Have you ever imagined a system without waste and only value-added?
First of all, what is Value Added?
Let’s cover what a process is formed out of:
- Value Added – A value-added activity is any action made that increases the benefit of a product or service to a customer
- Non Value Added – Activities that consume resources, but does not add value to the product or service
- Necessary Non-Value Added Activities – Activities that do not add value to the product or service, but are currently necessary. These are a bit harder to identify.
- Business Value Added – A change made to the product or service which is necessary for future steps but is not noticed by the final customer.
- Machinery Value Added – is any process executed by a machinery that increases the benefit of a good or service to a customer.
What should we concentrate on?
The Yamazumi Chart aims to identify it’s three enemies:
- Muda (waste) – Overproduction, Waiting, Non-used Talent, Transport, Inventories, Defects, Motion, and Over-processing
- Muri (overburden) – When machines or operators are utilized for more than 100% to finish their tasks, they are overburdened.
- Mura (unevenness) – variation of cycle times for different operators or variation of the product demand
These are found in both manufacturing and office processes and it is really important to eliminate them to have a clean process and better productivity.
The most common mistake that is extremely often made is looking only for Muda (waste), without taking into consideration the balance between people (overloading and overburdening)
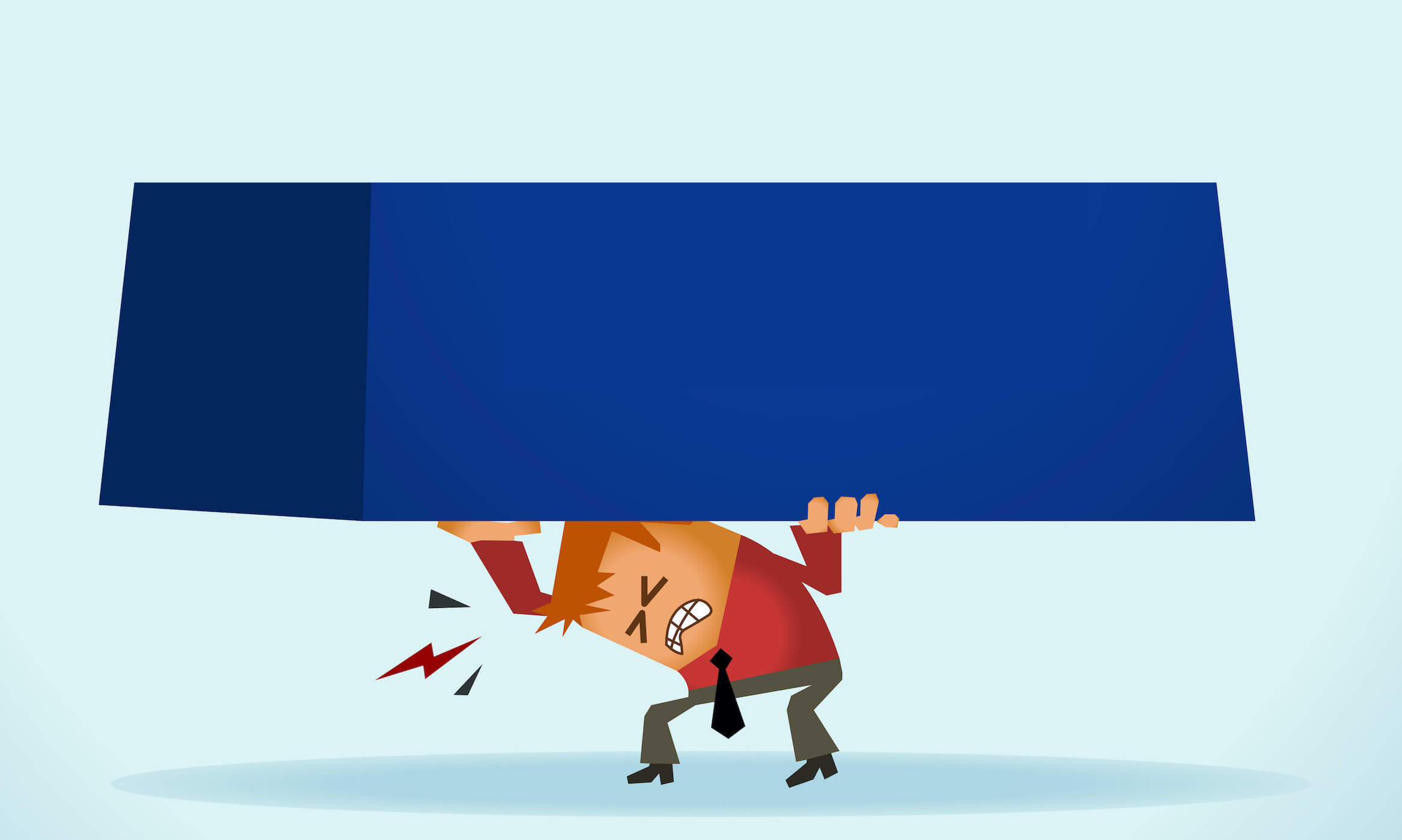
Yamazumi – how do we start?
