Why do we need Quality Improvement culture?
Building an organizational culture of Quality Improvement is an absolute necessity for any organization, both to withstand difficult conditions and to perform in a challenging economic environment.
Usually, the company’s efforts and resources are spent to deal with unexpected daily issues and to concentrate the people’s energy in a never-ending „fire fighting” approach.
By developing a quality improvement mindset plus a collection of specific tools and skills associated with it, inside all different compartments and across the organization, will bring great benefits in the medium term:
- Increase customer satisfaction and trust in your brand.
- Create savings and cost avoidance with a direct impact on product/ service conversion cost performance.
- Reduce the burden and pressure on members and leadership, increasing their motivation and satisfaction.
- Release leadership and team members to focus more on new projects and future development, rather than on-time consuming and low or no-value activities.
The quality performance of the organization is impacted by a number of practices that must be developed and supported daily under the sponsorship of management. And, consequently, the successful implementation of these practices will influence the efficiency with which a company is able to achieve its objectives.
Finally, it means that the organization controls its processes and is produced with minimal wastes.
One of the best solutions to the quality problems and their effects on the organization and its stakeholders can be offered by Built-in Quality.
What is the Built-in Quality (BIQ) process?
BIQ was developed by Toyota and is part of Toyota Production System (TPS) pillars, with several characteristics:
- BIQ is one of the first steps in Lean deployment.
- The BIQ foundation is to develop the employee’s mindset for quality, by preventing and stopping the flow of defects.
- When a new product goes into serial production it already has a level of quality inside its DNA that has been “designed” and established.
- With BIQ, each person involved in operational and support processes must ensure they never accept, create and knowingly release a defect, or, as it is also known as the 3 Don’t concept: Don’t Accept/ Don’t Produce/ Don’t Release defects.
- An important difference compared to the other quality approaches is the stop function, so the reaction flow when an incident occurs is: Stop, Sort, then Fix.
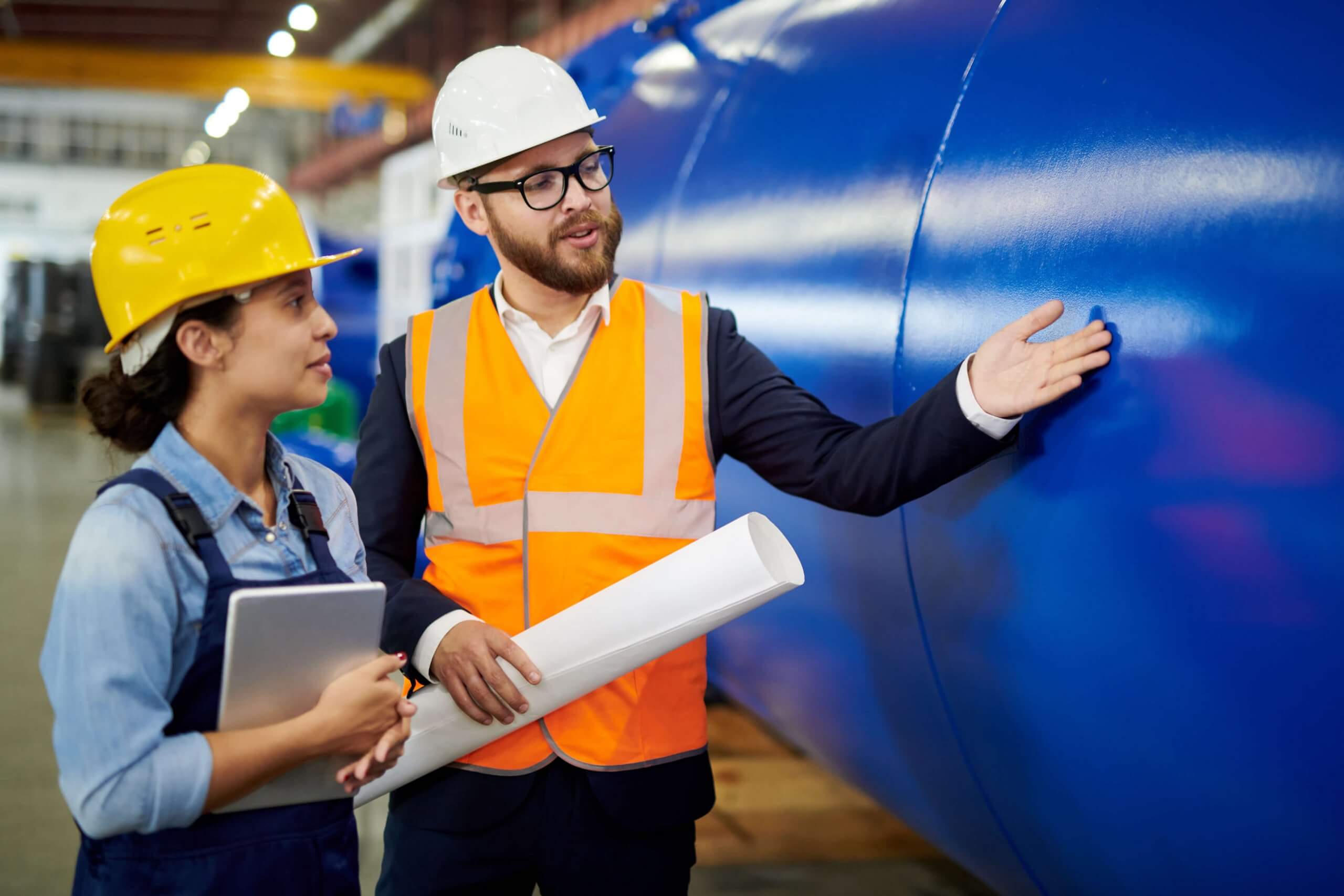
What is a Built-in Quality vision?
