Production Planning & Control Training
Learn the best practices from a Toyota Leader
The key for real Lean Production success
One of the keys to Toyota’s success is the role that Production Planning and Control plays in the organization.
Production Planning and Control is the voice of the Customer to manufacturing and conversely it is the section that manages information flow from the Customer, Suppliers, Manufacturing and Engineering.
As Atsushi Niimi (former President of TMMNA) once said, “PPC is where the real power of Toyota is”.
Main benefits
Participants will understand the Toyota Way in:
How to create a Production Forecast
How to smooth a weekly production schedule.
How to facilitate a Production Forecast Meeting
How to adjust daily production based on Pull System.
Practical Training Instructed by Former Toyota Leader
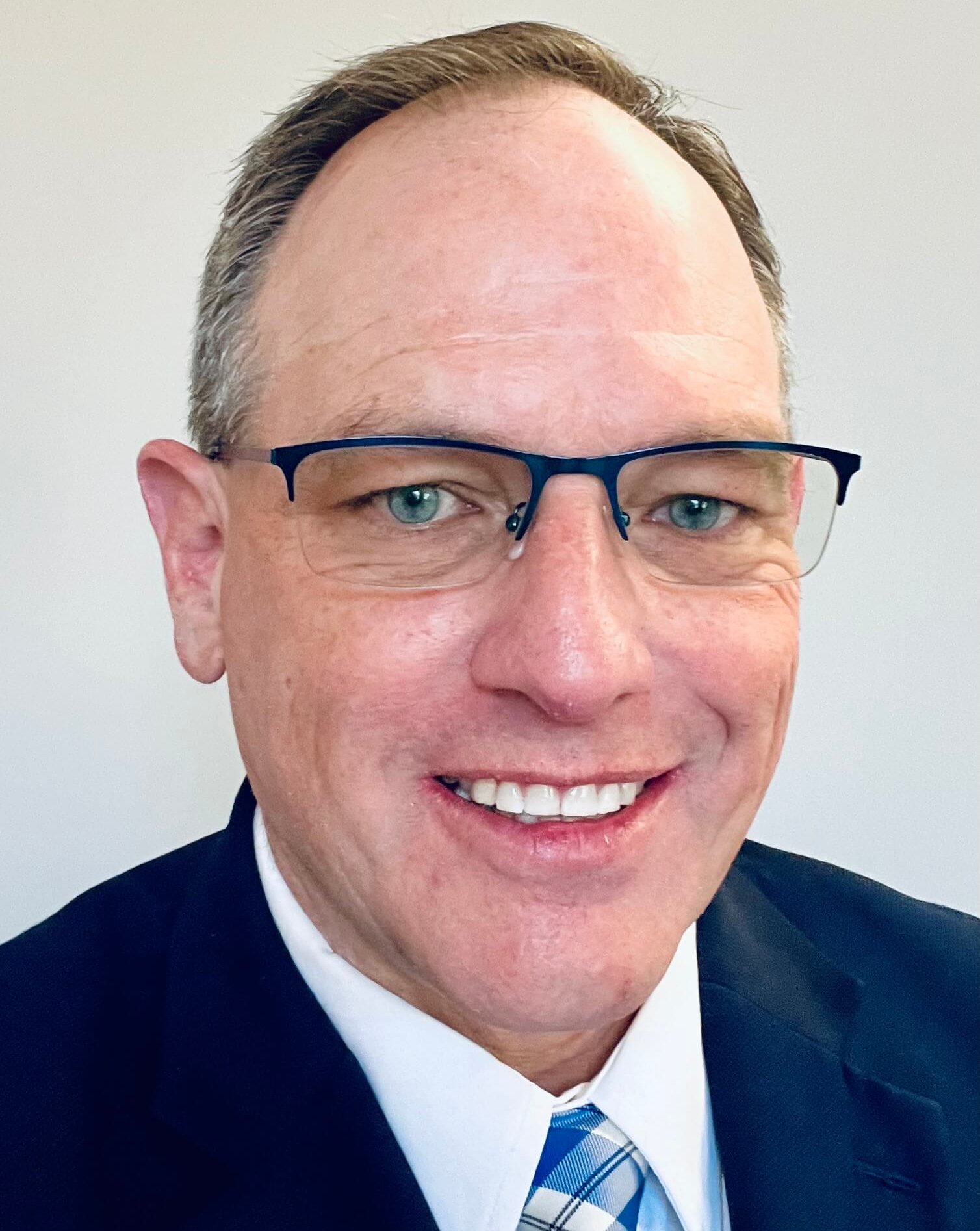
Craig A. Mullenbach
Craig A. Mullenbach
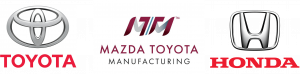
+ 25 years of Experience at Toyota | Lean Management Consultant
+ 25 years of Experience at Toyota | Lean Management Consultant
Craig worked for Toyota Motor Manufacturing for 25 years, after that as consultant for the recent years, He has extensive experience working for top organizations like Honda, Toyota Texas and Indiana and the Joint Venture of Mazda-Toyota, during 4 plant start-ups.
