Gemba Leadership
Gemba Leadership
Online Live Training with Virtual Tour
If value is created on the shopfloor, why leaders should be somewhere else?
Ritsuo Shingo
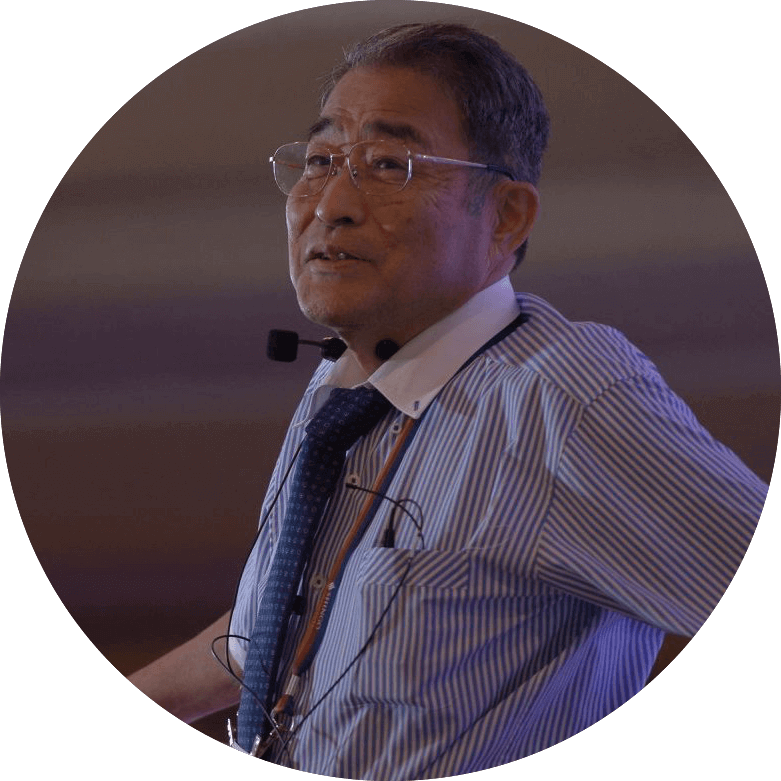
Former President of Toyota & Hino Motors China
-
His father, Dr. Shigeo Shingo, distinguished himself as one of the world’s leading experts in improving manufacturing processes and he has been described as an “engineering genius” who helped create and write about many aspects of the revolutionary manufacturing practices which comprise the renowned Toyota Production System.
-
Ritsuo Shingo helped in the start-up of five Toyota manufacturing plants outside Japan.
-
He worked also at Toyota Motor UK (Derby) and then returned to the China Dept. in Japan.
-
In 1998, had newly established the Toyota first Joint Venture in China, “Sichuan Toyota Motor” and became the first president of the Joint Venture. He established the Joint Venture between Hino Motors and Guang-Qi Motors and became the president
-
In 2012 He left Toyota and started to help leaders around the world, sharing his experience.
Mihai Cristea
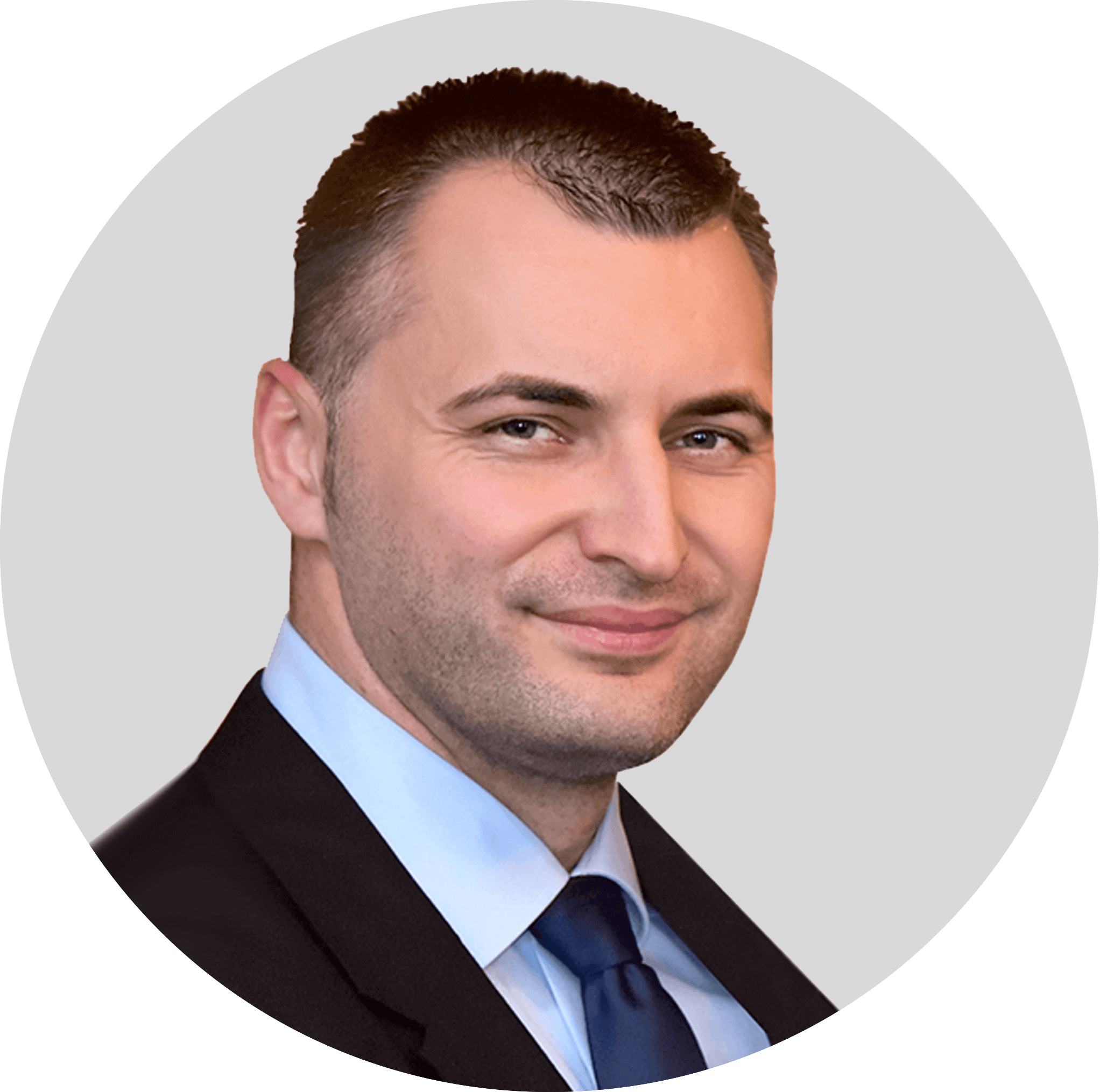
Automotive Plant Manager
-
Mihai is an Automotive plant manager, and over the last 6 years, he started and guide his team in a journey towards excellence, based on the lean principles, spreading the mentality and culture of Gemba leadership with his team, always looking to get further and better.
-
He managed to turn around performance and keep growing the safety, quality, delivery, cost indicators.
-
He has achieved these results by developing work systems such as problem-solving, daily management, Gemba walks, visual management, and technology to support faster response.
-
He is a leader who leads by example, paying attention to people’s development and quick reaction to improve overall performance.
This program aims to transmit and discuss key points to enhance the way leaders act and engage their teams to work on continuous improvement.
Dates: 23,24, 25, 30, 31 March 2021
5 sessions, each one of 2 hours
Location: Online Live via Zoom
Time:
EET (Bucharest) 1:00 PM – 3:00 PM
CET (Madrid, Budapest) 12:00 PM to 2:00 PM
Language: English
