Total Productive Maintenance (TPM)
Increase availability by eliminating and preventing losses
In the journey to operational excellence, many companies realize that low availability is a major barrier.
The key to successful manufacturing is when the machines perform as specified in their design. The basis for a successful Lean production system is Total Productive Maintenance (TPM).
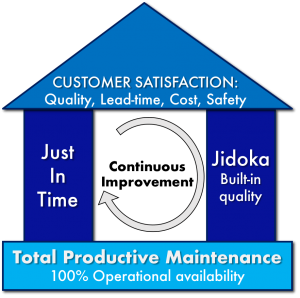
TPS House
What is TPM?
TPM is a Maintenance Management system that seeks to eliminate and prevent operational losses.
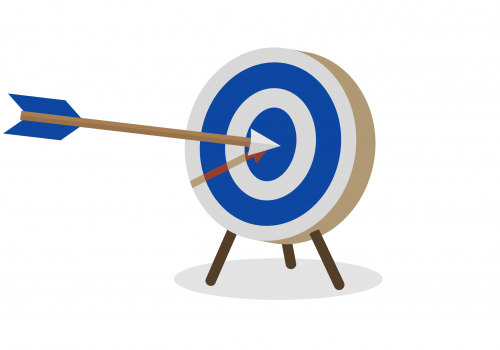
Endless challenge of 100% operational availability
To maximize the efficiency of the machines, everyone participates in: Planning, Use, Maintenance and Improvement of the Machines.
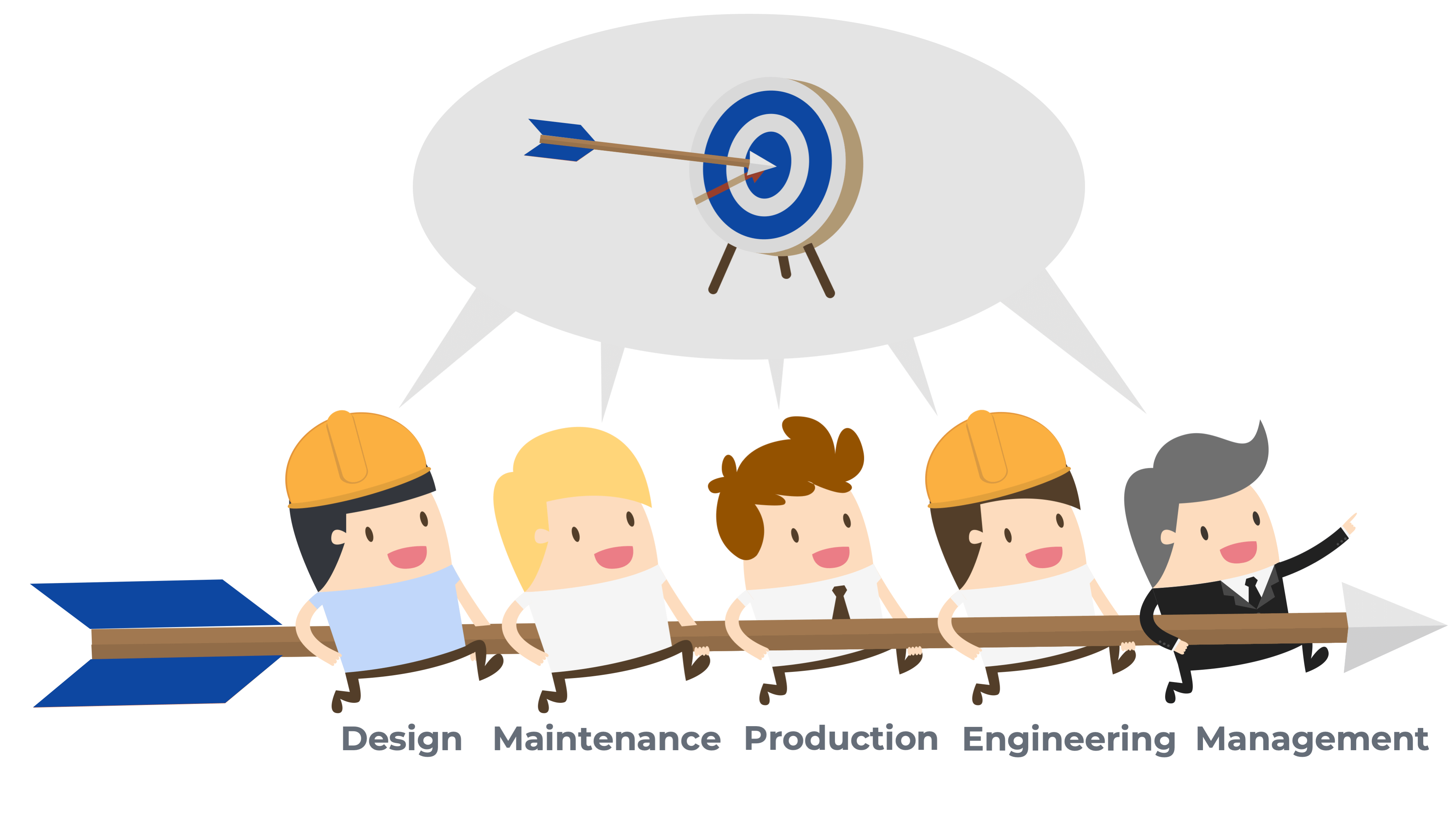
Involving the whole team in TPM
The 4 elements of the TPM Model are:
1) Designing a Good Equipment
Thinking of a simple, easy to use machine and maintaining a machine that is designed to not have downtime, using knowledge of the process and working conditions.
