Why this workshop?
To have stable and reliable equipment is the base for operational excellence.
We shared 3 days with participants from different plants, to understand the TPM management model, and how to implement it in their plants in order to attain a management system that aims to improve the operational availability, while enabling the team work between functions like manufacturing, engineering, quality and maintenance.
We have maintenance & operations managers from companies like Honeywell, VCST, Celestica, Hammerer Aluminium Industries, Hella, among others.
Total Productive Maintenance (TPM) has been introduced recently as a mandatory requirement for the IATF 16949:2016 norm, in order to have a formal system of maintaining and improving the integrity of equipment and its impact to the quality of the processes.
Workshop Highlights:
- We reviewed the 4 Pillars and 12 items of the TPM Management.
- We performed exercises direct on the processes of the plant
- We worked in teams with pilot equipments
- We showed case examples of TPM implementation in Toyota and other companies
The TPM Model
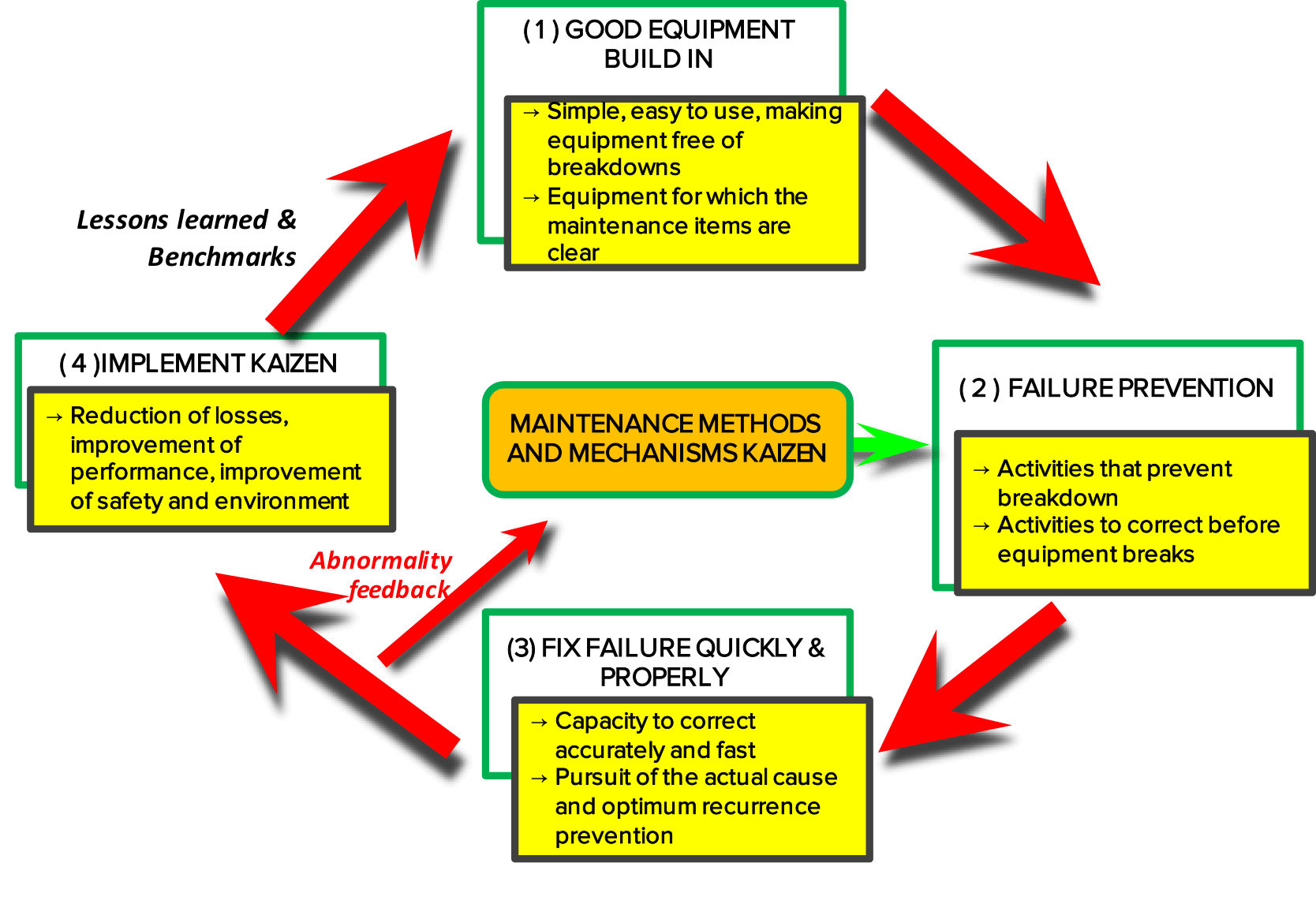