- Improve Customer satisfaction by promoting 0 defects, aligning the process to this expectation.
- Strengthen Quality Behaviors leveraging don’t accept, don’t make, and don’t release defects and stop the machine, record, fix the issue, and restart.
- Reduce No-Value Added activities and Cost of Poor Quality.
- Continually improve the product’s design and develop & maintain capable processes.
- Integrate Statistical Process Control (SPC) and Poka-Yoke with the objective of removing the 100% inspection.
- Include in Standard Work reviews the data collected with Measurement Systems Analysis (MSA) and SPC, to improve products and processes.
- Optimize existing inspections in the incoming area and shop floor by improving supplier quality.
- Improve Problem Solving effectiveness and closed-loop to standard processes and product designs.
What are a few of the Key Elements of Built-in Quality?
Listed below are some basic elements of BIQ but the concept is not limited to them:
- Protect the Customer using Problem Solving.
- Prevent quality issues & escapes through Poka-Yoke, Failure Mode and Effects Analysis (FMEA), for both Serial Production and New Part Introduction.
- Andon and Escalation Process.
- Visual Management & Process Change Log.
- Autonomation (automation with a human touch).
- Layered Audit Process.
- Data-Driven Process Control and 6 Sigma tools for analysis, collection, and retrieval of actionable data.
- Leadership Practices and Coaching.
- 5S process.
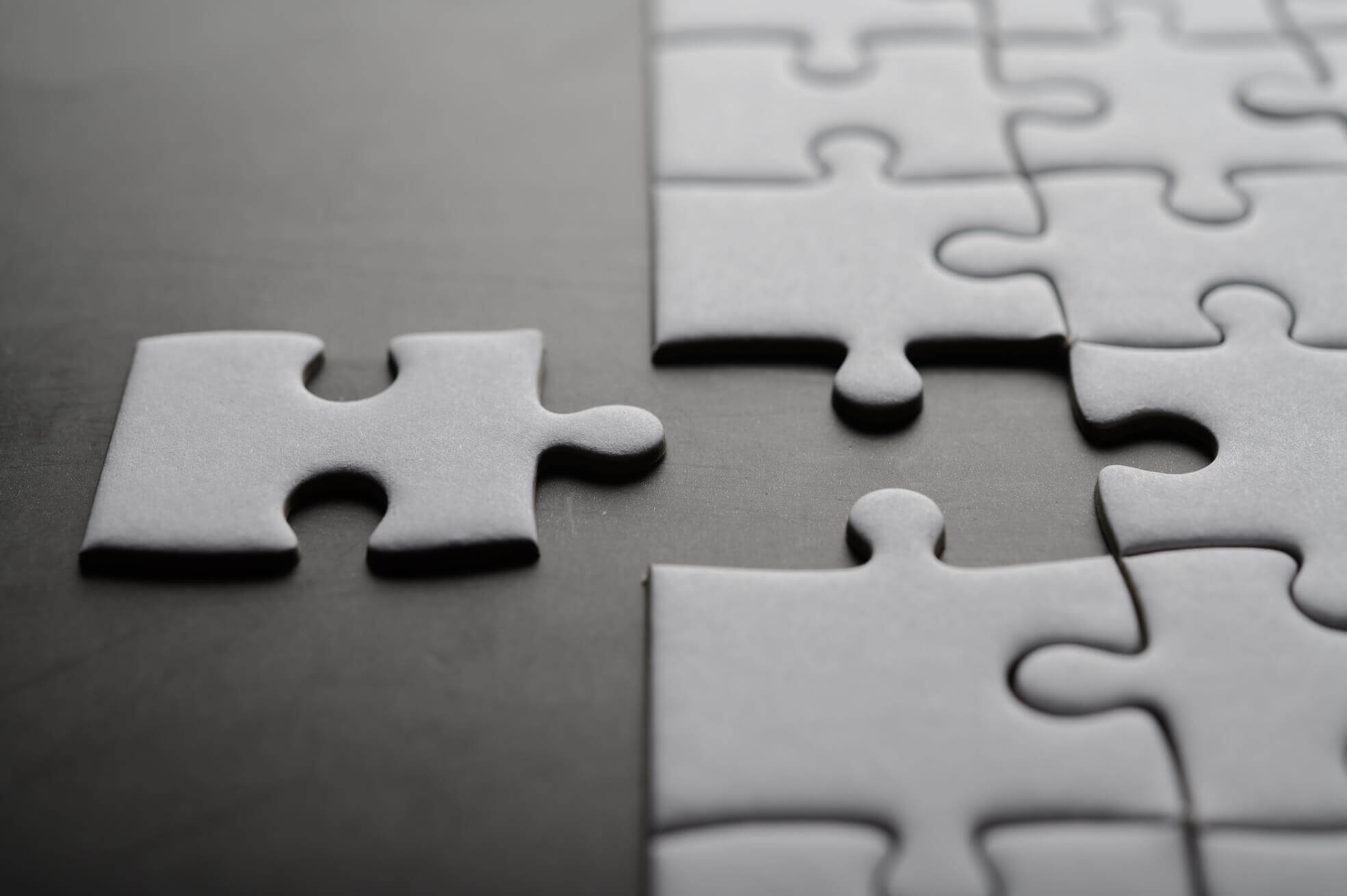
Conclusion
All of these are Lean tools and their systemic application with scientific thinking can produce those changes that lead to excellence in quality.