Daily Management Development System
Align and engage all the company levels to go beyond the “typical” Lean implementation
9-11 July, In-field Training at Inteva Salonta

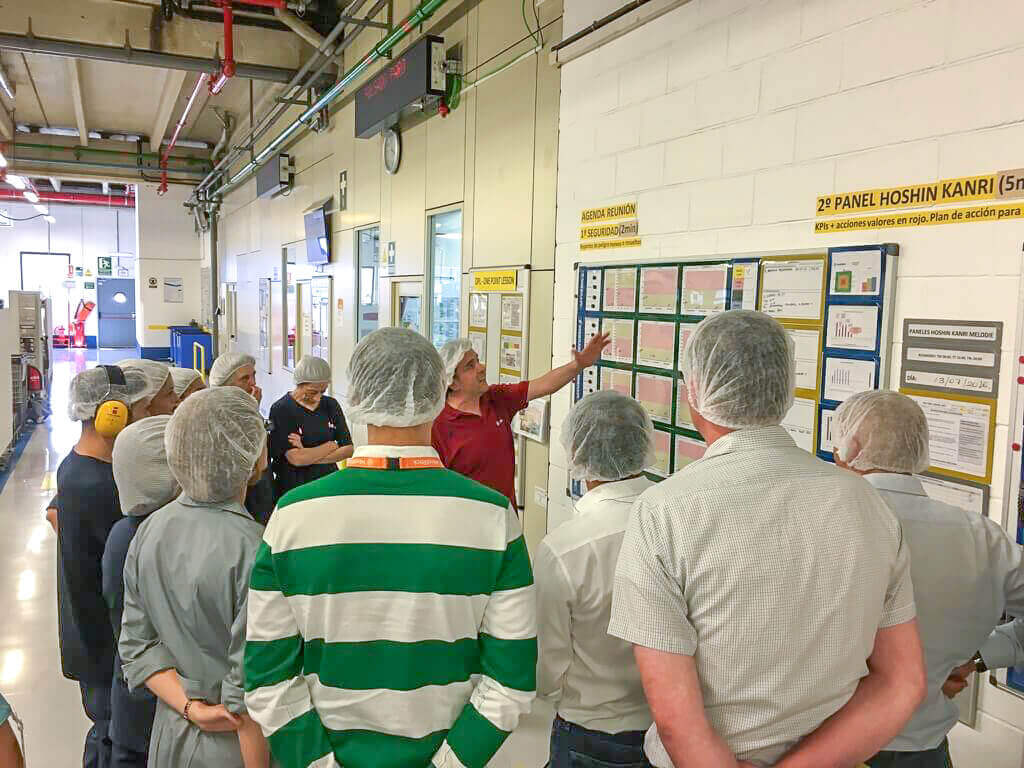
This program address the factors to get you out of the improvement trap
Most companies embarking on a lean journey soon become frustrated with improvement events and isolated projects that yield great short-term results but have no sustainability and no major innovation.
They are searching for something more: the culture that goes beyond “just managing” continuous improvement.
