Quick Change Over (SMED)
Quick Change Over (SMED)
In Field Training
Improving set up time in order to Increase flexibility.
Improving set up time in order to Increase flexibility.

Changeover = Time to Change a from the Last Part of a Production Lot to the First Good Part of the next Production Lot.
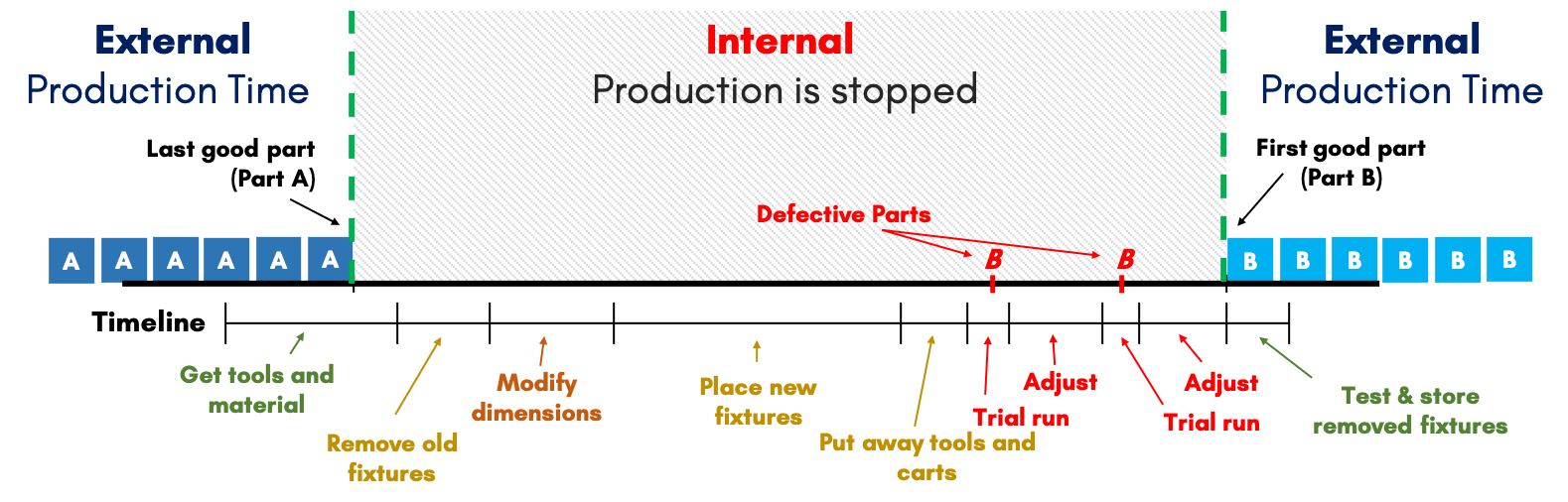
Single Minute Exchange of Die (SMED) is a method developed by Shigeo Shingo and a cornerstone for Just in Time production, it originally looks to reduce the setup time in less than 10 minutes, today this approach is used to improve all kinds of setting activities.
