Why Lean Manufacturing
A new approach for Production Management
The Lean management system (founded on the Toyota Production System) is a management philosophy that shortens the time between the customer order and the product shipment by eliminating all inefficiencies (sources of waste).
This is ultimately reflected in terms of quality, delivery, cost, and greater team morale, making a company capable to overcome bigger challenges and their competitors.
Workshop Highlights:
This 3 days workshop is a practical way to present the Lean principles concepts and its implementation in the shop floor (Gemba) from our host plant.
This program aims to develop participants, to really understand the lean principles (know why), and systems which support the behaviors of an operational excellence enterprise, the structure and deployment strategy for an initial phase of a lean transformation, which systems must be deployed and which triggers must be developed, explaining how to measure the deployment based on behaviors, which will deliver good process and results in soft and hard benefits.
TRAINING ACTIVITIES
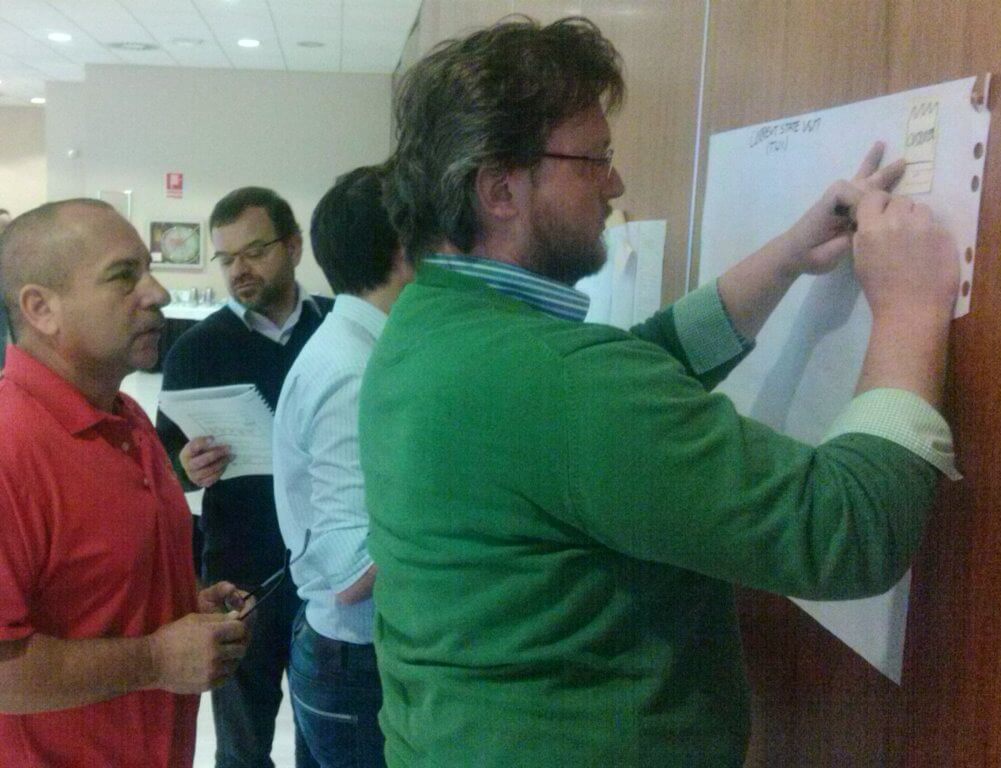
Real Value Stream Mapping
A powerful method to analyze & Identify the main opportunities from a process
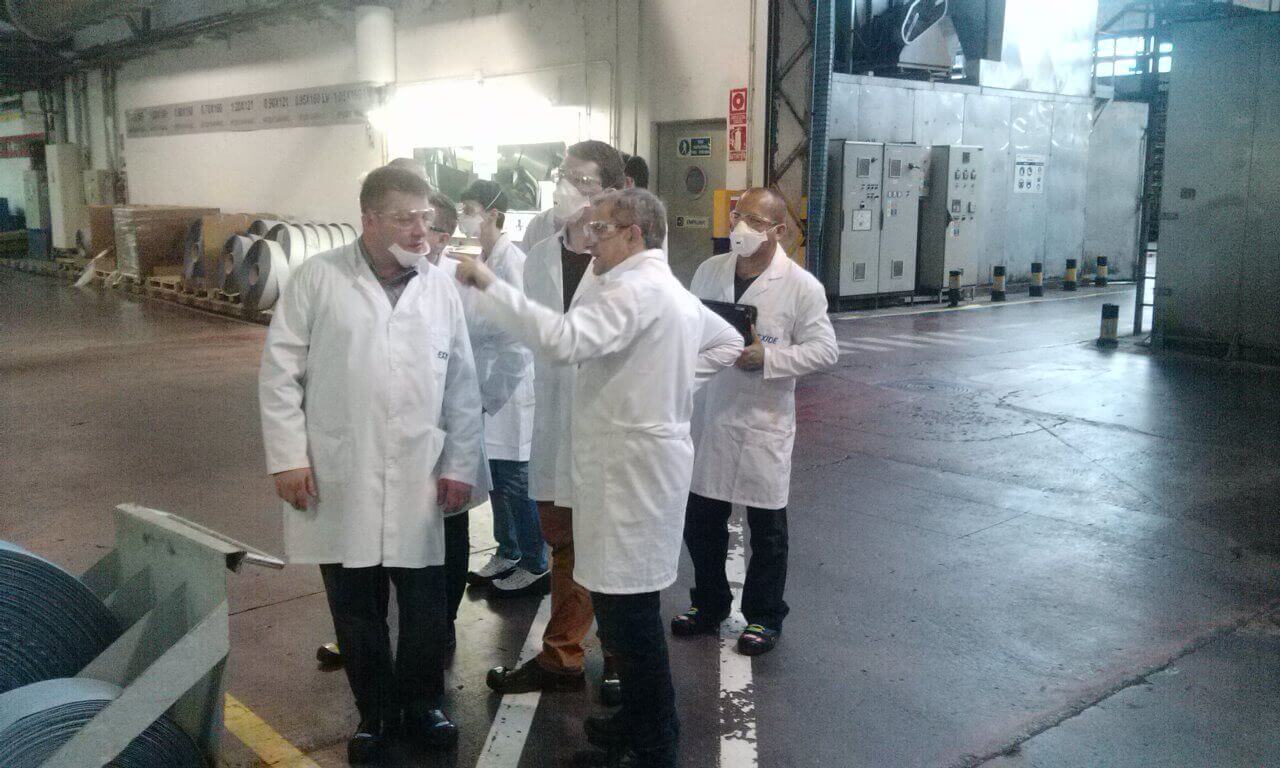
Shop floor (Gemba) Activities
Learn the Lean methods with practical team activities conducted on the shop floor.
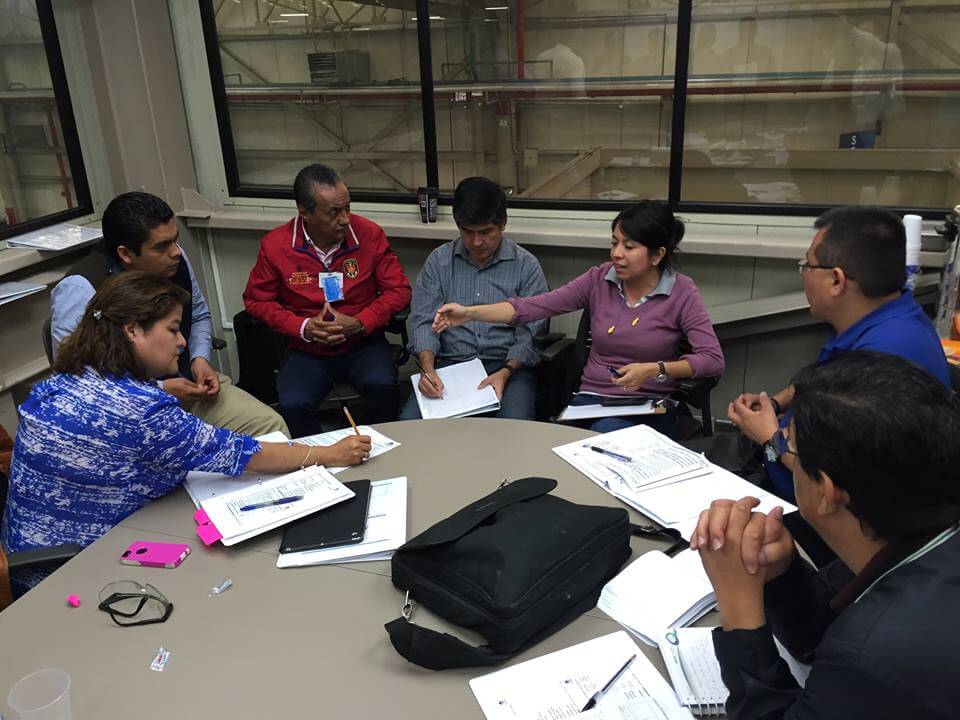
Improvement Planning and Management
Learn how to plan and coordinate the improvement efforts in an effective way
Training length: 24 hrs (3zile)
Who should particioate?
Managers of operational and support departments, average levels in production, quality and engineering, Lean practitioners.
Recommended industries:
-
-
Manufacturers: Automotive, Electrical / Electronic, Pharmaceutical, Food and Beverage, Printing, Plastics, among others.
-
Why participate?
- All exercises and applications are focused in real shop floor operations.
- Learn and receive direct feedback about Lean management from an experienced instructor
- Receive nurturing feedback from external participants from other industries
- Development of skills that can only be achieved by intensive practice and coaching.