Align & deploy actions across the organization to achieve your objectives
Participants will split into teams to perform activities in the shop floor and present their observations
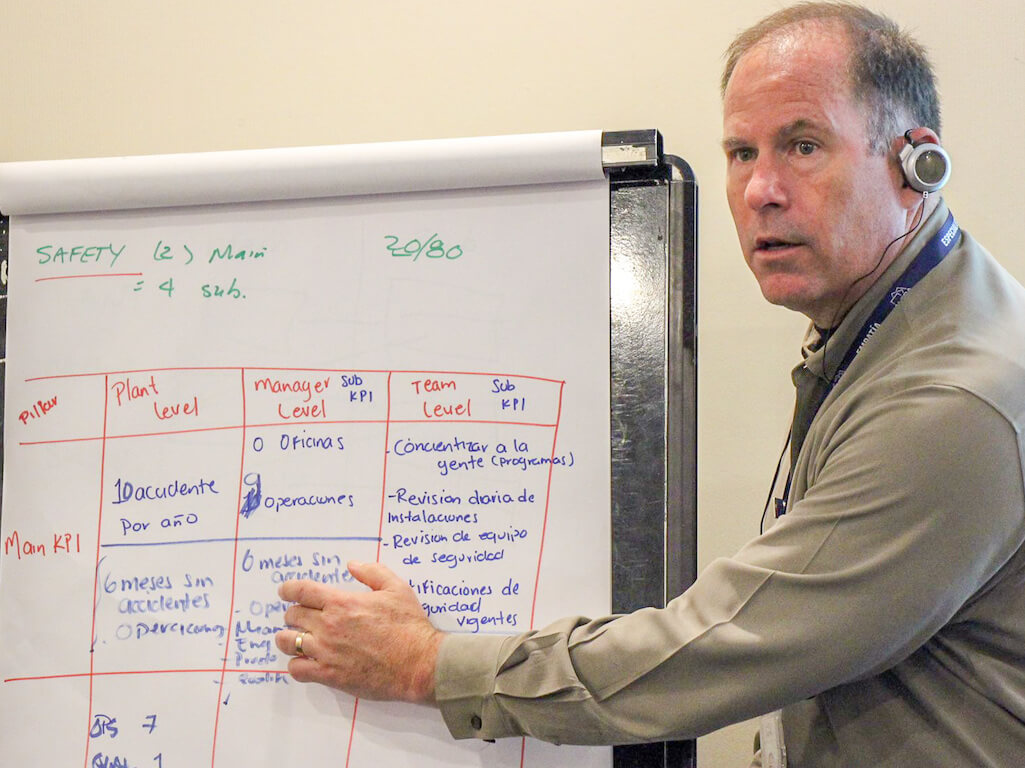
Practical Learning
Learn the concepts from Toyota examples, group exercises and trainer’s experience
