SMED Concept
Single Minute Exchange of Die (SMED) is a method developed by Shigeo Shingo and a cornerstone for Just in Time production, it originally looks to reduce the setup time in less than 10 minutes, today this approach is used to improve all kinds of setting activities.
Improve the Change over process – Learn how to make it easier and streamline any process to reduce idle time and get results by calculating the savings and impact on reducing the change over time.
5S is an important factor of the SMED implementation.
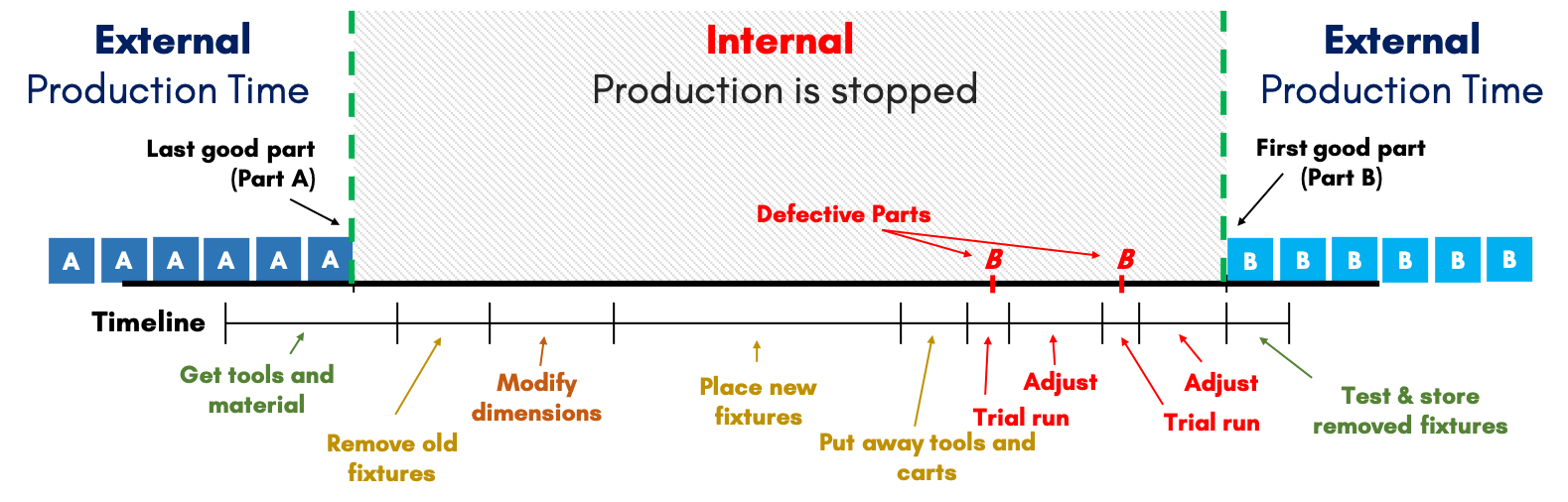
Changeover process
Separating actions by the 4 Steps in the Change Over Process
To see the whole process and optimize it to reduce your changeover time you have to structurize the observed process, each step of the changeover process integrated into one of the 4 SMED steps.
- Preparation – ensuring that all parts and tools are where they should be and that they are functioning properly. Also included in this step is the period after processing when tooling, machinery is cleaned, identified, and tested for functionality prior to storage. Move these items to external and simplify.
- Exchange – Involves the removal of the tooling after the production lot is completed and the placement of the new tooling before the next production lot. Reduce or eliminate these items.
- Setting Conditions – perform all the process control settings prior to the production run. Inclusive of calibrations and measurements (centering, dimensioning, measuring temperature or pressure,) needed to make the machine, tooling operates effectively. Eliminate these actions.
- Trial run & Adjustments – Includes the necessary adjustments (re-calibrations, additional measurements) required after the first trial pieces are produced. The greater the accuracy of the measurements and calibrations in the settings step, the easier these adjustments will be. Eliminate these actions.