Craig was responsible for starting up the Production Control department at the new Mazda Toyota Manufacturing to support the launch of the new Corolla Cross and Mazda CX-50.
Deep Production Control experience including Ramp Up Planning, Annual and Monthly Volume Planning, New Model Projects, Logistics, Process Improvement, PDCA, Continuous Improvement, and other Toyota lean practices.
Coached and developed the leaders in the group to successfully establish their respective functions. Taught the PC Division professional staff key lean and TPS principles (Process flow creation, JKK, PDCA, Problem Solving, Kaizen, work standardization), and project management principles.
His supplier development experience includes managing team overseeing activity of 23 On-Site Suppliers at the TX truck plant and a 2-year assignment to Toyota Boshoku Indiana to advise and establish new model management processes and standards. Also led readiness activities for near site suppliers introduced at Indiana for launch of a second plant.
External Affairs Manager during which managed community and government engagement through key events, including Tacoma transfer to San Antonio, and Japan earthquake.
Craig has also 6 years working for Honda including New Model Project Managemen
Host Company: Joyson Safety Systems Arad
Joyson Safety Systems is a global leader in mobility safety providing safety-critical components, systems and technology to automotive and non-automotive markets.
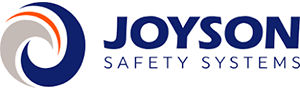
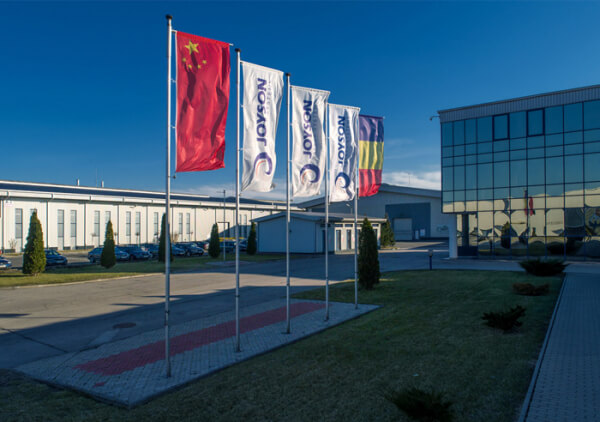
Zona Industrială Arad Vest, Str. III 9, Arad 310491
Training dates:
18,19 & 20 September 2024
Location:
Arad, Romania
Available seats
18 participants
Recommended Industries
Manufacturing Companies: Automotive, Electrical/Electronic, Pharmaceutical, Food & Beverages, Printing, Plastics, among others.
Who should attend?
General Managers, Managers and Supervisors in Supply Chain, Production Planning or Lean Implementation that would like to understand how to maintain a consistent flow of information while supplying the plants with Just in Time product and materials.
Agenda:
- 4 hrs.
- Role of PPC in a Lean Company
- Current Planning vs Production Planning and Control(PPC)
- Creating a Production Planning Group
- Creating a Production Plan (Theory)
- Defining TAKT time
- Creating a Production Forecast
- Creating the Production Plan
- 4 hrs
- Go, See and Understand (Gemba) at planning.
- Gemba Walk Production Line
- Map current State production plan
- Value finished Goods
- Create Production Board(Maintenance Support)
- Create Finished Good Kanban (Staff Support)
- 50% of Team. 6 hours
- Select Target Product Line(cell)
- Create Production 2 month production forecast 1-month firm plan.
- Create Weekly Plan
- Set Min~ Max inventory Targets
- 50% of Team. 6 hours.
- Inventory Finished Goods
- Create Daily production pattern
- Set up Kanban Board Kanbans
- Production Team/Conveyance Training
- Entire Team, Production Manager, Conveyance Manager. 2 hour
- Status check
- Roadblocks and Countermeasure.
- Develop checklists
- 6 hours.
- Assign each member to small group of 2~3.
- Process confirmation.
- List Problems
- Report Out. 2 hours.
- Reports Results
- Report lessons learned
- Create host company homework
In this course we would like to:
- Show the Roles and Responsibility of PPC in a lean organization.
- Create a smoothed weekly Production Plan that will absorb order fluctuation.
- Create a Kanban Replenishment system to drive Just in Time Production while maintaining minimum and maximum inventory levels of finished goods
- Measure the results of our trial.
This workshop will give the participant a chance to create a Production Forecast and Firm Plan, create a weekly plan, and create a Kanban control board to regulate production (replenishment) and confirm production readiness (Man, Method, Machine and Material).