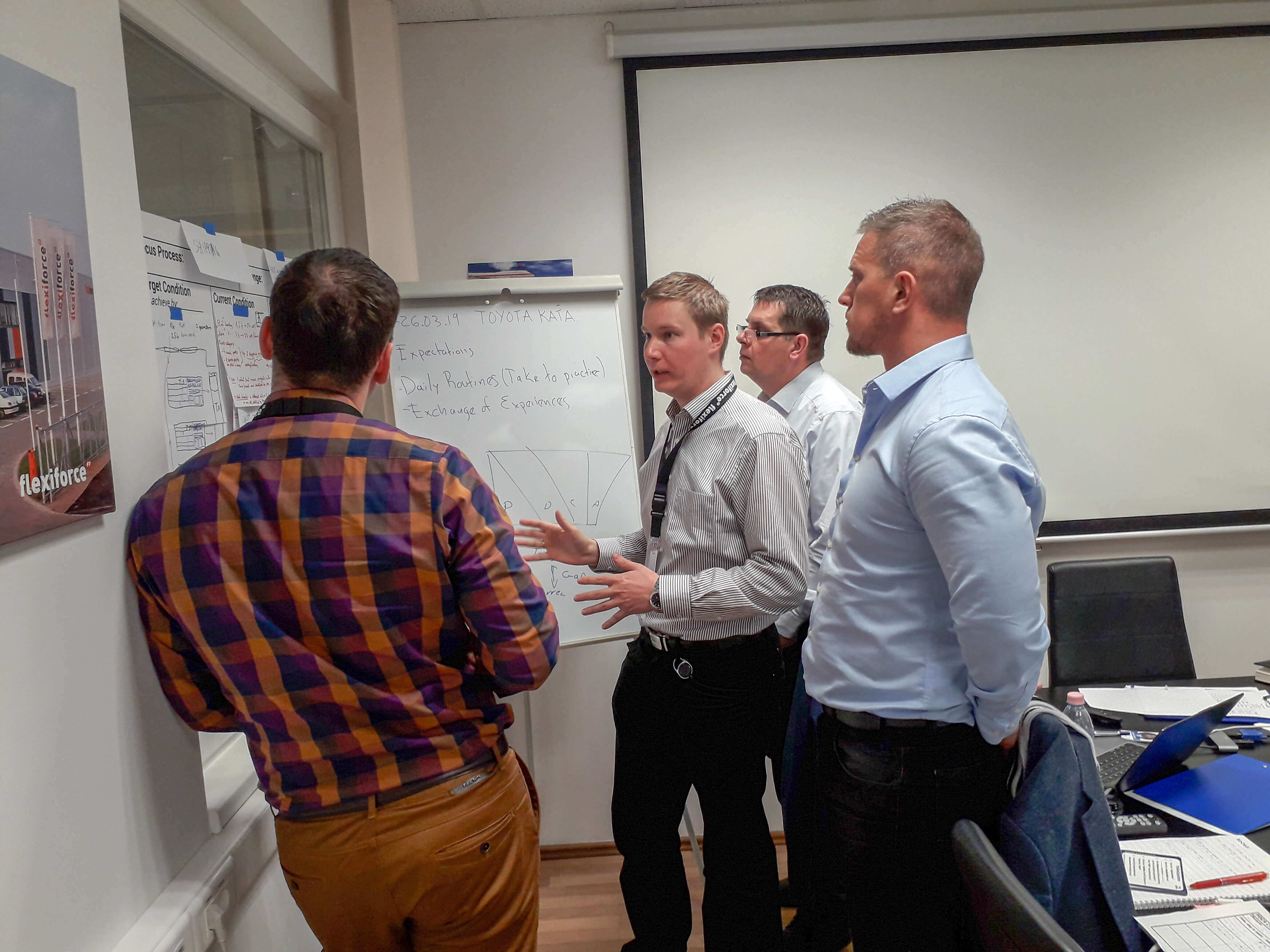
Group Discussion
Share experiences with managers from different industries and background
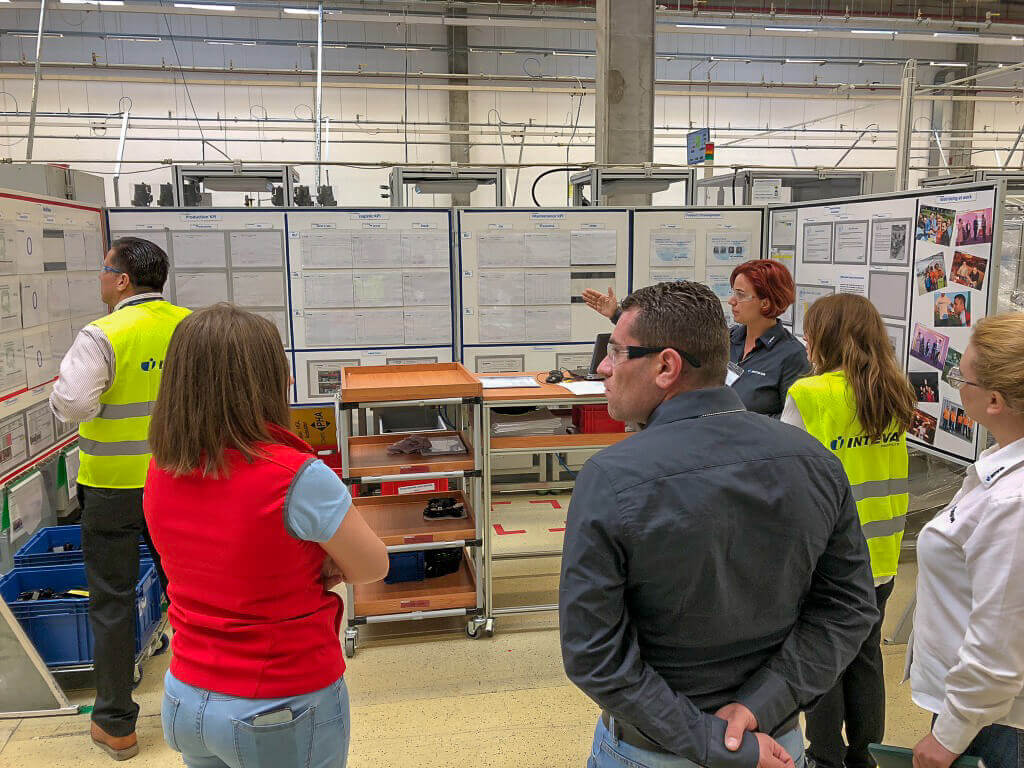
Shop Floor Exercises
The training is hosted by a factory, with activities direct in the process area
