Hoshin Kanri – Strategy Deployment Process
Get everyone in the same direction, and focus on the “vital few” major problems in the organization.
Most organization’s struggle with “getting everyone on the same page” to work towards the right direction. This is what the Hoshin Kanri process is designed to do.
Hoshin is a process that leverages the power of the entire organization, not just a few leaders. It gets everyone in the organization on the same page and the process of catch ball that goes both vertically and horizontally through the organization.
The resulting alignment gets everyone going in the same direction, focusing on the “vital few” major problems in the organization.
The process then taps into the creativity of teams to address these problems by focusing not only on results but on the “process”, which will not only help to achieve the results, but allow the organization to standardize, sustain and share them.
Training length: 16 hours (2 days)
Investment: 790 Euro/ person
Who Should Attend:
CEO, President, Vice-Presidents, Executive Leaders, General Managers, Lean Leaders, and any one facilitating change within your organization who understand the importance of going beyond tools to creating effective management systems and processes in order to set the basis for creating a sustainable lean culture.
Read more about Hoshin Kanri:
Centrul de afaceri Maris
Strada Voinicilor, Arad 317405, Romania
Agenda:
- Assessment – Determine “Current State – Future State & Gaps to Address”
- “Purpose of Plan” and Power of Why – True North – Values, Vision, Mission, Roles and Responsibilities of each level
- Top issues and needs for – Customer (Customer Satisfaction Survey), Market, Business, Competition etc.
- What Strategic Objectives to we need to achieve in the next 5 years?
- Key Performance Indicators Trends
- Current state of these metrics & ID gaps (both type and value)
- Internal assessment (State of Lean, Employee Issues, etc.)
- Beyond SWOT to Innovation Strategies
- Servant Leadership
- A new role for the “Next Generation Lean Leader”
- Process KPI’s
- Leader Standardized Work
- Lean Leadership “On the Job Development Model”
- PDCA – Discipline and Accountability
- Role of HR in Partnering with Leadership for Driving Innovative Change
- Engaged Workforce – Idea Generation
- Coaching – Problem Solving
- Reflection Process
- Create Plan and Schedule for “Key Lean Element” Implementation Strategies
- Assign members and “lead” for each Strategy
- Plan “Catch-ball” activity to “flush out” and cascade plan
Instructor
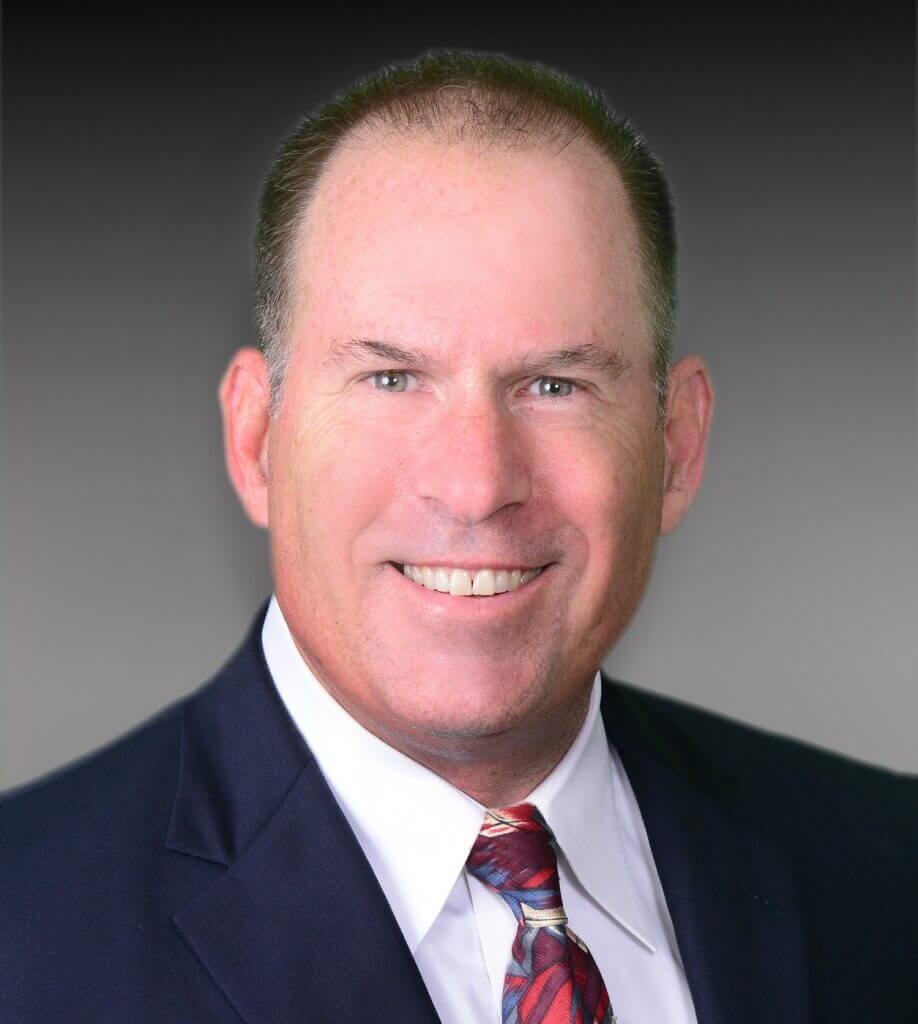
Jeff Strabala
Strategy & Operations Management Expert
Jeff worked for Toyota for over 21 years; his extensive experience is based in Operations Management in Toyota North America as Manager and internal consultant.