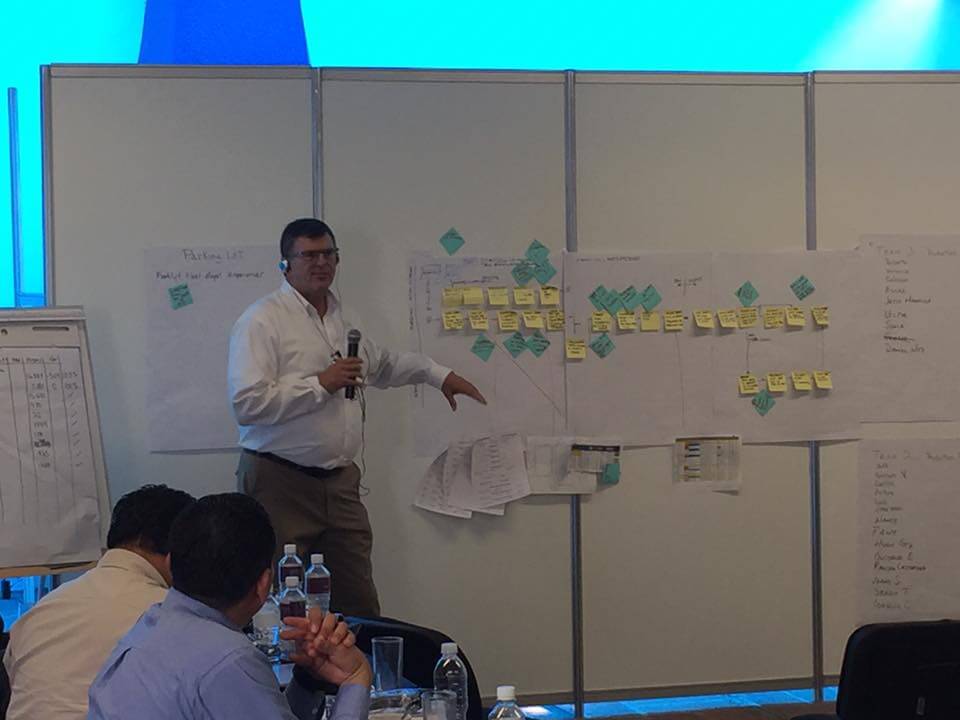
Learn to Map the entire Supply Chain
Identify & Analyze the main opportunities from the supply chain with a real value stream mapping in the host company.

Group Discussion
Share experiences with supply chain professional from different industries and background.
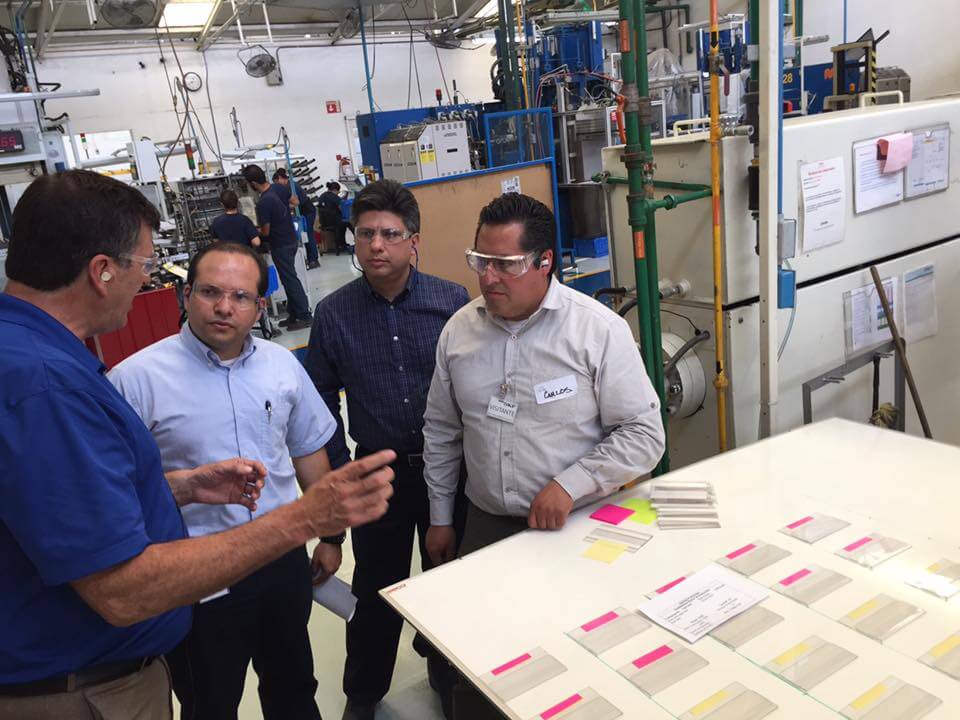
Real Implementation
The training is based in a real project environment to define a production plan and its requirements.