Instructed by seasoned Lean Coaches
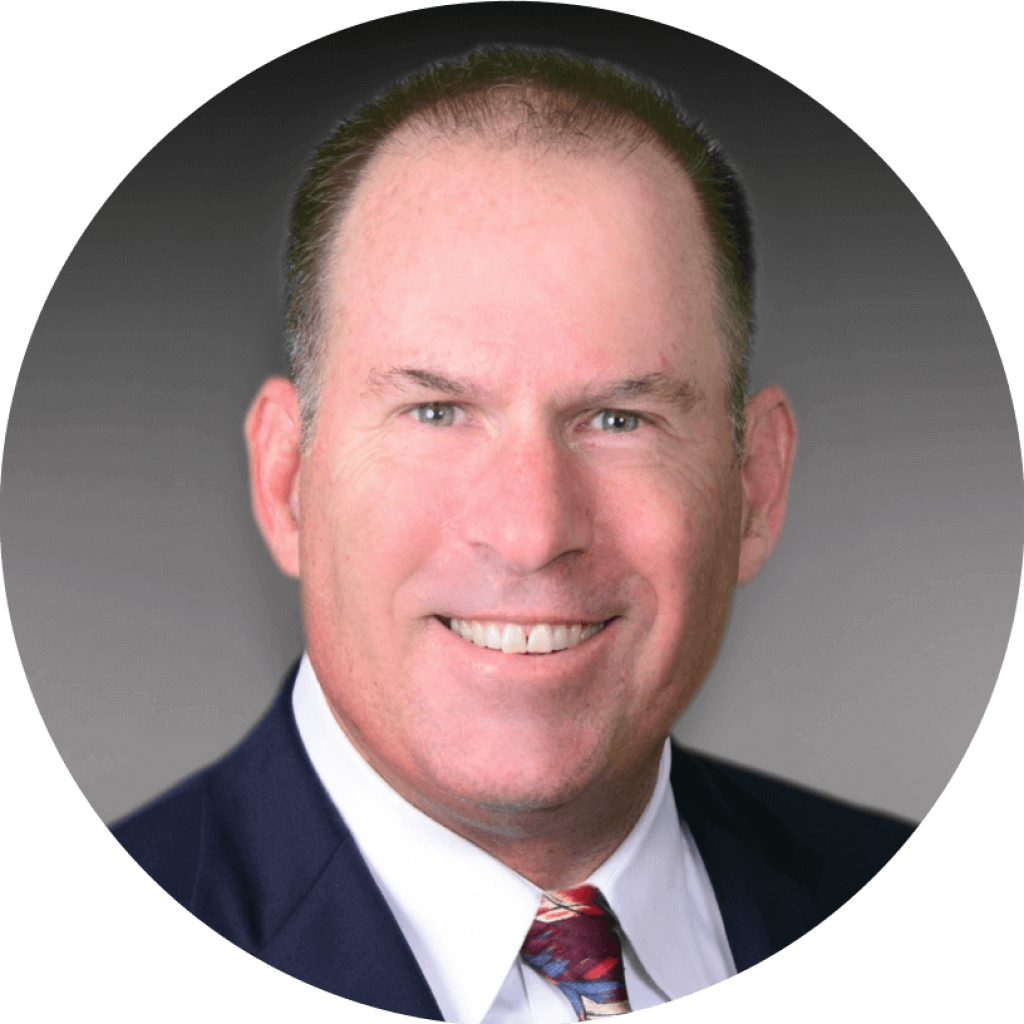
Jeff Strabala
Former Toyota Manager & Operations Management Expert
Jeff worked for Toyota for over 21 years; his extensive experience is based in Operations Management in Toyota North America as Manager and internal consultant.
