A Reverse FMEA (RFMEA) is a powerful tool used to validate the assumptions made during a traditional Failure Mode and Effects Analysis (FMEA). It’s essentially a “go-see” approach, where you physically visit the process or production line to observe it in action.
Why Use a Reverse FMEA?
- Identify Gaps: It helps pinpoint any missing failure modes or controls that may not have been considered during the initial FMEA.
- Validate Assumptions: It ensures that the assumptions made in the FMEA are accurate and relevant to the real-world process.
- Improve Control Effectiveness: It assesses the effectiveness of existing controls and identifies opportunities for improvement.
- Enhance Problem-Solving: It encourages a proactive approach to problem-solving by focusing on potential failures and their root causes.
How to Conduct a Reverse FMEA
- Review the FMEA: Begin by thoroughly reviewing the existing FMEA for the process.
- Visit the Process: Go to the actual location where the process is being carried out.
- Observe the Process: Watch the process in action, paying close attention to each step.
- Identify Potential Failures: Look for any potential failures or deviations from the standard process.
- Assess Control Effectiveness: Evaluate the effectiveness of the controls in place to prevent or detect failures.
- Document Findings: Record any discrepancies or additional risks identified during the observation.
- Update the FMEA: Incorporate the findings from the RFMEA into the original FMEA, updating the risk assessments and control plans as needed.
Key Benefits of Reverse FMEA
- Improved Product Quality: By identifying and addressing potential failures, you can significantly improve product quality.
- Reduced Costs: Early identification of potential problems can help prevent costly defects and rework.
- Enhanced Customer Satisfaction: By delivering higher-quality products, you can increase customer satisfaction and loyalty.
- Continuous Improvement: The RFMEA promotes a culture of continuous improvement by encouraging a proactive approach to problem-solving.
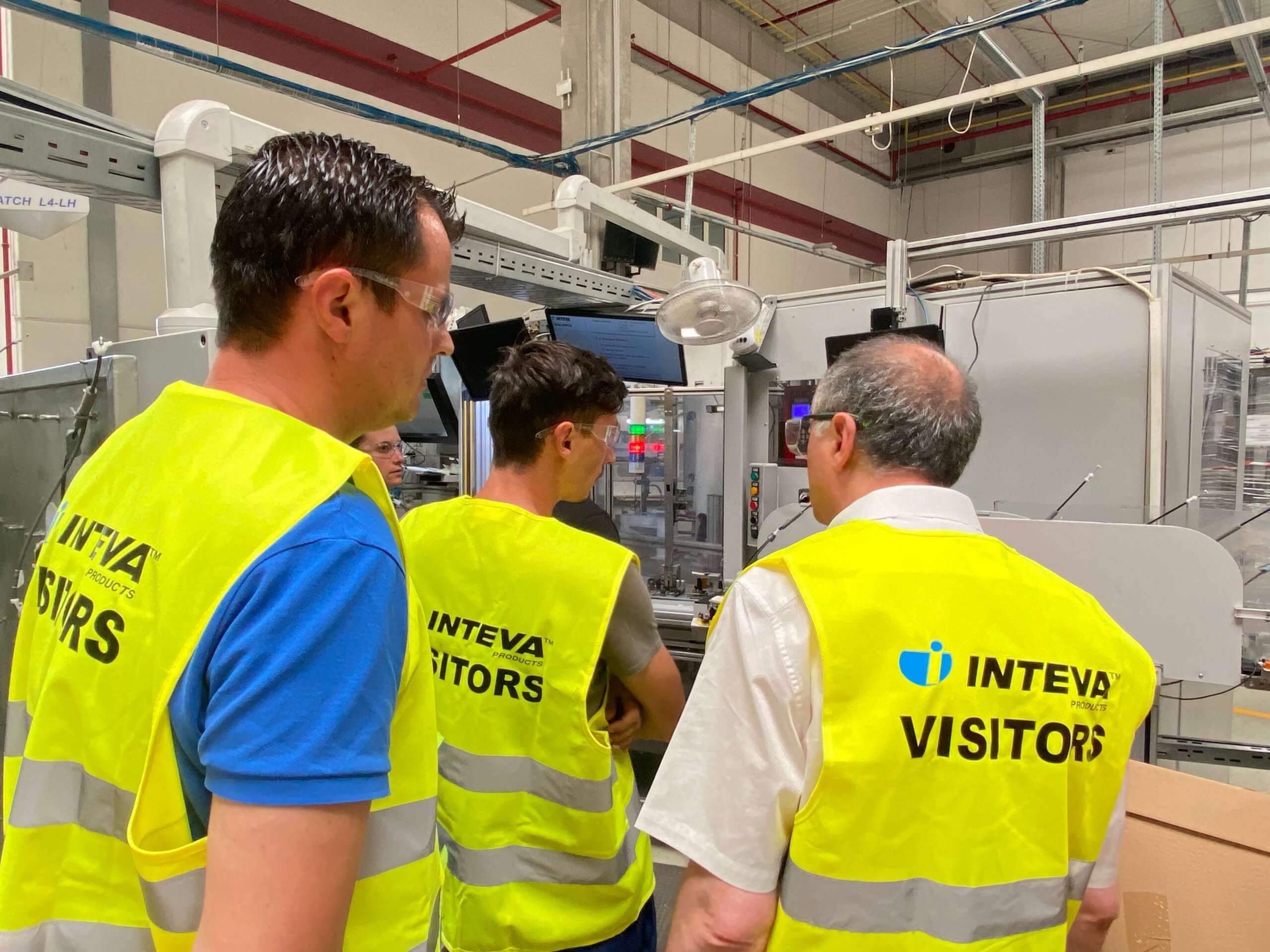
Conclusion
By conducting regular Reverse FMEAs, organizations can ensure that their FMEAs remain accurate and effective, leading to improved product quality, reduced costs, and increased customer satisfaction.
Reverse FMEA, FMEA Verification, Process Observation, Failure Mode and Effects Analysis (FMEA), Problem-Solving, Continuous Improvement, Quality Assurance, Risk Reduction,