In Field Training: we will learn and practice on the shop floor
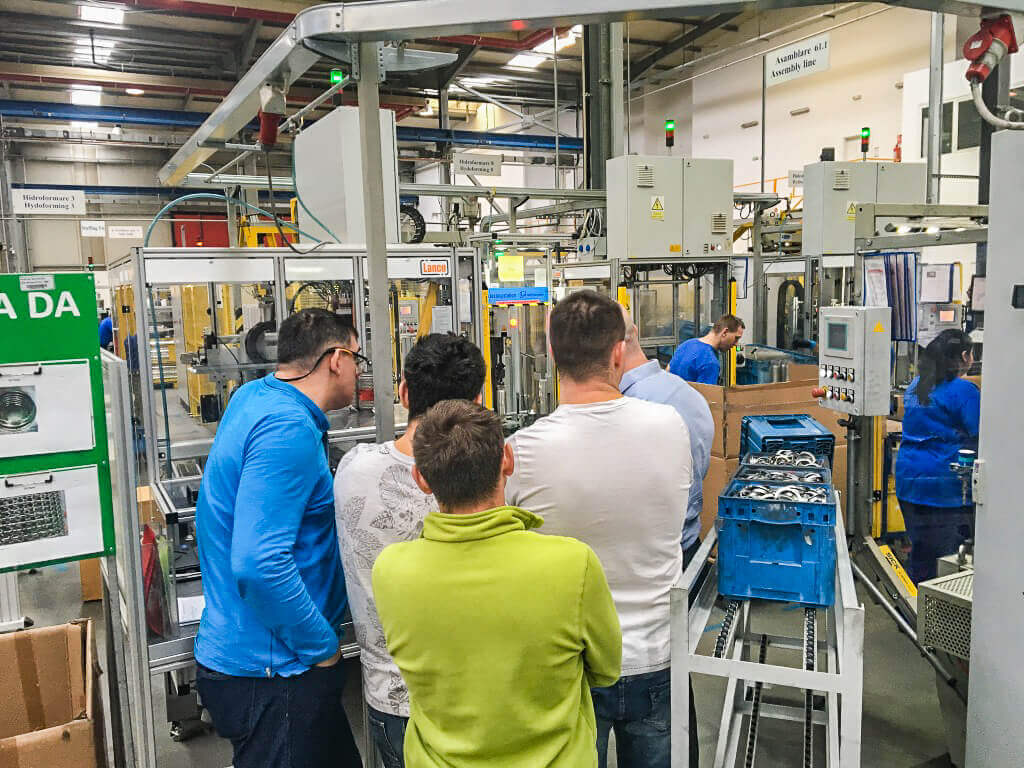
Shopfloor activities
Practice the steps of SMED to reduce time on selected processes.
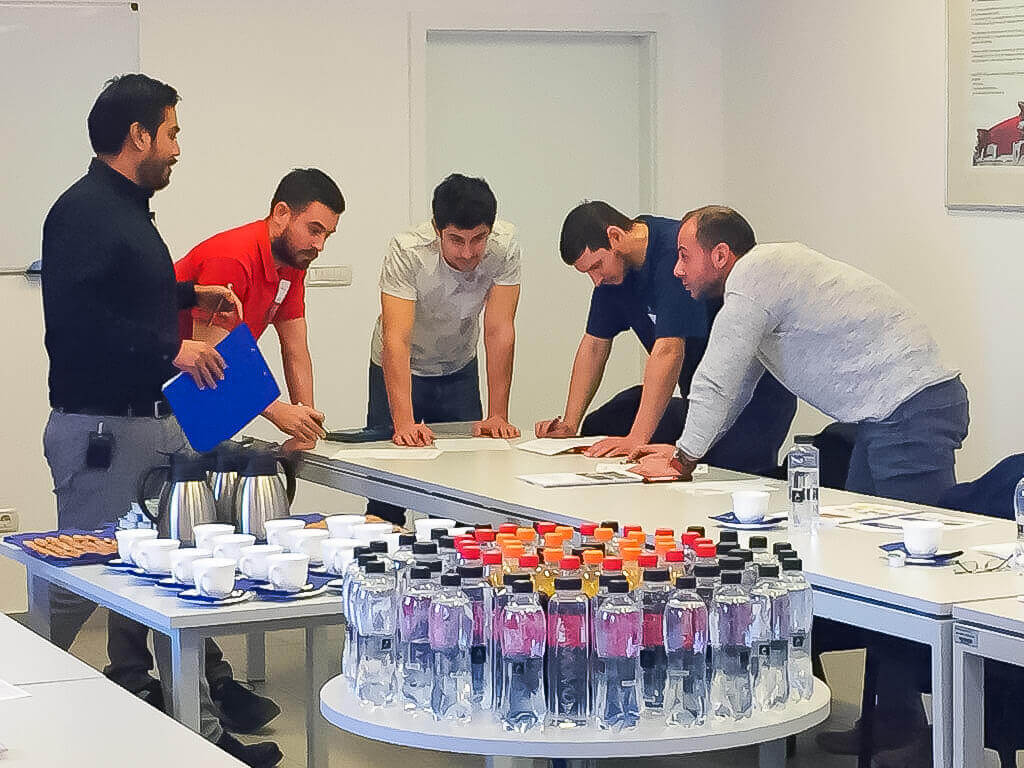
Group Exercises
Learn with participants from other industries and exchange experiences
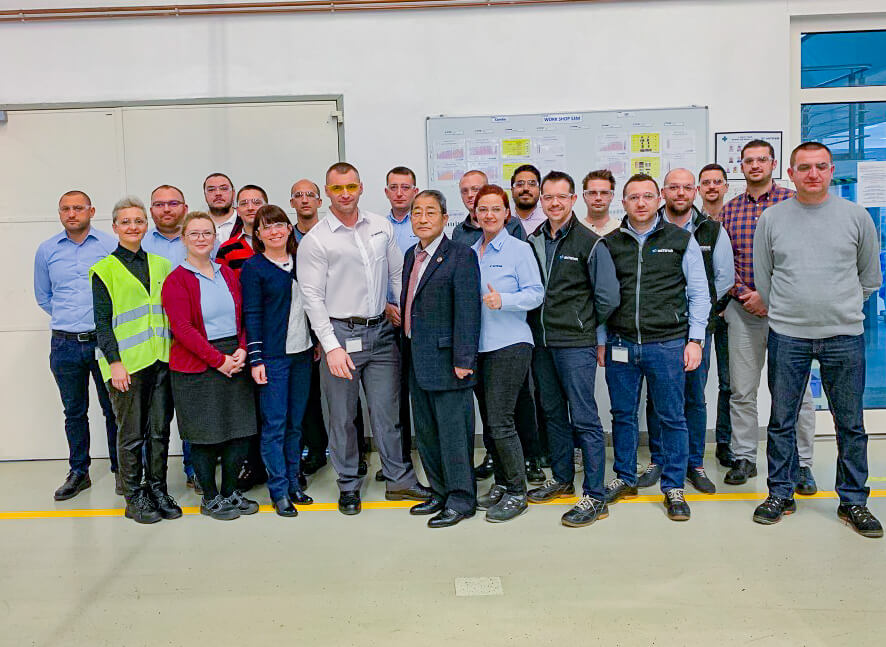
Case examples
Implementation examples and clear exercises to clarify the method.
Objective: understand the concept and practical implementation of SMED in order to set the foundations for Just in Time production and higher equipment availability.
Benefits from SMED:
Quick setups will enable you to:
-
Reduce the work in process and finish good inventory
-
Produce smaller batches of more varied products
-
Reduce your lead time to serve your customers faster
-
Instill the sense of urgency on your team.
Approach: Participants split into teams to perform activities in the shop floor and practice the concepts, working in real processes with a coaching provided throughout the steps.
Skills to be practiced during the workshop:
-The 4 steps method to analyze and improve the Change over process
-How to make easier and streamline any process to reduce the idle time.
-Calculate the savings and impact on reducing the change over time.
Who should attend: Senior managers, leaders and middle managers that are interested on improving the flexiblity on their processes in order to better serve their customers.