Jeff was member of the Leadership team for the launch of two “Greenfield” automotive plants and subsequent plant capacity expansions valued in $4.2 billion USD. During his tenure at Toyota, Jeff also spent 3 years of “internal consulting” with improvement projects at Toyota and Tier 1 suppliers.
Project General Manager (Consultant) – Toyota OMDD
- Internal consulting position, Investigation, Analysis, and Improvement of floor operations applying core Toyota Production Systems tools.
Vice President – FIC America Corp
- Led Supply Chain, Conveyance Operations, Project Planning, Production Control, Human Resources, IT, Accounting and General Affairs/Purchasing teams for 2-plant manufacturing operation in Automotive Tier 1 supply.
- Systems and Processes put in place reduced plant Overtime 25%, while simultaneously reducing delivery delays & errors 80% saving over $3million annually.
Project General Manager – Toyota North America.
- Improved Safety Systems for Toyota’s MS manufacturing plant through active initiatives to educate plant personnel revise and introduce new programs, establish management accountability through daily reporting and monthly performance meetings, introduced gated safety management process that reduced TIR by 50% within 6 months.
- Developed, Validated comprehensive [all functions] Safety Metrics during 2013 New Generation Corolla launch, resulted in improved safety KPI during launch, Metrics, tracking and reporting adopted in North American Region.
Assistant General Manager-Toyota
- Responsible for Plant Manufacturing Operations, member of Executive Team,
Primary responsibility for Production Control, Supply Chain & Logistics, Project Management for 8 Model changes, Plant Manpower Productivity planning and reporting. - Supported Toyota Production System training and application, and Visual Management (FMDS) roll out at TMMBC, management Mentor.
Manager, Production Control – Toyota (TMMBC & TMMI)
- Production Control Planning & Coordination of Operations for Toyota truck factory with multiple product lines 2000 -2003.
- Additional collateral duties involved management of TMMI Corporate Strategy and Reporting, TPS Training Group, Manpower Planning and Productivity group.
Manager Accounting & Finance, Toyota TMMI
- Started up Accounting & Finance operations for Greenfield Toyota plant in Indiana, responsible for accounting, internal and government compliance, budgeting and cost reduction efforts.

Edgar Cardenas
Lean Advisor & Coach – Europe ALFRA Operations Director
Edgar has work in the several years in different Romania, Hungary, Russia, Mexico, Colombia, Spain, USA, providing support to companies on their improvement journey based on developing teams to improve the quality of people & processes, in several industries including: Automotive, Electronics manufacturing, Food & Beverages, Plastics, Shared Service Centers, logistic services, among others.
He recently provide support to companies like Bosch, Hino Motors, Mercedes Benz, Kimball, Zebra technologies, Takata, Inteva Products, Dawn Foods, BOA, Mars, Rubbermaid, Faist Group, Emerson, Exide, Harsha Engineers, Steelcase..
-
Lean for Business Processes corporate trainer for several companies
-
Operational Excellence speaker at several international Lean Conferences & Summits.
-
He has developed in Lean Management over 1000 managers & leaders
-
Certified as Lean Practitioner & Six Sigma´s Black Belt by the IIE, Atlanta , Georgia.
-
Edgar has received direct coaching and professional development from renowned leaders like:, Ritsuo Shingo (Former Toyota President ), PhD. Jeffrey Liker (The Toyota Way), Gary Convis (Former VP at Toyota N.A. )
Host Plant: Inteva Products
Committed to the highest standard for quality, Inteva meets all customer requirements and expectations. The company is focused on total commitment toward the continuous improvement of products and processes. Inteva employs over 15,000 team members in 18 countries. Inteva World Headquarters is in Troy, Michigan.
Inteva Products Salonta Plant produces latches, window regulators and mechanical cables for several world class automakers. Salonta site has being in the lean journey for several years, achieving tangible benefits in performance, developing the teamwork to solve any kind of issue and continuously learning.
Our product lines include Closure Systems, Interior Systems, Motors & Electronics and Roof Systems, and we have more than 90 customers, including virtually all of the world’s leading global and regional automakers.