I think any Plant Manager has dreamed about a no-waste process with excellent productivity, happy employees, and a healthy company.
Of course, this is extremely hard to achieve, and there will always be room for improvement but let’s see how the Yamazumi Chart helps in Lean Manufacturing.
Don’t forget that 5S has a big impact and is mandatory in reducing Muri, Muda and Mura.
It reduces waste
Wasted time is wasted money, and of course, no organization wants to waste money if this can be avoided. The Yamazumi Method helps solve this problem, but of course, it implies dedication from management.
The Yamazumi chart helps see each step of each process, each individual step that the operator or machinery does.
You have to take one process and observe (take notes) every step, timing it to make the Yamazumi Chart.
After that, you can separate the steps, marking which one adds value and which doesn’t to finish the Yamazumi Chart.
After the process has been observed and timed, the chart can be formed, therefore, and the team can observe which step does not add value and can be eliminated or reduced.
Here you have a Yamazumi chart formed for 5 stations:
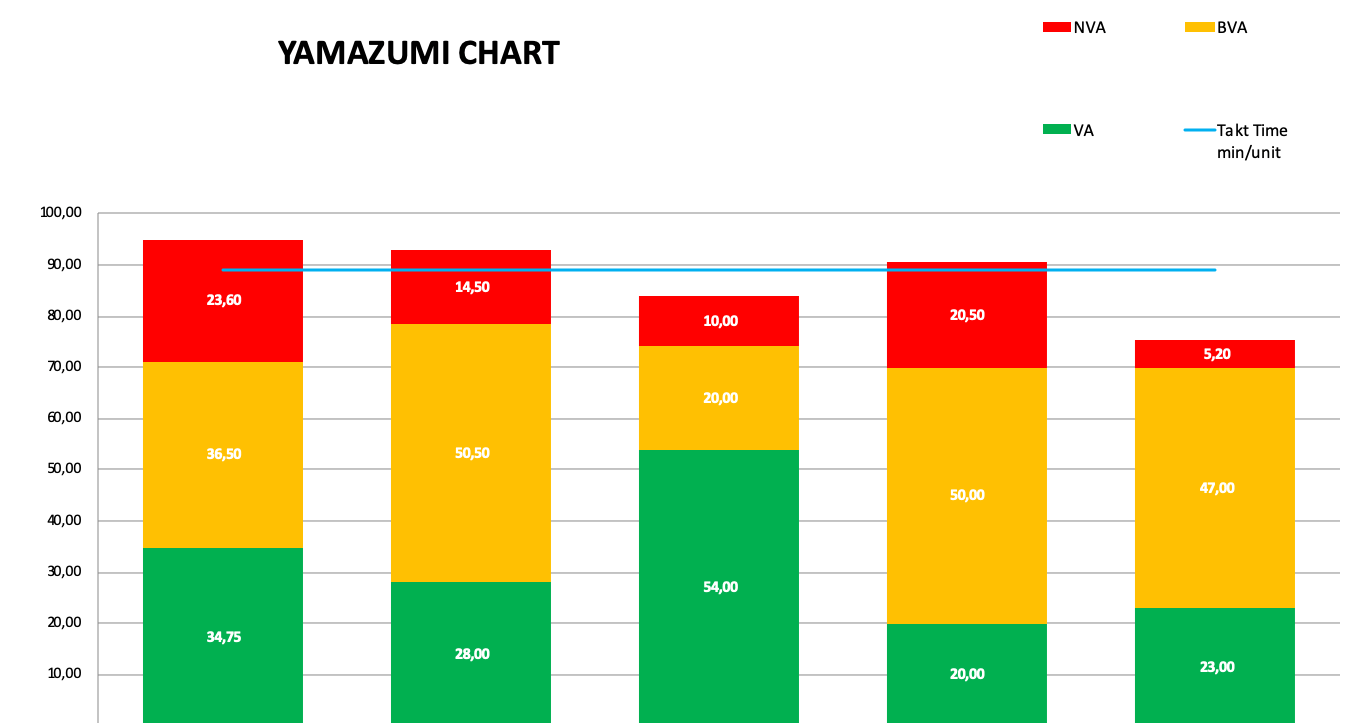
Yamazumi chart formed before any changes have been made
You can see the whole process better
After you have the Yamazumi chart formed you can see the whole process, involving each and every step individually and you can rearrange it as you want. (technically approved) This too can lead to reducing a lot of waste, especially useless movement.