Most of the concepts are accompanied by practical exercises or shop floor exercises
-
Lean Management and the need for flexibility
-
SMED background, the cornerstone for Just in Time
-
Calculating the operational benefits from Quick Change over.
-
Flexibility indicator: Every part Every Interval
-
SMED Methodology
-
Activities classification in a Change over
-
Define the set-up Steps
-
Separate Internal from External Activities
-
Prepare all external activities
-
Transform Internal into External Activities
-
Streamline Internal Activities
-
Requirements to enable quick change over
-
Standardization, 5s and Visual Management
-
PDCA approach for reducing the change over time
-
The link to leveled Production and pull system
-
Continuous Improvement
SMED Process
-
1) Document & classify activities
Document a “Dry-Run” Setup, and separate Events into Internal Setup and External Setup
-
2) Transform internal into externals activities
Convert any internal setup events to external setup events using focused, engineered methods.
-
3) Streamline internal events
Standardize activities to simplify, reduce, and Eliminate tasks.
-
4) Eliminating Adjustments and Trial Runs
Turn intuition and guessing into data and settings, 100% elimination of trial runs
Receive the brochure with all details in your email
SMED, Set up, Quick Change over, Zero Change over, one touch Exchange of Die, Single Minute exchange of die, Changeover, Setup Rapid, Quick Setup, Reducerea timpului de reglare