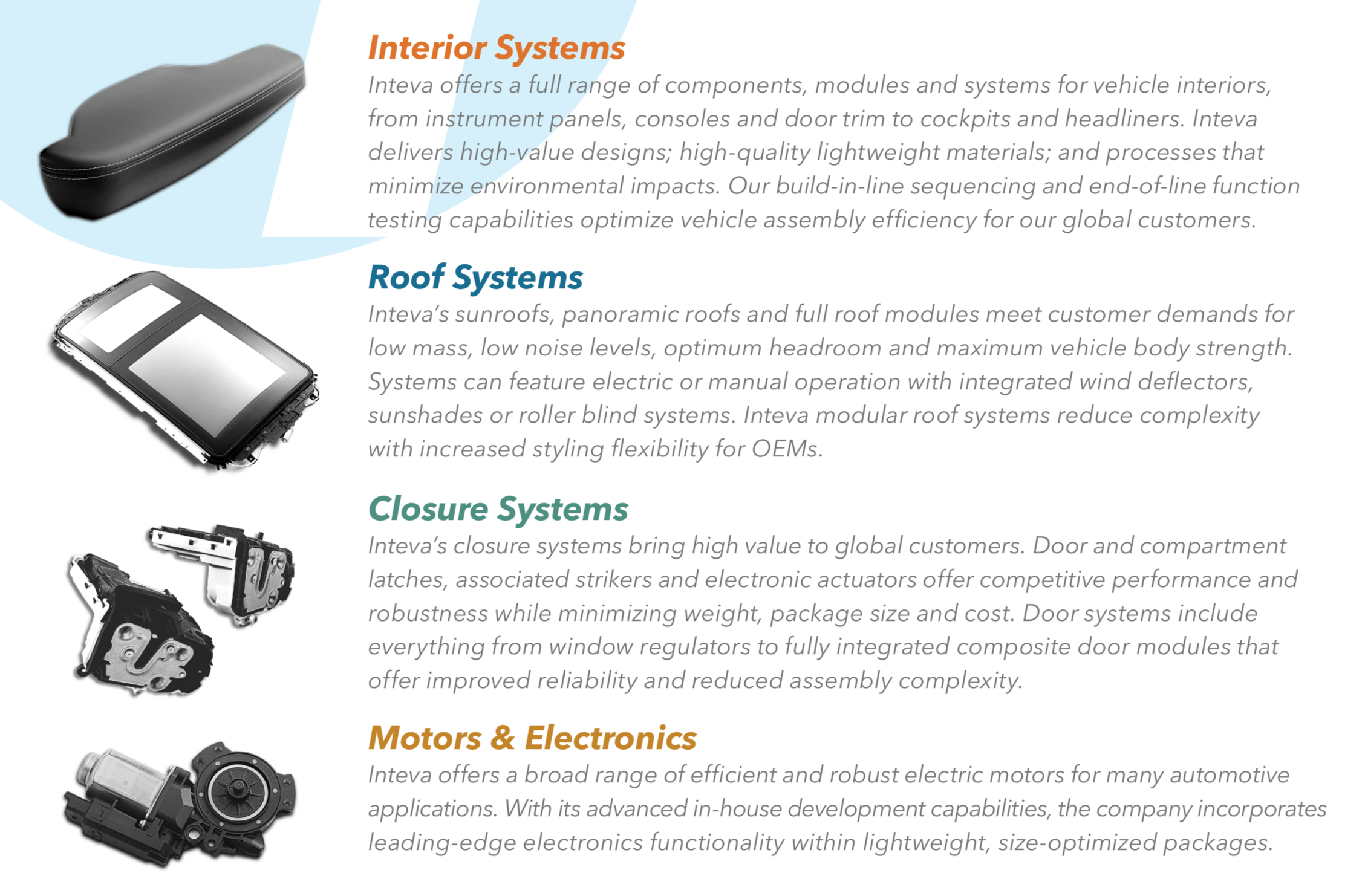
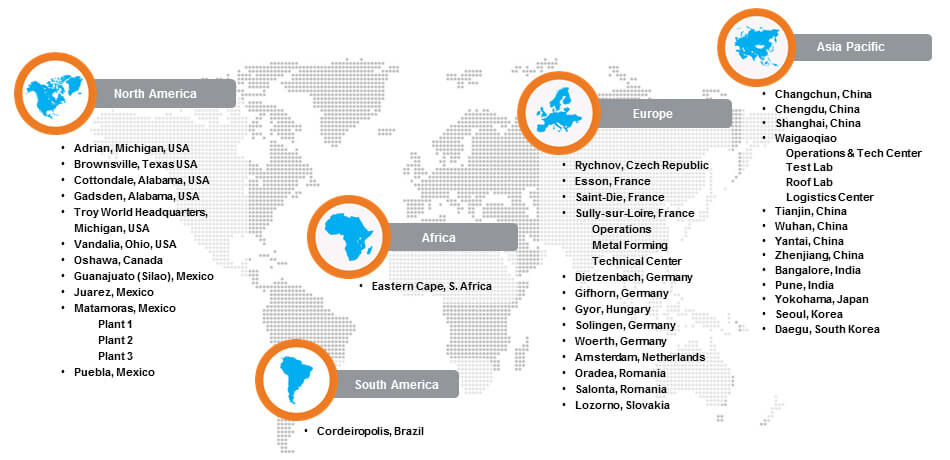
Dates: 9-11 July
Location: Salonta, Romania
Language: English
Who should attend?
Leaders who wants to understand how to go beyond tools and create effective management systems in order to increase performance and creating a sustainable lean culture.
Why to participate:
-
Learn how to set up the framework for daily management system to engage every level of management and team members towards driving business results
-
Learn by doing: Alignment of the organization’s goals and activities both vertically and horizontally to drive the desire behaviors.
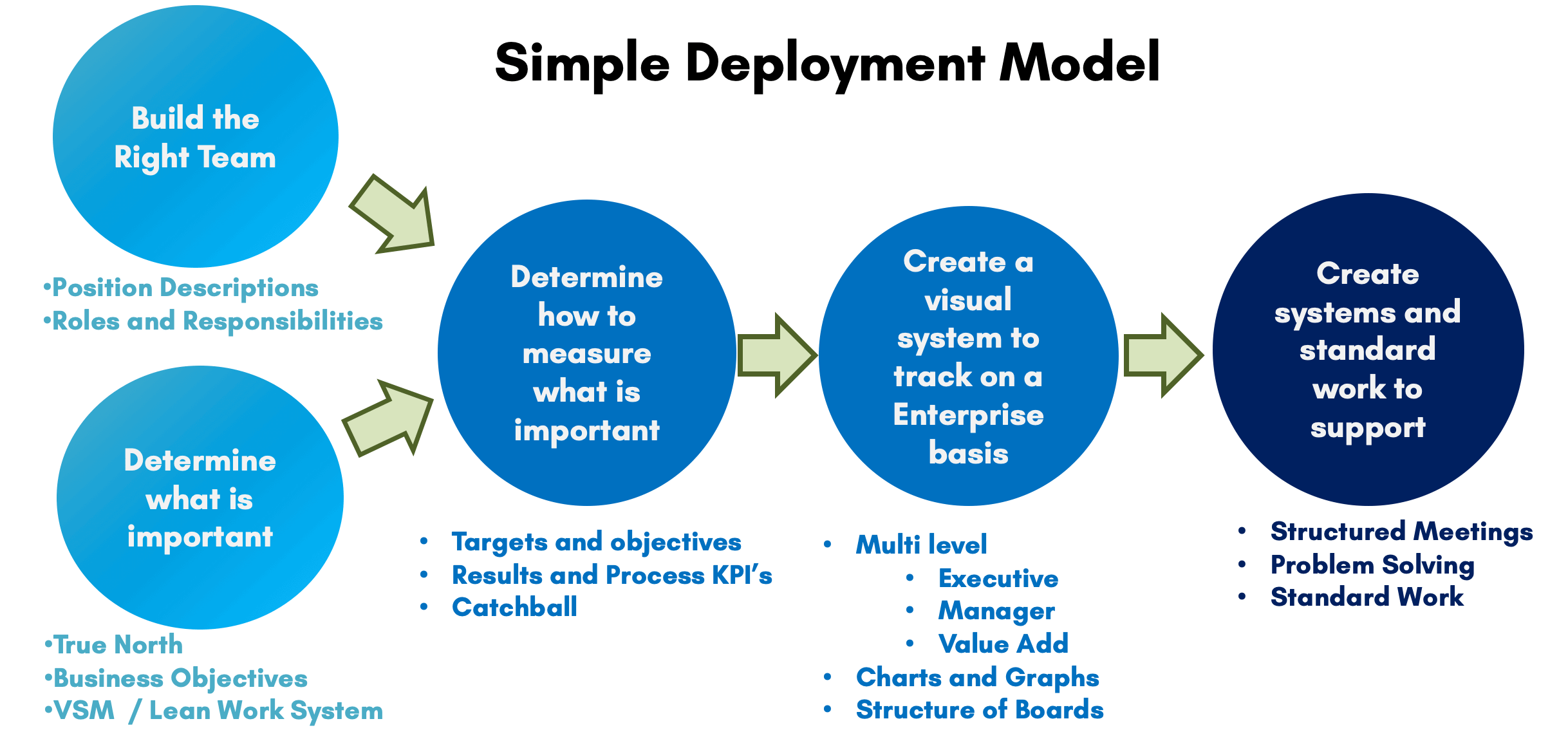
Training Agenda:
- Confirm True North – Cascade
- Group Exercise: Everyone on the same page for True North
- Why – Mission , Purpose
- How – Values and Operating System
- What – Vision and True North Goals
- Philosophy and Beliefs
- Roles and Responsibilities for each Level
- Servant Leadership in action
- Job Security Philosophy
- Roles and Responsibilities for each Level