Jeff was member of the Leadership team for the launch of two “Greenfield” automotive plants and subsequent plant capacity expansions valued in $4.2 billion USD. During his tenure at Toyota, Jeff also spent 3 years of “internal consulting” with improvement projects at Toyota and Tier 1 suppliers plants adding value related to safety, visual and floor management, strategic planning, people development and financial controls.
Project General Manager (Consultant) – Toyota OMDD
- Internal consulting position, Investigation, Analysis, and Improvement of floor operations applying core Toyota Production Systems tools.
Vice President – FIC America Corp
- Led Supply Chain, Conveyance Operations, Project Planning, Production Control, Human Resources, IT, Accounting and General Affairs/Purchasing teams for 2-plant manufacturing operation in Automotive Tier 1 supply.
- Systems and Processes put in place reduced plant Overtime 25%, while simultaneously reducing delivery delays & errors 80% saving over $3million annually.
Project General Manager – Toyota North America.
- Improved Safety Systems for Toyota’s MS manufacturing plant through active initiatives to educate plant personnel revise and introduce new programs, establish management accountability through daily reporting and monthly performance meetings, introduced gated safety management process that reduced TIR by 50% within 6 months.
- Developed, Validated comprehensive [all functions] Safety Metrics during 2013 New Generation Corolla launch, resulted in improved safety KPI during launch, Metrics, tracking and reporting adopted in North American Region.
Assistant General Manager-Toyota
- Responsible for Plant Manufacturing Operations, member of Executive Team,
Primary responsibility for Production Control, Supply Chain & Logistics, Project Management for 8 Model changes, Plant Manpower Productivity planning and reporting. - Supported Toyota Production System training and application, and Visual Management (FMDS) roll out at TMMBC, management Mentor.
Manager, Production Control – Toyota (TMMBC & TMMI)
- Production Control Planning & Coordination of Operations for Toyota truck factory with multiple product lines 2000 -2003.
- Additional collateral duties involved management of TMMI Corporate Strategy and Reporting, TPS Training Group, Manpower Planning and Productivity group.
Manager Accounting & Finance, Toyota TMMI
- Started up Accounting & Finance operations for Greenfield Toyota plant in Indiana, responsible for accounting, internal and government compliance, budgeting and cost reduction efforts.
Academy Background:
University of California, Los Angeles – Bachelor of Applied Science (BASc), Systems Engineering
University of Southern California – Marshall School of Business – MBA, Operations and Venture Management.
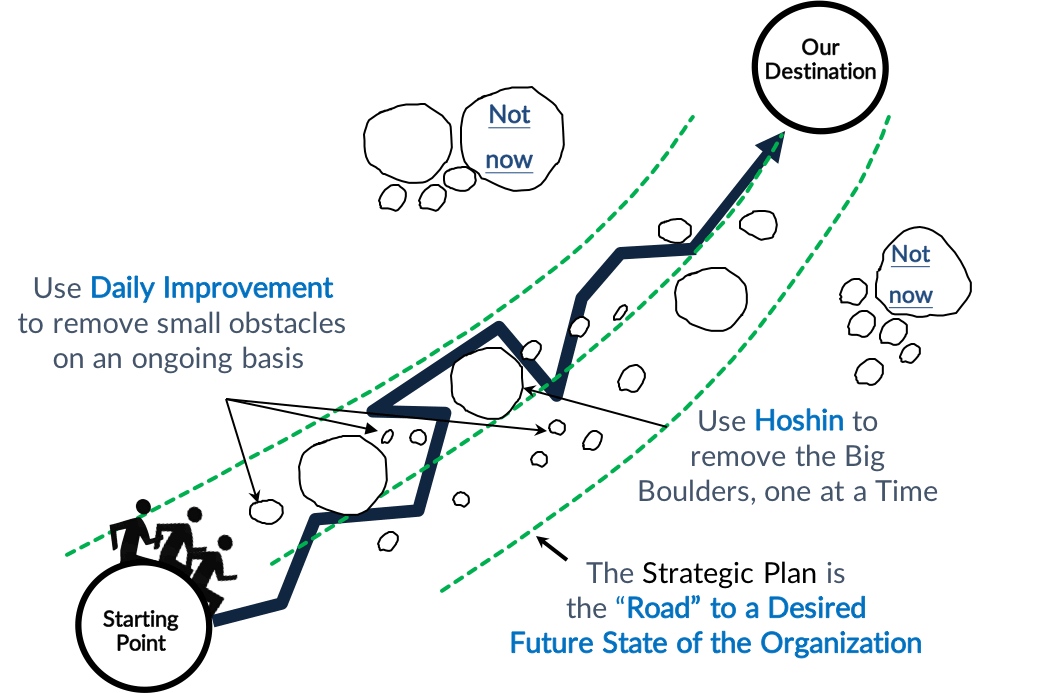