Who should attend?
Leaders who wants to understand how to go beyond tools and create effective management systems in order to increase performance and creating a sustainable lean culture.
Why to participate:
-
Learn how to frame a daily management system to engage every level of management and team members towards driving business results.
TRAINING AGENDA
Go and Observe (Gembaism)
4S, Visual Management and Standard Work
Virtual Tour on the Shopfloor (Visual Management)
PDCA
Source Control
Virtual Tour ( Problem Solving Activities and Employee Involvement)
How to create Quick Response
Stop at the first defect
Line Response 5W2H
Problem Solving Activity
What to do on Gemba Walks
Culture = Behaviors
Key behaviors Indicators and Key Performance Indicators
Toyota Experience Opening Plants
Leadership
Improvement possibility in companies I have consulted/visited
Join us, Register Now!
- Individual PackageUntil March 8€750/ ParticipantReduced from 900€
-
Personal Access to online Live Training
- Virtual Gemba Tour
- Access to live workshop with the trainer and other participants
- Digital training material
- Alfra Consulting training recognition
-
Our participants review

For me, it was the first course conducted 100% online, but the way it was structured and approached did not affect the quality of the course.
Congratulations to the entire Alfra team! Good job!

Thank you, in my personal name, first of all! It was very interesting for me. I admit that I am fascinated by the LEAN system and I have a curiosity and a desire to deepen my knowledge in the field.
And, implicitly, on behalf of the company. It is a very useful source of information for my colleagues.

I think that this course made an important contribution through trainers, content, and structure, also the practical examples completed the theoretical part and inspired me in what I want to implement in the company as a philosophy and good practices. The way that the scientific part was explained helped me and then the practical part through skills up to the level of attention to behaviors also. The live sessions, especially in which Mr. Cristea was invited, reinforced the message that the implementation of lean management is possible.