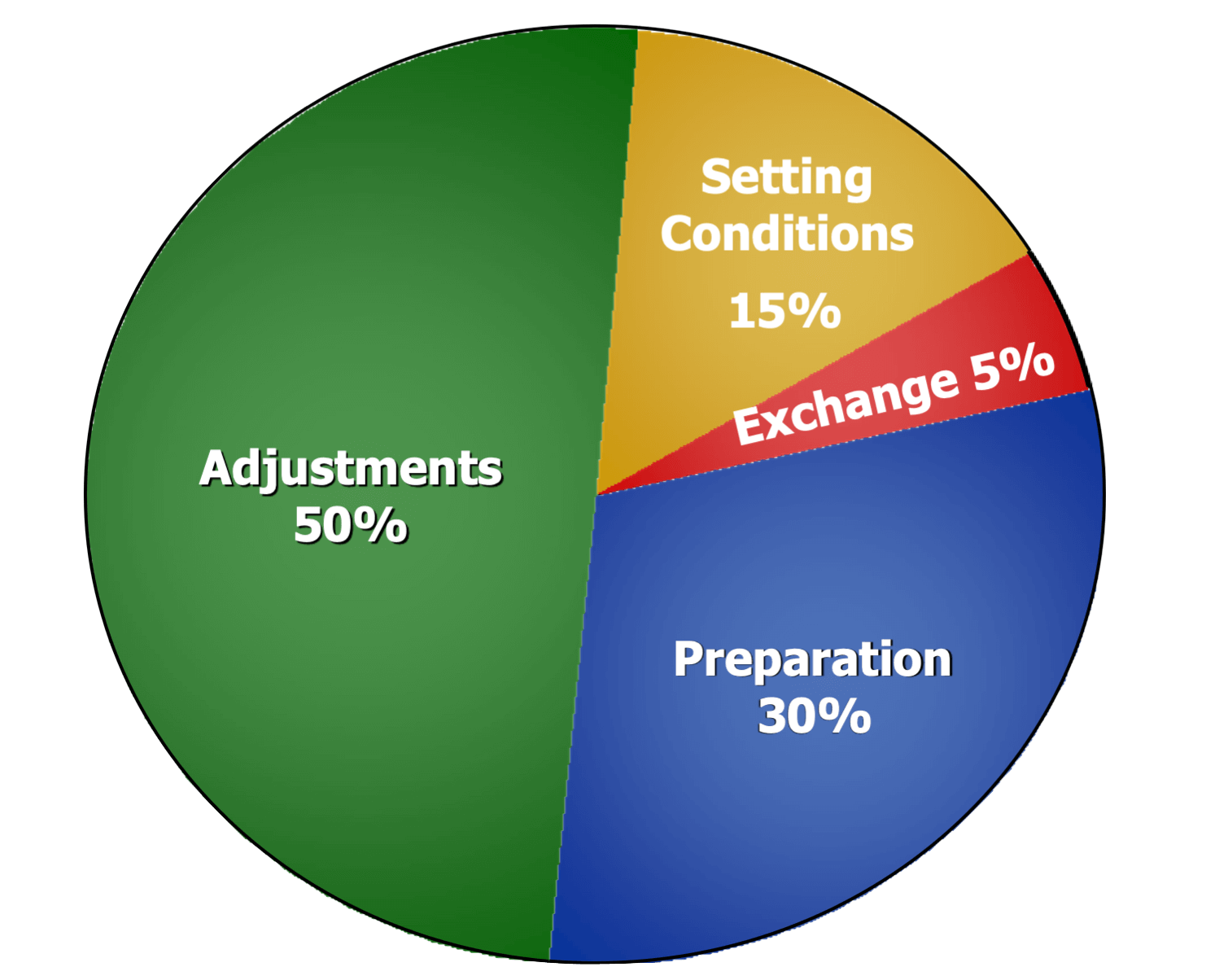
SMED steps diagram
SMED STEPS
1. Document & separate external/internal set up steps
Internal elements = Steps of the process done while the machine is idle
External elements = Steps of the process done while the machine continues to operate
In traditional setup operations, internal and external setups are confused, the first step is to clarify the steps.
You have to involve everyone concerned with this project.
- Study actual conditions on the shop floor by interviewing workers.
- Operators have intimate knowledge of the process, the machine, and their job.
- They will be more willing to accept new rules and procedures if they helped set them up.
Document the Actual (Live) process Setup, go and watch it throughout.
Also, video recording allows workers to review and explain their activities.
2. Transform Internal setup steps into externals
After watching the entire changeover process and establishing which step is done internally and externally, you have to transform as many internal elements as you can in external elements (to be while the machine continues to operate).
Ways to convert Internal to External Setup:
- Re-examine internal events from Step 1 and verify that they are actually internal.
- Convert any internal setup events to external setup events using focused, engineered methods.
Operations that are now performed as internal setup can often be converted to external setup by re-examining their true function. It is extremely important to adopt new perspectives that are not bound by old habits.
You know the saying: THINK OUTSIDE THE BOX, do it!
3. Streamline internal events (Simplify, Reduce, Eliminate)
Streamline Internal Setup by:
- Simplifying Movement
- Reducing Movement
- Eliminating Movement
4. Eliminate adjustments internal to the setup
The frequency and length of test runs and adjustment procedures depend on the skill of the setup engineer. The greatest difficulties in a setup operation lie in adjusting the equipment correctly.
The large proportion of time associated with trial runs derives from these adjustment problems. If we want to make trial runs and adjustments easier, we need to understand that the most effective approach is to increase the precision of the adjustments (measurements and calibrations).