Restrictions: External participants will sign a non-conflict of interest agreement, assuring they are not from a competitor company for the host company.
1) Identify key opportunities using Value Stream Mapping < / strong> to achieve continuous and global improvement Lean
2) Run and manage Kaizen cycles to improve quality , cost, delivery and safety with the help of the Lean philosophy
3) Establish Lean production methods and teams for long-lasting performance
TRAINING AGENDA: BODY OF KNOWLEDGE
- Manufacturing background & Toyota Production System
- Value definition for the complete enterprise
- 8 wastes for Manufacturing and transactional processes
- Differences between Push and Pull Systems
Gemba Exercise, going to production line for Value and Waste
- 5S phases, implementation tips & examples
- Visual Management for effective decision taking
- Standard Work concept & examples
Gemba Exercise, 5S and Visual Management, Standard Work Assessment and Improvement planning.
- Why Value Stream Management
- Lean Metrics for manufacturing processes
- Yamazumi, SIPOC & Spaghetti Charts
- Value Stream Mapping steps explanation
Gemba Exercise, development of a “VSM from Host Plant Process”
- One Piece Flow and Small Batch approaches
- Quality the source: Poka Yoke, Andon lights, Jidoka, how to assure first time quality.
- Just in Time Production and Replenishment: benefits of just in time production in inventory, space and lead time.
- Total Productive Maintenance Introduction
Gemba activities, OEE measurement evaluation and planning for Autonomous Maintenance introduction.
- Principles and benefits of SMED
Gemba activity, analysis and Improvement planning for a Change over process from the host plant
- Cell Manufacturing and Line Balancing Introduction: Create flexible manufacturing workplace, adapt it depending on the demand level, create different scenarios of workload.
- Explanation and types of the Pull Systems: how to implement pull systems depending on the process nature.
- Types of Kanban systems: calculation and implementation of Kanban signals to trigger the work.
- Heijunka and Production Leveling introduction: Concept, and benefits of a leveled production
- Analysis of information flow (production control, warehouse, manufacturing and shipping instructions)
- Development of improvement ideas & Future State VSM development
- Requirements to achieve Future State (Process and Enterprise level)
Gemba exercise, Host plant process improvement planning, development of a Future state Map for “Host company Process”, Development of Implementation proposals and Impact/effort matrix
Discussion in how to embrace the Lean culture in your organization.
- The True North
- Gemba Walk –Managing from the Gemba
- Daily Meetings & Performance review
Gemba exercise, Gemba walk definition
PARTICIPANTS OPINION
Training objectives on the plant
- Practical shop floor training in Lean principles and methods on the shop floor from our host plant with team based activities, participants get immerse into a kaizen teams.
- Analyze and develop a Value Stream Map from an entire production process (Selected by Host)
- Identify the main sources of waste in the entire process from a strategic point of view.
- Develop an action plan to establish a “Lean Production” System.
Do you want to go further? we can answer any question
CONTACT US
Instructor
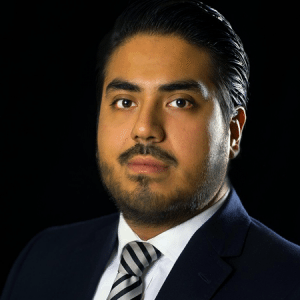
Edgar Cardenas Sanchez
International experience (Americas & Europe) in operational excellence deployment & training, for manufacturing & service environments, helping several customers to develop people & processes on their lean transformation journey , in several industry sectors including: Electronic Manufacturing, Food, Financial services, Plastics, Automotive, Logistics services, among others.
-
Co-developer of the Toyota Way assessment Model.
-
Lean Office corporate trainer for several companies (manufacturing and services) Depth training at OpEX Shingo Prize Model Assessment (2011 v.)He has consulted several companies, driving improvement initiatives & projects using Lean principles and systems deployment.
- Development Leader for the Lean Manufacturing E- Training and Lean Manufacturing Simulator Material
- Operational Excellence speaker at Mexico IIE Conferences and International Engineering Summits. He has trained on site in Lean Thinking over than 600 engineers and managers.
- Received development in Lean Leadership, Hoshin Kanri and Cultural change by PhD. Jeffrey Liker (The Toyota Way) & Gary Convis (Former VP at Toyota N.A. )
- Experience on Theory of Constraints to elevate systems throughput, also capable on Strategic Planning using TOC´s Thinking Process.
- Former Lean & Six Sigma Team Member for the RIM CFT from Celestica Monterrey. Former Associated Financial Vice President for the Institute of Industrial Engineers (IIE) Mexico Region.
- Certified Lean Practitioner by the IIE, Atlanta , Georgia
- Certified Six Sigma´s Black Belt by the IIE, Atlanta , Georgia
- Industrial Engineer BA degree from the U.A.N.L.