2) Downtime Prevention
Preparing the operational team for the use of the machine, defining the activities that will prevent downtime, such as autonomous maintenance, planned maintenance and predictive maintenance.
3) Fast and efficient solving of Downtime
Accurate and fast correction of the problem, follow-up of the cause and optimal prevention of the recurrent problem.
4) Improving maintenance methods (Kaizen)
Improving performance and working mechanisms/systems.
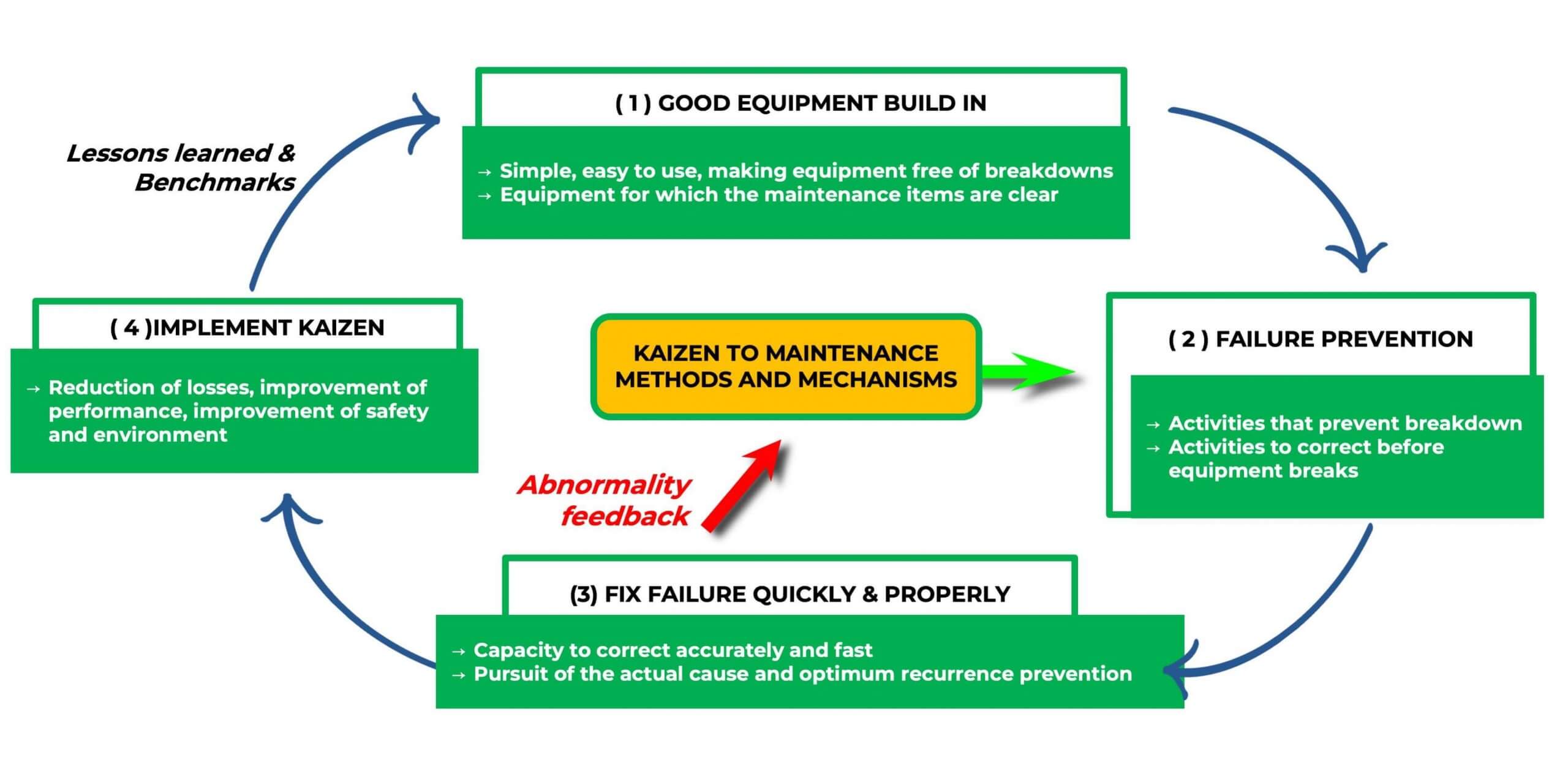
The 4 Elements of the TPM Model
An important concept in total productive maintenance is the involvement of all people in the use and care of the equipment, from team members to company management.
