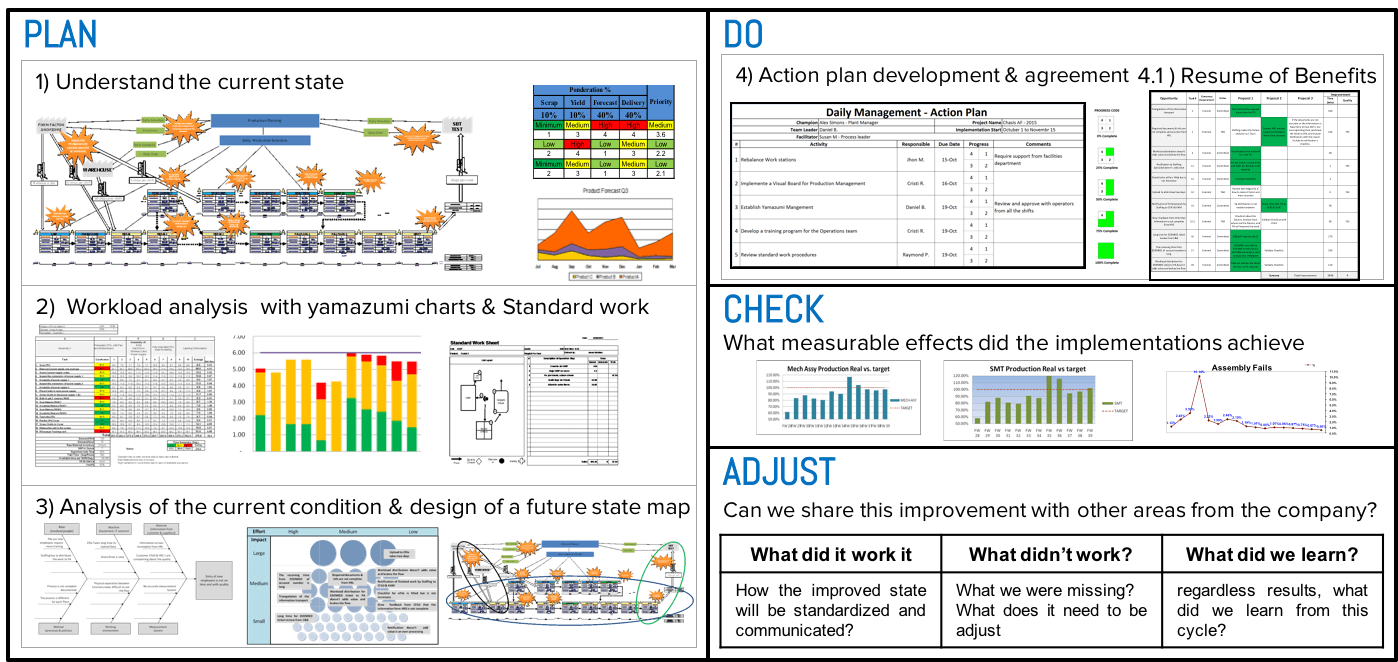