Removing Mura, Muri, and Muda, gives you a better organized process with less wasted time and increases productivity.
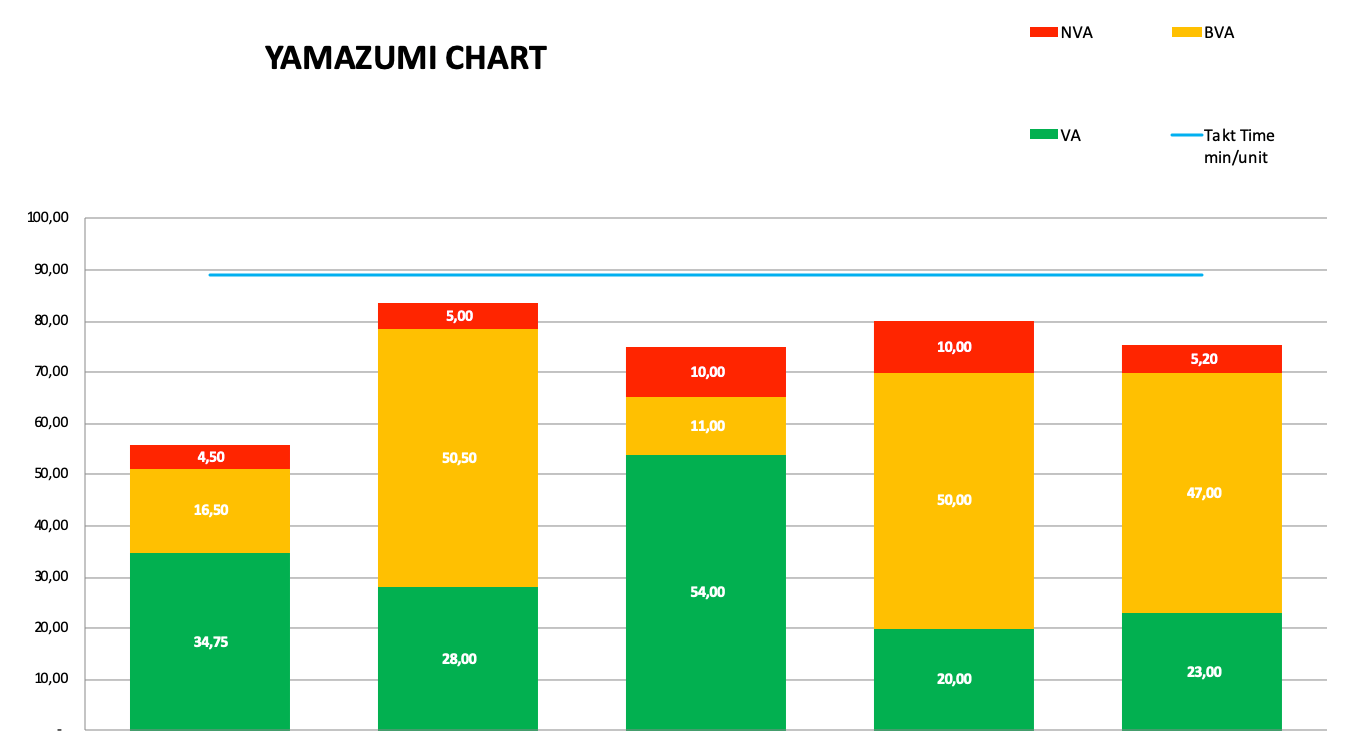
Yamazumi chart after eliminating waste
Conclusion
The Lean mindset is very important in developing good habits in a company. To continuously improve, the management has to be involved in continuously seeking improvement and coaching others to do the same.
The Yamazumi chart works very well in a Manufacturing Company, but it needs constant support from top management.