One of the first steps is to bring a machine to ideal conditions, major repairs and replacement of parts may be necessary for less well-kept machines, in order to have the operating conditions as a new machine.
The goal is to have a machine in ideal condition (standard) where the abnormalities are easy to identify, which can be easily identified by the people who operate the machines.
This leads us to the next concept, Autonomous Maintenance.
The purpose of autonomous maintenance is to develop a close relationship between production and maintenance departments where information is effectively shared in time to prevent downtime.
The activities led by the production team are:
- Assessment of possible abnormalities
- Cleaning and lubrication
- Replacement of small parts and consumables
- Minor adjustment and repairs
For these it is critical to develop a production team that knows the important elements of the machine, which must be formed by the engineering and maintenance team to know and use the machine properly.
Other very important elements for increasing operational availability is a quick reaction to damage, even when we have planned and defined prevention activities, we will have downtime situations and then we need a process of communication, diagnosis and repair of damage, without wasting time at each stage of the process.
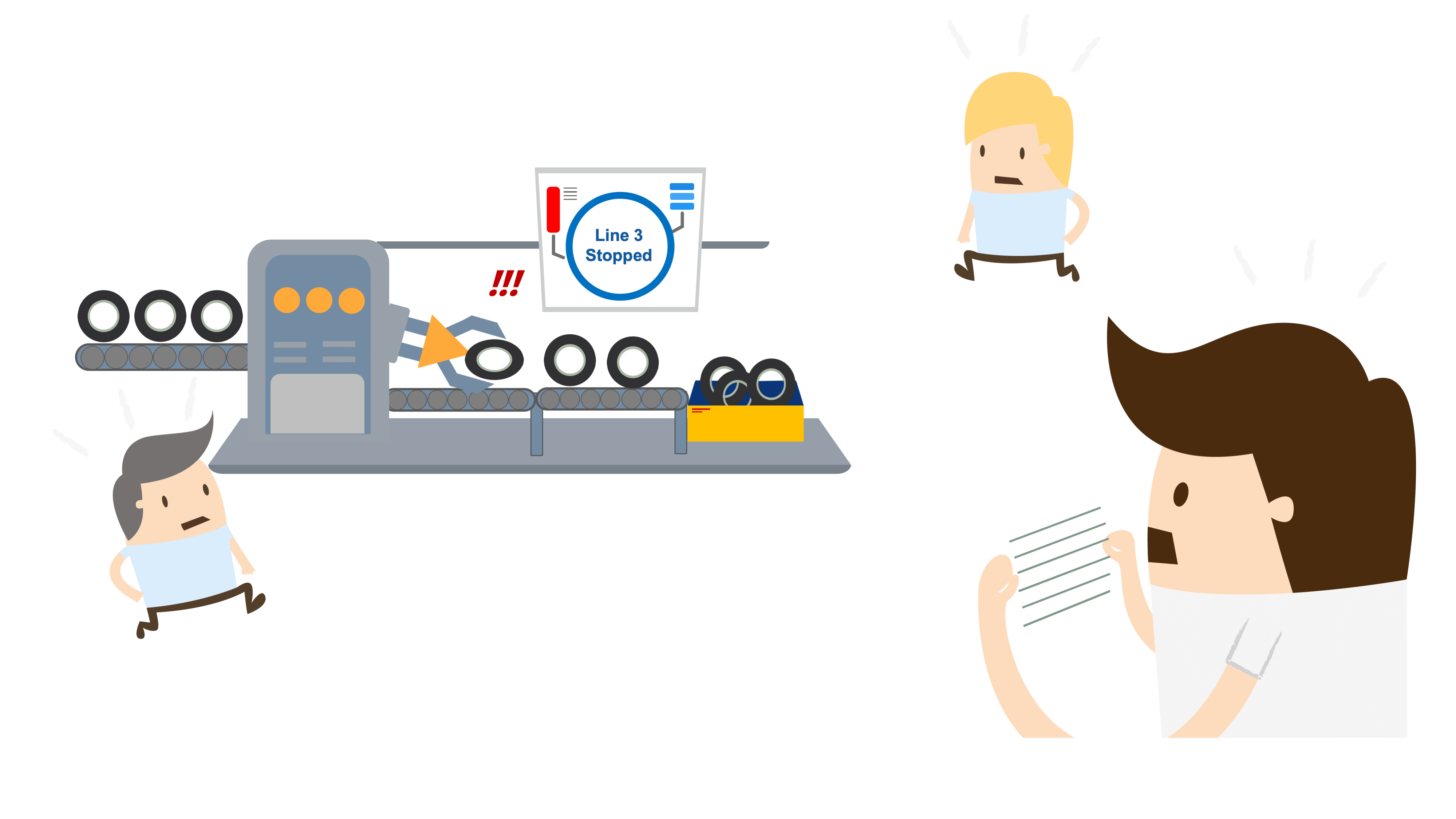