Results
Of course, we are all here because we expect results, right?
You will be surprised by how many wastes you can reduce or eliminate from the changeover process, whether it’s a lack of needed materials, a lack of organization, technical matters, or others.
SMED has been proven extremely efficient in reducing the change over time, but of course, you need an involved team focused on continuous improvement.
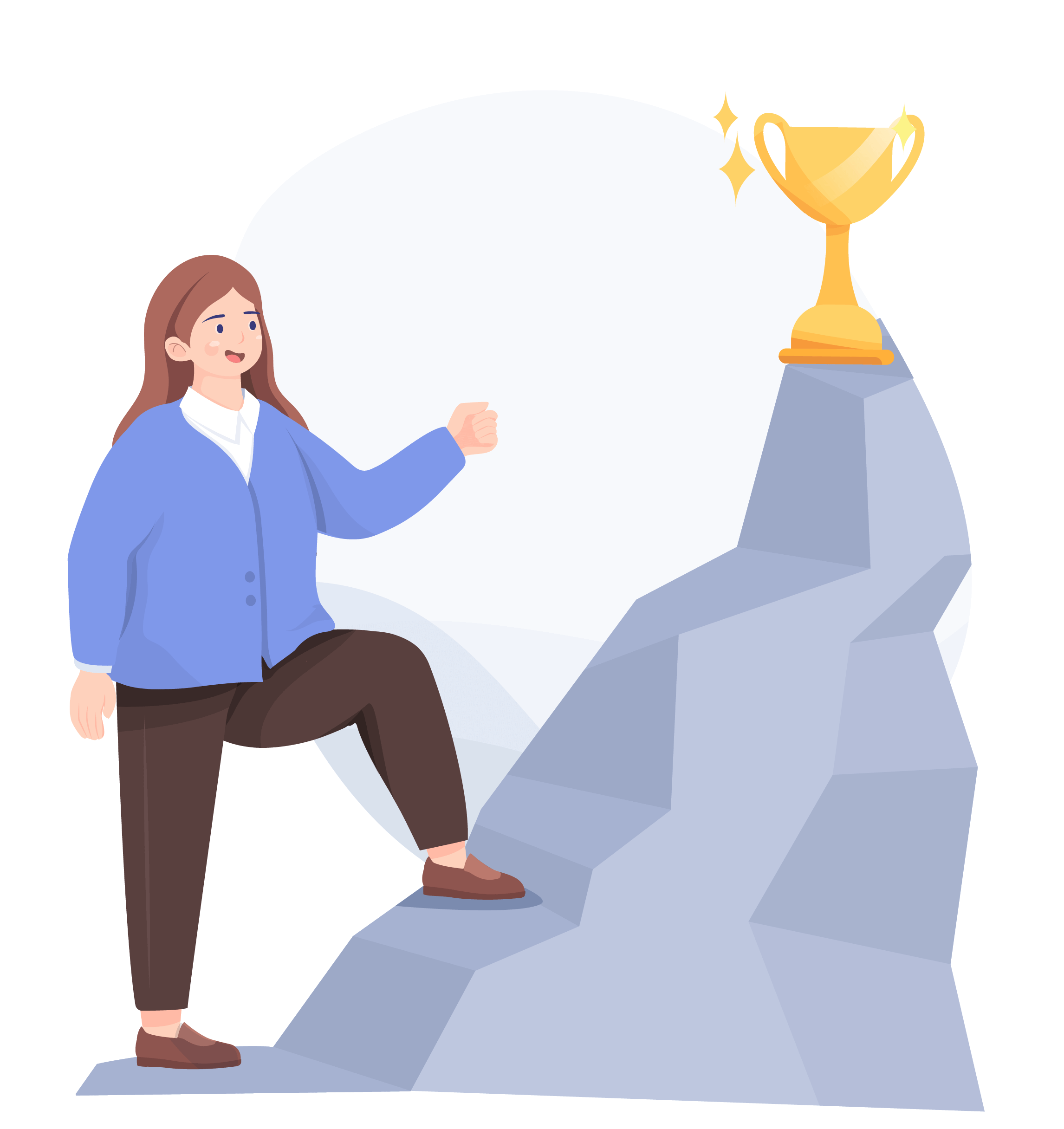
Conclusion
Managers who are responsible for production must recognize that the proper strategy is to make what can be sold, SMED makes it possible to respond quickly to fluctuations in demand.
Setup changes should allow defect-free products to be produced from the very start. It makes no sense to speed up a setup operation without knowing when quality products can be turned out.
The ideal setup change is no change at all. As long as setup changes are necessary, however, they should be designed to be performed with a ‘one-touch’ motion.
It is important to cut setup times, diminish lot sizes, and even loads simultaneously; no more than partial success can be expected with shortened setup times alone.