- ID “Current State” of Lean Culture and ID Gaps in relation to
- foundations of DMDS:
- 5-S, Standardization, Training Method, Visualization
- Value Stream Organization and Management Structure
- Exercise – each team report out “Current Situation” of their Lean Work Systems
- Gemba Exercise to ID “Current State” of Lean Culture and ID Gaps in relation to foundations of DMDS (5-S, Standardization, Training Method, Visualization, Value Stream Organization & PDCA). Large group will break into sub groups for each corresponding KPI Pillar
- Check Action – each team report out “Current Situation
-
- Key Performance Indicators
- Enterprise – Business and Financial
- Vertical Cascade – Tiered approach “Pillar” KPI’s
- Horizontal – Functional Support Indicators
- Main, Sub and Process KPI’s
- Key Performance Indicators
-
- Group Exercise: Recommend KPI Structure for all three levels of the organization. Include all pillars of Safety, Quality, Service/Delivery, Cost and People (other)
- Recommend Enterprise Wide KPI (and/or Main KPI)
- Recommend Vertical Cascade KPI’s – Main – Sub and Process
- Executive
- Manager
- Value Added Level
- Group Exercise: Recommend KPI Structure for all three levels of the organization. Include all pillars of Safety, Quality, Service/Delivery, Cost and People (other)
-
- Systematic Problem Solving at all level
- Executive to Value Added Member
- Boulders, Rocks and Pebbles
- Lean Leader Standardized Work
- Systematic Problem Solving at all level
-
-
- Group Exercise – Develop Role and Responsibility and “Leader Standardized Work” for each Level of Leadership
-
-
-
- Daily Huddle Standardized Work Enterprise – Business and Financial
-
-
- Idea Implementation and Escalation & Problem Solving Teams
- Strategic, System and Daily (Boulder, Rock and Pebble)
- Check status of these three levels “at the gemba” for all levels and all pillars
- Group Report Out – Three Level Problem Solving
-
- Group Exercise – Develop Role and Responsibility and “Leader Standardized Work” for each Level of Leadership
- Daily Huddle Standardized Work
Wrap up, debrief and next steps action plan